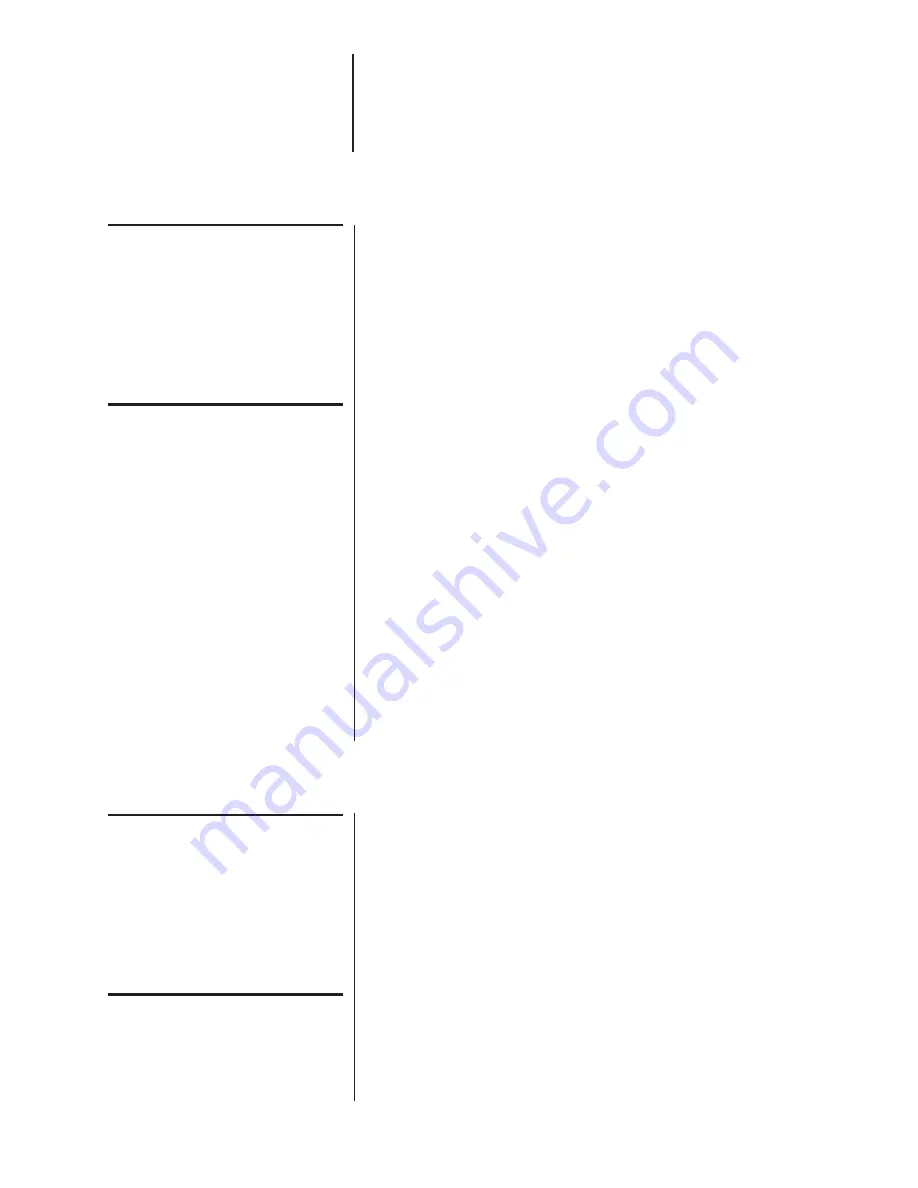
9
AP Dynamometer Service Manual
9.
Install the bezel assembly to the housing with the four 6-32 x ¼ pan
head bezel screws.
10.
Reinstall shackles and/or hook assemblies.
11.
Calibrate per procedures in the
Calibration
section of this manual.
1.
Remove the four 6-32 x ¼ pan head bezel screws holding the bezel to
the pan.
2.
Lift off the bezel, crystal, and max hand assembly.
3.
Remove the pointer from the gauge movement shaft with a pointer
puller (P/N 29945-0023).
4.
Remove the four 10-32 x 3/8 socket head cap screws and flat washers
from the two angle brackets holding on the dial pan cover plates.
5.
Remove two ¼-28 x ¾ socket head screws, flat and lock washers from
each of the ¼" thick side plates. The left plate contains the serial
number and zero adjustment access hole. Leave the thin cover plates
attached to these two plates. Note that the end of the two spacer
plates are flush to the end of the ¼" thick plates.
6.
Remove two ¼-28 x ½ socket head screws (no washers) from the ½"
thick side plates. The left plate holds the zero adjust assembly. The
right plate holds the gauge movement bracket assembly. Leave the
thin cover plates attached to these two ½" thick plates.
7.
Note that the pressure bar is located with the cutout away from the you
and that the distance from the right end to the notch is 3 5/16". The
distance from the left end to the notch is 3 9/16". This is important for
correct assembly.
8.
The shackles are each fitted with two needle bearings. Remove the
bearings with a mechanical press with the plunge ram within ½ degree
of the bearing hole axis. Under no circumstances should the bearings
be removed by impact. Take care that the plunger does not contact the
sides of the bearing hole as you push out the bearing.
1.
Reinsert the bearings with a mechanical press with the plunge ram
within ½ degree of the bearing hole axis. Insure that the bearing hole,
bearing outer surface and ram are all free of debris, dirt or particles.
To facilitate bearing installation, an anti-seize compound such as Fel-
Pro C5-A may be used, provided any excess lubricant is wiped off after
bearing installation. Carefully insert the bearings one at a time, insuring
that the bearing remains properly aligned to the bearing hole axis.
Reverse sides to install the second bearing. Always assembly the
bearing with the stamped end against the shoulder of the pressing tool.
2.
Again, note that the pressure bar is located with the cutout away from
the assembler and that the distance from the right end to the notch is
3 5/16". The distance from the left end to the notch is 3 9/16".
3.
Install the left plate with the zero bracket to the pressure bar with the
two ¼-28 X ½ socket head screws (no washers). Align this plate
parallel to the pressure bar and torque.
Separation of Pressure
Bar and Gauge
Movement on 10"
Diameter Units from
30,000 -100,000 lb
(15000-50000 kg)
Capacities
Reassembly of Pressure
Bar and Gauge
Movement on 10"
Diameter Units from
30,000 -100,000 lb
(15000-50000 kg)
Capacities
It is helpful to be consistent in
the location of the pressure
bar. In the directions at right
the dial pan is face up with the
plate containing the serial
number to the left and facing
you.