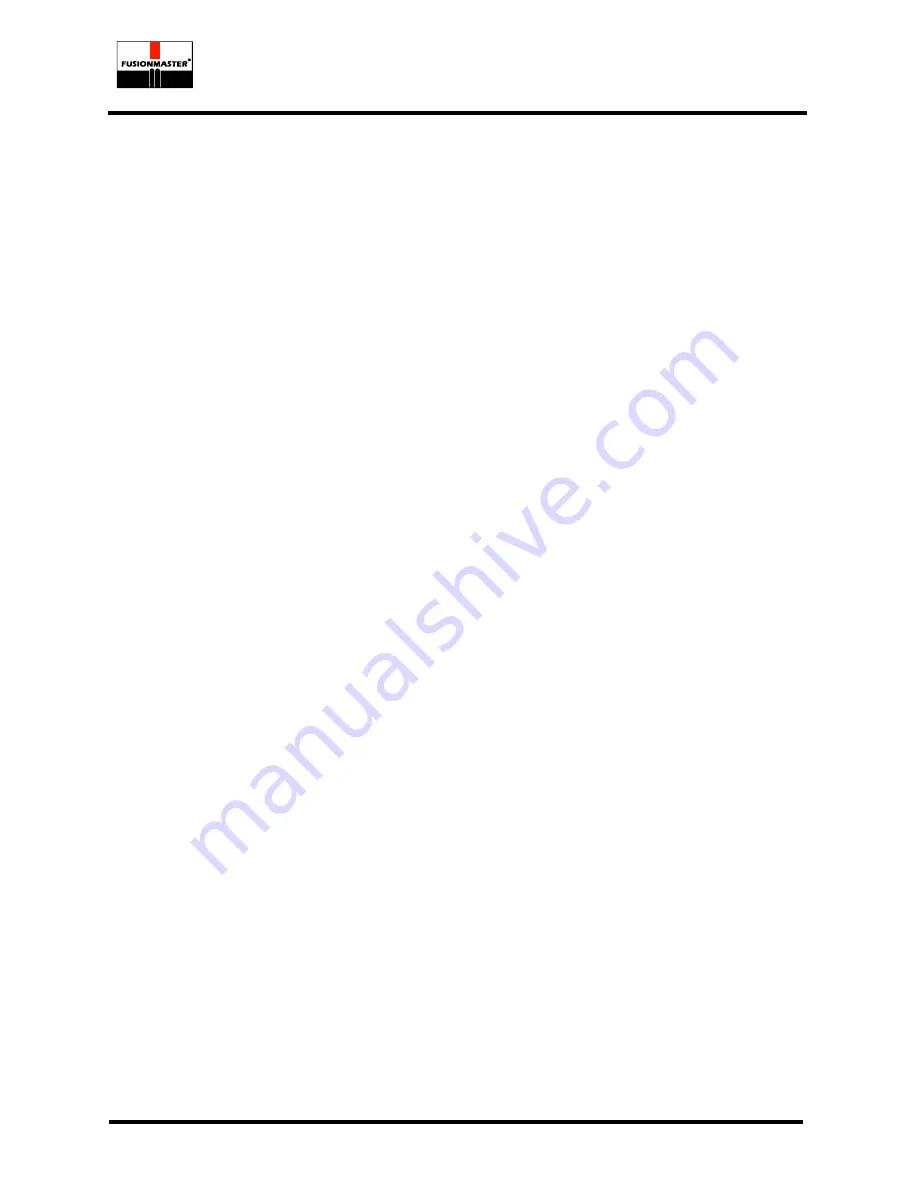
HF225 manual hydraulic butt welder
Simply Better.
Simply Better.
Simply Better.
Simply Better.
FUSIONMASTER®
and
DIXON
®
are registered trademarks of Dixon Industries Pty. Ltd.
©August 2002
Revised August 2013
Page 7
Move the pipe ends apart and place the facing machine between the pipe faces. Ensure the facer
body is securely hooked on to both guide shafts as this will ensure the facer sits square to the
frame and parallel with the clamps.
Start the facer rotating. Move the pipe ends into contact with the facer and apply the minimum
pressure necessary to achieve cutting until a continuous shaving of plastic is simultaneously
produced from both sides of the facer.
Caution:
To maximise drill and facer drive life, operate the drill at low speed (for maximum
torque), and do not apply excessive carriage pressure – e.g. never exceed 1,000 kPa
more than drag.
On completion of facing, reverse the pipe carriage away from the facer then stop facer rotation.
This prevents a step being produced in the faced ends. Raise the facer up and fully out of the
machine.
3.5.
Re-Check Pipe Alignment
Clear away all plastic cuttings without contaminating the pipe ends.
Do not touch the cut surface
or re-clean it
. Move the pipe ends together and re-check pipe alignment (maximum allowable
misalignment is 10% of wall thickness).
Always re-face the pipe ends if it becomes necessary to rotate the pipe in the clamps after initial
facing.
3.6.
Bead Up
Extend the heater rest bars through the left clamp into the weld zone ready to support the
heater plate.
Check the heater plate temperature before commencing each joint in case there has been any
failure of the power supply or temperature controller.
Place the heater plate between the pipe faces.
Move the carriage to bring the pipe faces into contact with the heater plate. Increase pressure to
the predetermined “bead-up” pressure.
Maintain pressure until an initial bead has formed completely around the pipe circumference on
both sides of the heater plate. The bead up time is variable, and is influenced by weather
conditions and pipe dimensions.
Caution:
Ensure the heater handle is NOT standing vertically above the plate or dangerous
overheating may occur. Do not allow the electric cord to rest on the hot plate.
3.7.
Heat Soak
After bead up, reduce the pressure down to the drag pressure to maintain a slight positive
pressure between the pipe and the heater for the heat soak period. Failing to reduce pressure
forces hot plastic out of the joint zone and could lead to a weld failure.
On completion of heat soak time, reverse the carriage direction to “crack” the heater plate away
from the melted pipe, then move the heater plate out of the weld zone as quickly as possible.
(Refer to parameters table for allowable changeover time).
The unique non-stick cloths allow a "peeling off" action as the pipe is cracked away, minimising
adhesion of the melted pipe to the heater.
Remove the heater plate and replace it in the floor stand.
Caution:
Do not allow the heater plate to slide across the pipe ends and distort the melted
surface. Do not contaminate the melted surface in any way.
3.8.
Fusion Cycle
Bring the melted pipe faces into contact with each other immediately to minimise heat loss from
the weld zone. Smoothly build up to the required fusion pressure to avoid squeezing out too
much hot plastic.
Shrinkage will occur as the weld cools allowing the pressure to fall. Voids may also form in the
weld zone. It is essential to operate the hand pump to maintain pressure until shrinkage ceases,