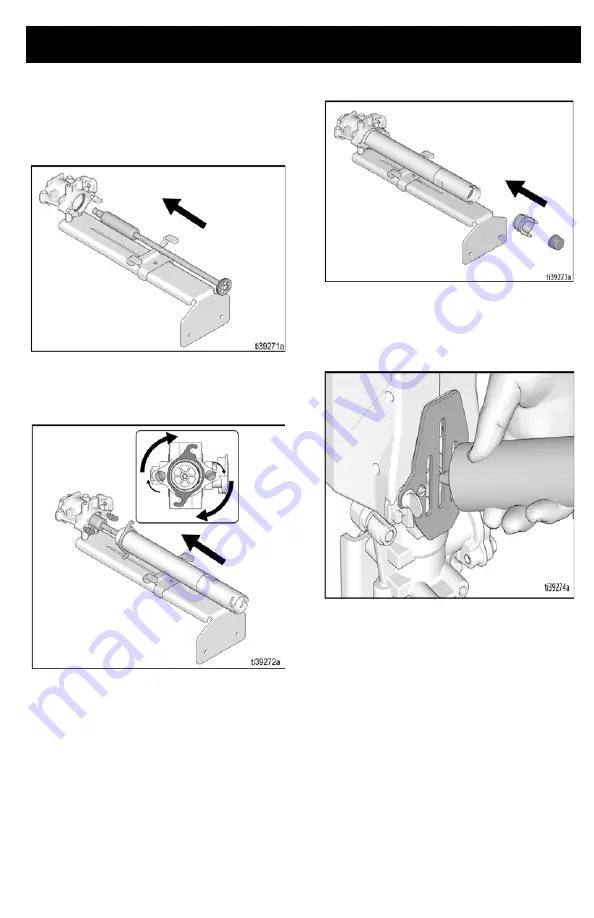
Cleaning
3A8110C
23
Pump Re-assembly
1.
Carefully insert piston rod assembly into
pump housing. Be careful not to damage
the throat seal.
2.
Slide cylinder onto piston, rotate onto
thumb screws. Hand tighten thumb
screws.
3.
Re-assemble inlet housing and filter.
4.
Re-assemble Power Head, see
5.
Apply Throat Seal Liquid (TSL) into
pump throat.
Содержание Graco PowerFill 3.5 Standard 26B417
Страница 39: ...Graco Information 3A8110C 39 ...