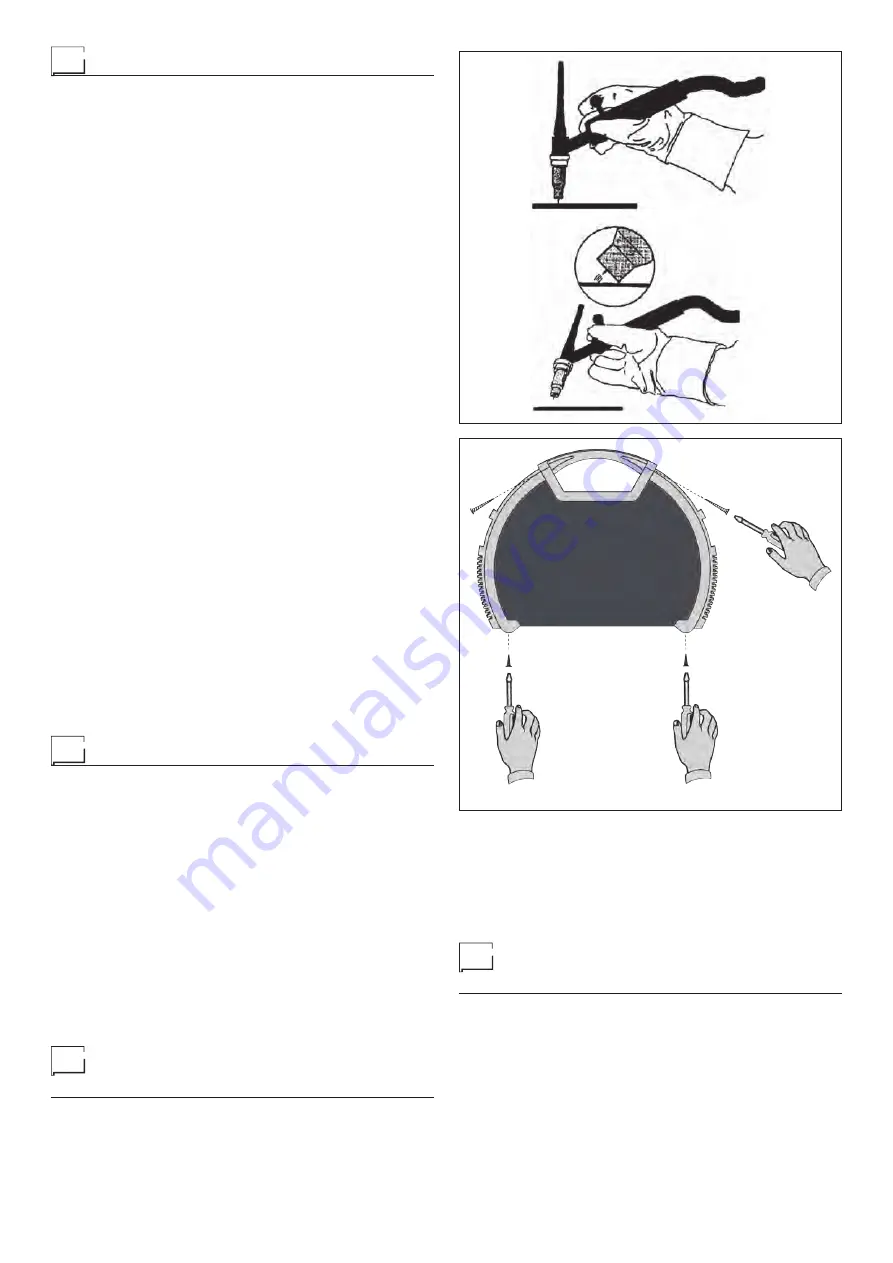
5
TIG welding (Fig. C)
TIG welding melts the metal of the workpiece, using an arc struck
by a tungsten electrode.
The fusion bath and the electrode are protected by gas (Argon).
This type of welding is used to weld thin sheet metal or when el-
evated quality is required.
1) Connecting the welding cables:
•
Connect one end of the gas hose to the gas connecter on
the TIG torch and the other end to the Argon cylinder and
open it.
•
With the machine switched off:
- Connect the earth cable to the snap-on connector marked
+ (positive).
- Connect the relative earth clamp to the workpiece or to the
workpiece support in an area free of rust, paint, grease,
etc..
- Connect the TIG torch power cable to the snap-on con-
nector marked - (negative).
2) Adjust the welding current using the potentiometer (Pos. 2,
Fig. A).
3) Turn the process selector (Pos. 3, Fig. A) to the TIG position.
4) Start the welding machine by selecting Pos. 1 on the line
switch (Pos. 1, Fig. A).
5) The green LED (Pos. 6, Fig. A) shows that the power supply
to the welding machine is on, and it is ready to work.
6) Adjust the gas flow by manually turning the valve on the TIG
torch.
7) The “Lift” function strikes the arc when the TIG torch electrode
comes into contact with the workpiece and is then removed
(see Fig. D).
8) Carry out TIG welding.
PART TO BE WELDED
The part to be welded must always be connected to earth in order
to reduce electromagnetic emission. Much attention must be af-
forded so that the earth connection of the part to be welded does
not increase the risk of accident to the user or the risk of damage
to other electric equipment. When it is necessary to connect the
part to be welded to earth, you should make a direct connection
between the part and the earth shaft. In those countries in which
such a connection is not allowed, connect the part to be welded
to earth using suitable capacitors, in compliance with the nation-
al regulations.
Maintenance
WARNING: Before carrying out any inspection of the inside of the
generator, disconnect the system from the supply.
SPARE PARTS
Original spare parts have been specially designed for our equip-
ment. The use of non-original spare parts may cause variations in
performance or reduce the foreseen level of safety. We decline all
responsibility for the use of non-original spare parts.
GENERATOR
As these systems are completely static, proceed as follow:
•
Periodic removal of accumulated dirt and dust from the inside
of the generator, using compressed air. Do not aim the air jet
directly onto the electrical components, in order to avoid dam-
aging them.
•
Make periodical inspections in order to individuate worn cables
or loose connections that are the cause of overheating.
The pointing out of any difficulties
and their elimination
The supply line is attributed with the cause of the most common
difficulties. In the case of breakdown, proceed as follows:
1) Check the value of the supply voltage.
2) Check that the power cable is perfectly connected to the plug
and the supply switch.
3) Check that the power fuses are not burned out or loose.
2000HA39
FIG. D
FIG. E
4) Check whether the following are defective:
•
The switch that supplies the machine.
•
The plug socket in the wall.
•
The generator switch.
NOTE: Given the required technical skills necessary for the repair
of the generator, in case of breakdown we advise you to contact
skilled personnel or our technical service department.
Procedure for welder assembly
and disassembly
Proceed as follows (Fig. E):
•
Unscrew the 4 screws holding the front and back panels.
•
Unscrew the 2 screws holding the handle.
•
Proceed the other way round to re-assemble the welder.