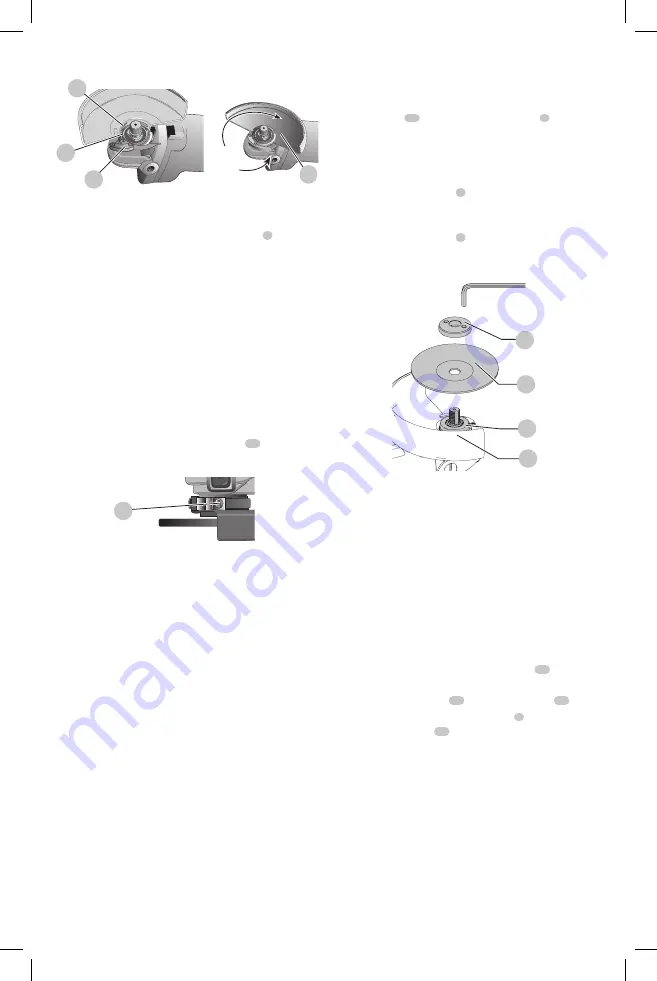
English
8
Fig. C
7
14
15
6
2. Push the guard down until the guard lugs engage and
rotate freely in the groove on the gear case hub.
3. With the guard latch open, rotate the guard
6
into the
desired working position. The guard body should be
positioned between the spindle and the operator to
provide maximum operator protection.
4. Close the guard latch to secure the guard on the
gear case. You should not be able to rotate the guard
by hand when the latch is closed. Do not operate
the grinder with a loose guard or the clamp lever in
open position.
5. To remove the guard, open the guard latch, rotate the
guard so that the arrows are aligned and pull up on
the guard.
nOTE:
The guard is pre-adjusted to the diameter of the gear
case hub at the factory. If, after a period of time, the guard
becomes loose, tighten the adjusting screw
13
with clamp
lever in the closed position.
Fig. D
13
CAUTION:
Do not tighten the adjusting screw with
the clamp lever in open position. Undetectable
damage to the guard or the mounting hub may result.
CAUTION:
If guard cannot be tightened by adjusting
clamp, do not use tool and take the tool and guard to
a service center to repair or replace the guard.
Flanges and Wheels
CAUTION:
Turn unit off and unplug the tool before
making any adjustments or removing or installing
attachments or accessories.
Mounting Non-Hubbed Wheels (Fig. E)
WARNING:
Failure to properly seat the flanges and/or
wheel could result in serious injury (or damage to the
tool or wheel).
CAUTION:
Included flanges must be used with
depressed center Type 27/42 grinding wheels and
Type 1/41 cutting wheels. Refer to the
Accessories
Chart
for more information.
WARNING:
A closed, two-sided cutting wheel guard
is required when using abrasive cutting wheels or
diamond coated cutting wheels.
WARNING:
Use of a damaged flange or guard or fail-
ure to use proper flange and guard can re sult in injury
due to wheel breakage and wheel contact. Refer to the
Accessories Chart
for more information.
1. Place the tool on a table, guard up.
2. Place wheel
17
against the backing flange
3
,
centering the wheel on the raised center (pilot) of the
backing flange.
3. While depressing the spindle lock button and with the
hex depressions facing away from the wheel, thread the
threaded locking flange
4
on spindle so that the lugs
engage the two slots in the spindle.
4. While depressing the spindle lock button, tighten the
threaded locking flange
4
using a Hex wrench.
5. To remove the wheel, depress the spindle lock button
and loosen the threaded locking flange.
Fig. E
4
17
3
1
Mounting Sanding Backing Pads (Fig. A, F)
nOTE:
Use of a guard with sanding discs that use backing
pads, often called fiber resin discs, is not required. Since a
guard is not required for these accessories, the guard may or
may not fit correctly if used.
WARNING:
Failure to properly seat the clamp nut
and/or pad could result in serious injury (or damage
to the tool or wheel).
WARNING:
Proper guard must be reinstalled for
grinding wheel, cutting wheel, sanding flap disc,
wire brush or wire wheel applications after sanding
applications are complete.
1. Place or appropriately thread backing pad
16
on
the spindle.
2. Place the sanding disc
18
on the backing pad
16
.
3. While depressing spindle lock button
2
, thread the
sanding clamp nut
19
on spindle, piloting the raised
hub on the clamp nut into the center of san ding disc
and backing pad.
4. Tighten the clamp nut by hand. Then depress the
spindle lock button while turning the sanding disc until
the sanding disc and clamp nut are snug.
5. To remove the wheel, grasp and turn the backing
pad and sanding pad while depressing the spindle
lock button.
Содержание DWE43840CN
Страница 47: ......