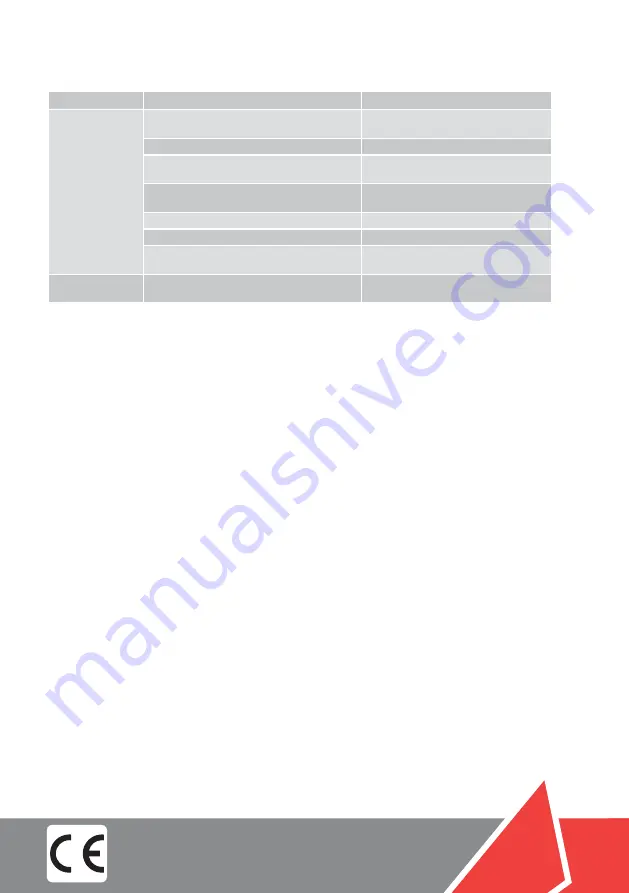
IP2250EN
ASSA ABLOY Entrance Systems AB
Lodjursgatan 10
SE-261 44, Landskrona
Sweden
© ASSA ABLOY
6. Troubleshooting
Problem
Possible cause
Operation
The gate doesn't
open or close.
No power supply.
Check that the mains power supply is
present.
Gearmotor released.
See release instructions.
Photocells interrupted.
Check that the photocells are clean and
operating correctly.
Permanent stop command.
Check the stop command or control
panel.
Faulty selector.
Check the selector or control panel.
Faulty remote control
Check the condition of the batteries.
Electric lock not working
Check the positioning and proper oper-
ation of the lock.
The gate opens but
doesn't close.
Photocells interrupted.
Check that the photocells are clean and
operating correctly.