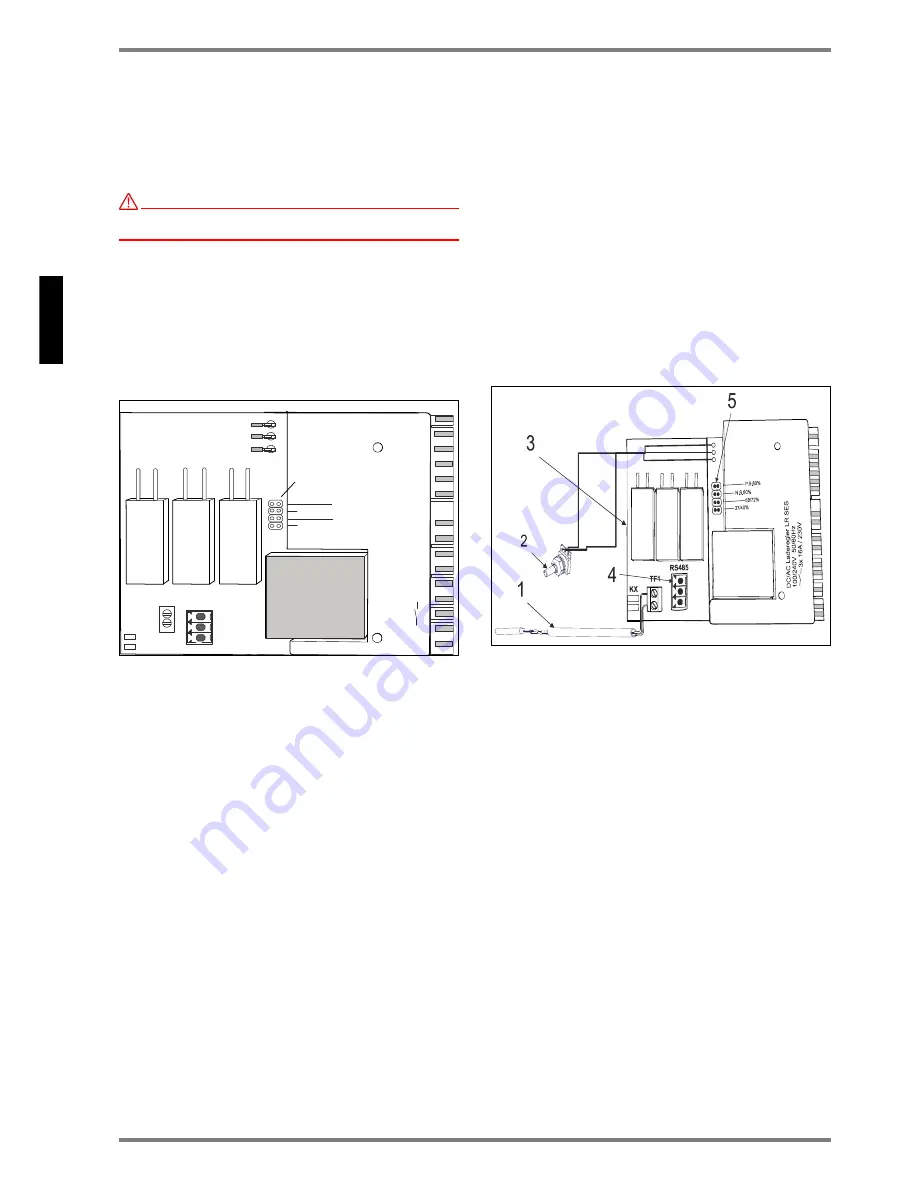
www.dimplex.de/en 459462.66.01 · 10/14/B
EN-37
E
n
g
li
s
h
FSR 15-35 / FSR 15-35 GS / FSR 15-35 GW
7 LR SES Charge Controller
7.1 Operation using a standard charge control system
DC control signal: 0.91 to 1.43 V DC
Connect charge control cable to terminals A1+ and A2- on the
storage heater.
ACHTUNG!
Ensure you connect the cables to the terminals with the
correct polarity!
AC control signal 230V AC
Connect charge control cable to terminals A1~ and A2~ on
the storage heater.
On ED system charge control systems, the storage heater's
charge controller can be operated at 80%, 72%, 68%, 40%
and 37%. The factory setting is for 80% ED systems.
If the storage heater is operated on other ED systems, then
the program jumper (A) must be plugged in at the appropriate
position.
Fig. 34: Charge regulator with program jumper (A) ED signal
7.2 Setting - reaction to fault
The factory setting is for the storage heater to be pro-
grammed for "positive reaction to fault" (known also by its
German abbreviation, "P.S."). This means that, if the control
current fails, e.g. due to a defect in the charging control de-
vice, the equipment charges up to maximum heat storage.
If charging is not required, if this fault occurs, the program
jumper (B) on the charge regulator can be set to "negative re-
action to fault"(known also by its German abbreviation, "N.S.").
Programming to set a "negative reaction to fault" can only be
carried out during operation on suitable charging control de-
vices. In addition, an 80% ED signal is necessary in the case
of AC charging control devices.
7.3 Operation on SES Smart Eco System
Quantum storage heaters can also be controlled using an in-
telligent home automation "Smart Eco System". This also en-
ables the system to be operated with minimum power con-
sumption.
The following components are necessary in this case: an
SES KM1 communication module for each storage heater, a
special radio room temperature gauge (RT.101EO) per room,
and an FG 101 EO external sensor and SES ZE central unit
per system.
For more detailed information, please refer to the relevant op-
erating instructions.
7.4 Performing a functional test on the charge con-
troller
Description
The charge controller integrated in the storage heater is an
electronic two-point regulator which switches 230V~ to the
heating elements, depending on the:
core temperature,
charging control signal (to A1+ and A2- or A1~ and A2~),
load activation (to L-SH, N-SH), and
the setting on the potentiometer,
via the 3 relay outputs.
The core temperature (heat storage) is recorded using a plat-
inum residual heat gauge. The residual heat gauge's resist-
ance value at room temperature equals: R20°C = 107 Ohm.
Fig. 35:Charge controller components
1 - Residual heat gauge
2 - Intensity setter (potentiometer)
3 - Switch relay for heating elements
4 - Service port
5 - ED signal program jumper
Prerequisites
A charge control cable must not be connected to the ter-
minals A1+ and A2- or A1 and A2~.
The functional test must be performed on the storage
heater when it is cold.
The program jumper on the charge controller must be set
to "PS" 80% (factory setting).
Mains voltage must be present on terminals "L-R,N-R"
and "L-SH, N-SH" (terminal screws must be tightened
up).
If an SES KM1 communication module is present, it must
be unplugged.
Functional test
Turn the potentiometer anticlockwise until it stops on the left:
The heating elements must not be affected by the
controls!
Turn the potentiometer clockwise until it stops on the right:
The heating elements must be affected by the controls!
37/40%
TF1
KX
R
S
4
8
5
68/72%
P.S.80%
N.S.80%
D
C
/A
C
L
a
d
e
re
g
le
r
L
R
S
E
S
1
0
0
/2
4
0
V
5
0
/6
0
H
z
3
x
1
6
A
/
2
3
0
V
A