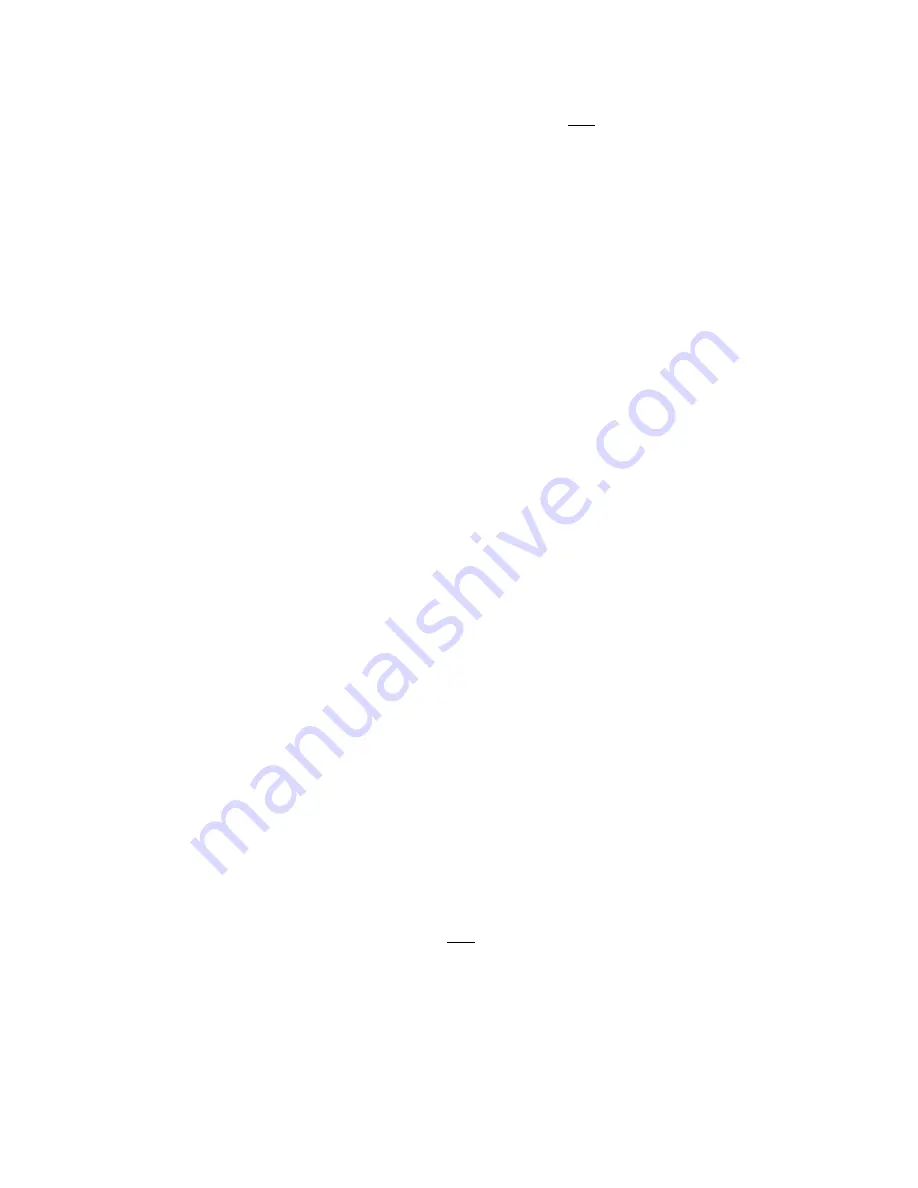
Displacement Follower User’s Manual
Version 1.4, April 19, 2004
IM1008
Page 17
13
Now, move the target or tracking head so that the circle is totally within the light area of the target. See
Figure 15b
.
Adjust the lens aperture or light source for a reading of +20% on the front panel meter. If this reading cannot be
achieved, then the high voltage to the photo tube may need to be adjusted. See
Focusing and System Noise
on page12).
14
Repeat steps 12 and 13 until the light and dark readings are in range.
15
Set the
Light/Operat
e switch to
Operate
.
16
Turn the rear panel
Vertical/Horizontal
switch counterclockwise for vertical axis tracking or clockwise for horizontal
axis tracking. Set the
Target Phase
switch to the type of target to be tracked, light over dark or dark over light.
Note
This switch must be set properly or the normal negative feedback servo action becomes positive and the system
will not work correctly. Refer to Section 4.
17
The meter and output voltage will now indicate the position of the target. (If an equilibrium position is desired with a
corresponding zero reference voltage, then the position of the entire tracking head or the target must be adjusted.).
18
Move the target and observe that the meter deflects, showing target position. With a light-over-dark target, an upward
movement produces a negative voltage; the negative sense of the output voltage is in the direction of the light portion of
the target.
19
If the system does not appear to be locked onto the target, simply waving your hand in front of the lens may fix the
problem. See
Common Problems
on page 21.
20
With lock-on complete, set the filter switch to the lowest cutoff frequency applicable. The filter switch simply places a
low pass RC circuit at the displacement output BNC connectors.
21
You can connect an external monitoring device such as a digital oscilloscope, oscillograph or X-Y recorder, among
others, to the output BNC connectors. Since the output impedance of the 5100 is just under 50 ohms, loading effects by
external instrumentation will be negligible.
Velocity and Acceleration Measurement
The 5100 Control Unit is equipped with differential amplifiers for obtaining the velocity and acceleration of a target. The
position signal has been hard-wired to these amplifiers in series. This causes the vertical displacement signal to be
differential twice, yielding vertical velocity and vertical acceleration signals at the respective outputs.
Various full-scale velocity and acceleration values are determined by the two 8-position time constant selector switches.
The output velocity is equal to the full-scale displacement of the lens divided by the time indicated by the velocity time
constant switch. For example, for a one-inch range of measurement with the
Velocity
selector at 30ms, the full-scale (10V
P-P) velocity output would be one inch (1”) divided by 30 ms, or 33 inches per second at the peak. Standard nomenclature
of the vibration test industry has been used: displacement is read in inches double amplitude; velocity, in inches peak per
second; and acceleration in inches peak per second squared.
If the motion to be observed is varying vertically by 1”, and a 1” range of measurement lens is used, this motion has what is
called a one inch double amplitude (P-P), and the vertical position output of the 5100 would be a 10V P-P. This voltage,
which is proportional to displacement, is fed into the differential amplifier. The differential amplifier has a full-scale output
of 10V P-P which therefore equals the input displacement of 1” double amplitude divided by the
Velocity Time
Constant
selector switch setting of 30ms, and is 33 inches peak per second at the velocity output.
If differentiated again, a 10V P-P signal at the
Vertical Acceleration
output would equal the vertical velocity reading of
33 inches peak per second divided by the acceleration time constant selector setting in seconds, and would be in inches peak
per second squared.