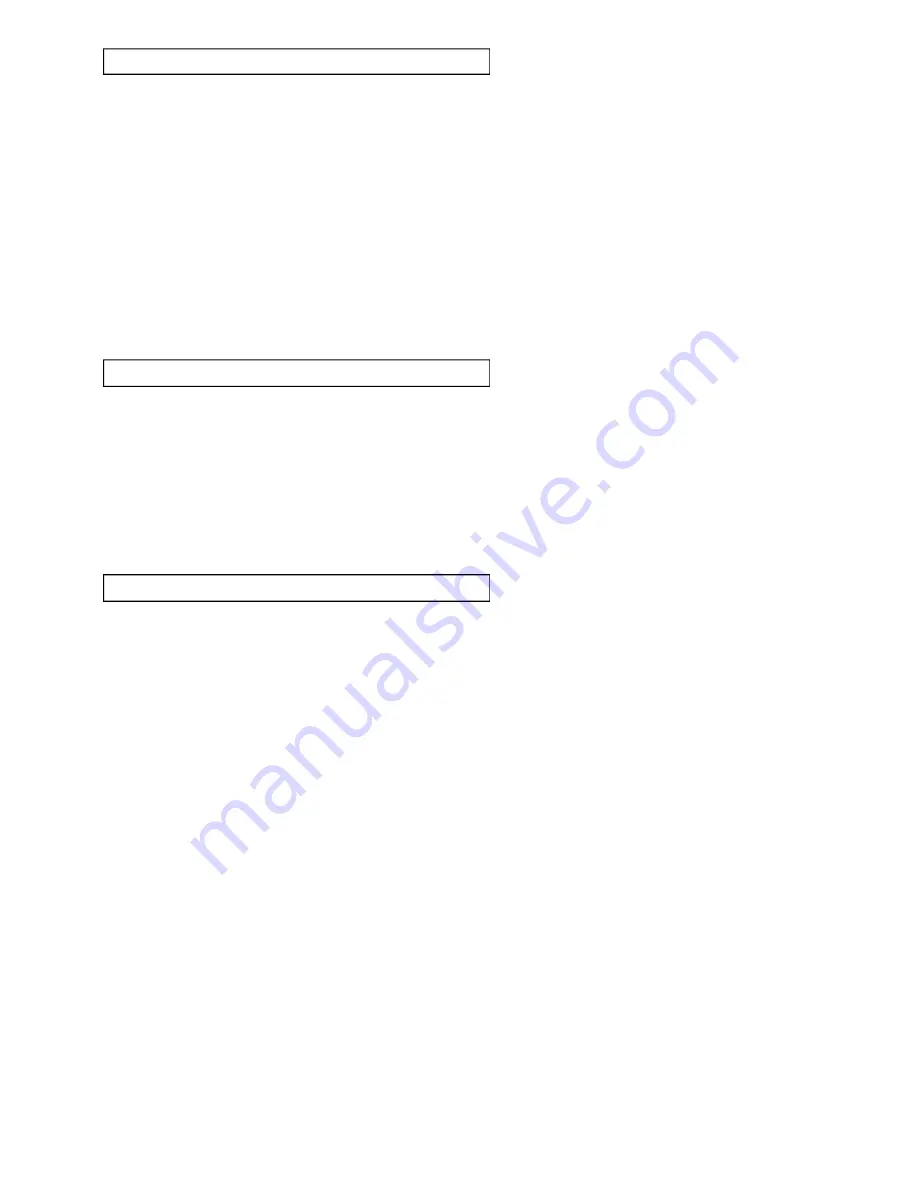
1. Mix, prepare and filter the coating material to be sprayed to the manufacturer’s instructions.
2. Adjust the spray gun controls and pressures before turning on the air and coating material supplies.
2.1
Fan pattern valve (6) marked ‘FAN’ on the gun body
. Turn adjusting screw to fully open position, by turning
counter-clockwise.
2.2
Atomising control valve (6) marked ‘ATOM’ on the gun body.
Turn adjusting screw to fully open position, by
turning counter-clockwise.
2.1
Needle adjustment.
Fully close needle adjusting screw (29), release locknut (28), turn clockwise until resistance is
felt, then turn to the fully open position by turning counter-clockwise ten turns and secure with locknut (28).
3. Regulate the air supply pressure to 4 bar (60 lbf/in
2
) and coating material pressure to 1 bar (15 lbf/in
2
)
4. Turn on air and coating material supplies and test spray by operating control valve. The recommended spray distance is 150
mm (6"). If the finish is too wet, reduce the coating material supply pressure, or turn the needle adjusting screw (29) fully
clockwise then gradually open until the desired pattern is achieved. If the atomisation is too coarse increase the air
pressure. The spray width can be reduced from fan to round by turning fan adjusting valve (6) marked ‘FAN’ clockwise.
Note.
If both ‘FAN’ and ‘ATOM’ valves (6) are closed the air supply operates the cylinder only and will allow coating material to
be jetted from the nozzle.
5. To prevent accidental discharge of coating material, always turn off and release pressure when the gun is not in use.
Flushing the system:
1. Turn off coating material supply and relieve pressure.
2. Close both air valves (6) marked ‘FAN’ and ‘ATOM’.
3. Replace coating material with a suitable solvent, reduce pressure and turn on supply.
4. Remove air cap, trigger the gun by operating the control valve. Flush system until clean.
Clean air cap by immersing in solvent, brush or wipe clean. If any holes in the air cap are blocked use a toothpick or broom
straw to remove the obstruction. Never use a steel wire or hard implement which will damage the air cap and result in a
distorted pattern.
Lubrication:
Daily lubricate with light mineral oil the valve stems (7) and needle seal (14) through holes in seal retainer (16).
Occasionally coat the gun body cylinder section and springs (25 & 26) with mineral based grease.
Note:
Order numbers shown in parts list for figure 1 with suffix ‘-K5’, etc. at the end of the order No. indicates a kit of parts.
Example
AG-12-K5
is a kit of five seals.
Nozzle (4) or Baffle (5)
Remove parts (1, 2, 3, 27, 28, 29, 25 and 26) unscrew nozzle (4) and pull baffle (5) out from body.
Caution:
Do not twist baffle (5) when removing from the gun body as this will bend the locating pin in the gun body.
Replace any worn or damaged parts. Reassembly, position baffle (5), ensure gun body locating pin is engaged in the narrow
slot in the baffle. Replace nozzle (4) and tighten. Recommended torque 13-14 Nm (115-125 lbf in). Fit parts (25, 26,27, 28, 29,
1, 2 or 3).
Seal (9)
Caution:
Always turn valve (7) fully counter-clockwise before fitting or removing valve assembly (6) from gun body.
Remove valve assembly (6) from gun body. Remove parts (13, 12, 11, 10 and 9). Lubricate seal (9) with mineral oil and
replace parts (9, 10, 11, 12 and 13). Refit valve assembly (6) to gun.
Seal (14), (SEE SAFETY WARNINGS UNDER MISUSE), and ‘0’ ring (15)
Remove parts (29, 28, 27, 26 and 25). Withdraw needle and piston assembly, insert a wide blade screwdriver into the slot and
unscrew seal retainer (16) and remove seal (14). Lubricate new seal (14) with mineral oil, replace ‘0’ ring (15), place seal (14)
into retainer (16) and screw into gun body. Tighten retainer (16) sufficiently to seal but not to impede free needle (17)
movement. Lightly coat seal (21) and ‘0’ ring (18) with mineral based grease. Fit needle and piston assembly into gun body.
Reassemble parts (29, 28, 27, 26 and 25).
Needle (17)
Remove parts (29, 28, 27, 26 and 25) and withdraw needle and piston assembly. Unscrew nut (24), remove needle (17) and
washer (23). Replace needle (17), position washer (23) and tighten nut (24). Adjust needle seal (14) with retainer (16)
sufficiently to seal but not to impede free needle (17) movement. Lightly coat seal (21) and ‘0’ ring (18) with mineral based
grease. Fit needle and piston assembly into gun body. Reassemble parts (29, 28, 27, 26 and 25).
Piston seal (21) and ‘0’ ring (18)
Remove parts (29, 28, 27, 26 and 25) and withdraw needle and piston assembly. Remove parts (18, 19, 20, 21). Replace seal
(21) and ‘0’ ring (18). Reassemble parts (18, 19, 20, 21) see figure 3 for the direction of circlip bow. Lightly coat seal (21) and ‘
0’ ring (18) with mineral based grease. Fit needle and piston assembly into gun body. Reassemble parts (25, 26, 27, 28 and
29). Adjust screw (29) and secure with locknut (28).
Connectors (30)
Remove connector (30) and clean threads in gun body. Apply a medium strength thread locking/sealing compound to the
external threads of the new connector. Screw into gun body and tighten. Recommended torque: 14 Nm (125 lbf in).
REPLACEMENT OF PARTS
(see figures 1 and 3)
PREVENTIVE MAINTENANCE
OPERATION
3
SB-E-2-782 – © ITW LTD 1994
Содержание AGF-508
Страница 7: ...SB EE 4 205 ITW LTD 1994 7 NOTES...