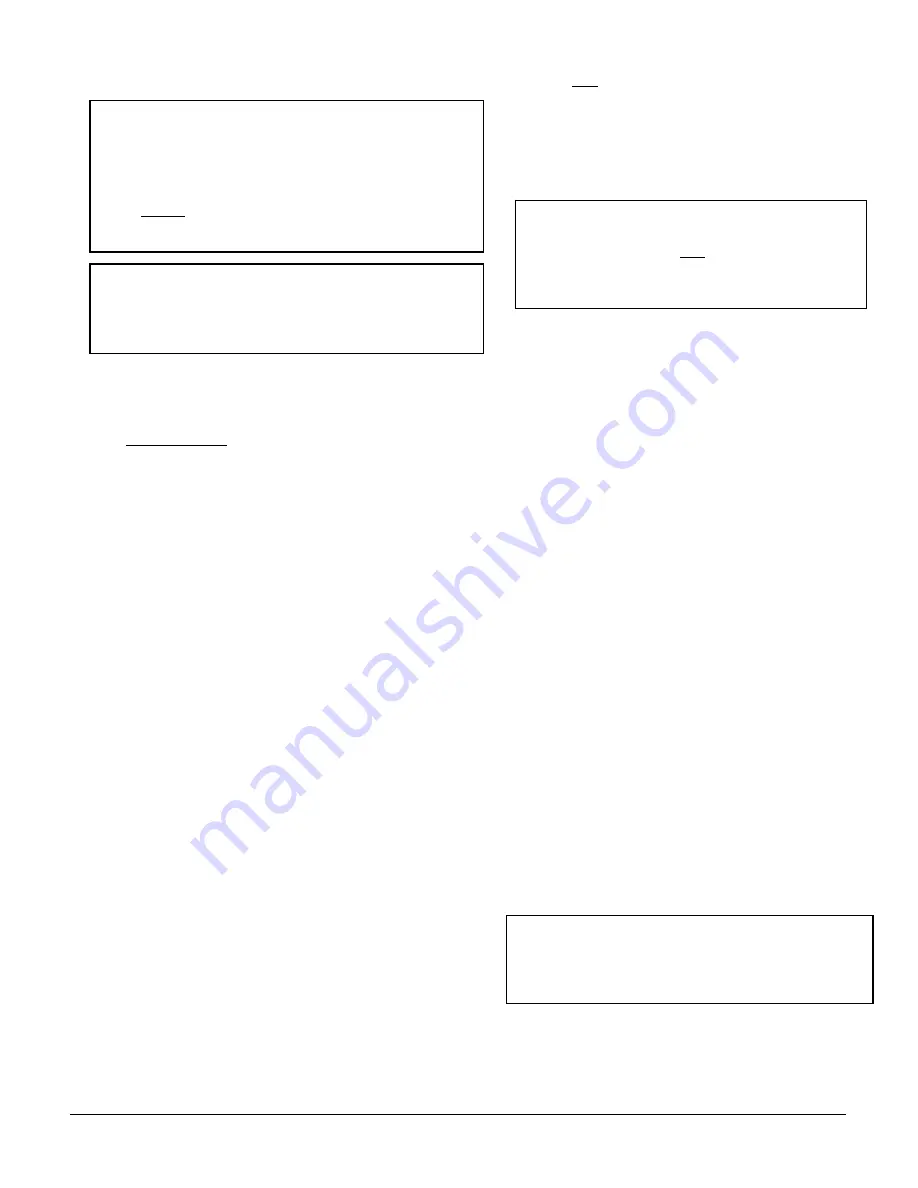
11
2.
The total
CAUTION
Low flue gas temperatures increase the risk of
condensation. Adjust the total temperature at or higher
then 204°C (400°F) in order for the heat exchanger
warranty to remain in force.
3.3.3 Combustion
Check
vent temperature should be between 204
and 302°C (400 and 575°F). If not, check for improper
air temperature rise, pump pressure, nozzle size or a
badly soothed heat exchanger.
IMPORTANT
The heat exchanger metal surfaces may have oil and the
baffle insulation also contains binders. These products will
3.3.7 Supply Air Temperature Rise Test
burn or evaporate when the unit operates for the first time.
1.
Operate the burner for at least 10 minutes;
Because of that, the smoke reading may be skewed during the
first minutes of operation. Therefore, the unit must operate
during at least 60 minutes before taking any readings to adjust
the combustion quality. Let the unit cool down before making
any adjustments.
IMPORTANT
The combustion check verification MUST be performed after
the nozzle replacement or the burner cleaning. After these
2.
Measure the air temperature in the return air plenum;
manipulations, the combustion parameters are necessarily
3.
Measuring the air temperature in the largest trunk
coming off the supply air plenum, just outside the
range of radiant heat from the heat exchanger. 0.3 m
(12") from the plenum of the main take-off is usually
sufficient;
modified. Refer also to the burner instruction manual.
1.
Pierce a test hole in the flue pipe, approximately 18 inches
from the furnace breech. Insert the smoke test probe into
the hole. For installation using a sidewall venting, use the
orifice provided on the breech plate;
4.
The temperature rise is calculated by subtracting the
return air temperature from the supply air
temperature;
2.
From a cold start, let the unit operate for about 5 minutes;
3.
Set the burner air setting until you have between 0 and 1
on the Bacharach Scale (or a ‘’trace’’);
5.
If the temperature rise is lower or exceeds the
temperature specified in Table 6, change to the next
lower or higher blower speed tap, until the
temperature rise falls to the target. If the excessive
temperature rise cannot be increased or reduced by
changing fan speed, investigate for ductwork
obstructions, dirty or improper air filter, improper firing
caused by improper pump pressure or nozzle sizing.
4.
Take a CO
2
sample at the same test location where the
#1 smoke reading was taken and make note of it.
Example: 13.8% of CO or 2.5% of O ;
2
2
5.
Adjust the burner air setting to obtain a CO
2
reading 1.5%
lower (or a O
2
reading 2.0% higher) than the reading
associated with the ‘’trace’’ of smoke. Example: 12.3% of
CO or 4.5% of O ;
2
2
3.3.8 Limit Control Check
6.
This method of adjusting the burner will result in clean
combustion (Bacharach smoke scale between 0 and a
‘’trace’’) and ensure the proper functioning of the system.
The optimum CO
After operating the furnace for at least 15 minutes, restrict
the return air supply by blocking the filters or the return air
register and allow the furnace to shut off on High Limit.
The burner will shut off but the blower will continue to run.
2
level is around 12% to 13% (or 3.5% to
5.0% of O ).
2
Remove the obstruction and the burner should restart
after a few minutes. The time required for the restart also
depends on the adjustment of the blower “OFF” delay.
3.3.4
Draft Regulator adjustment
On chimney installations only, a barometric draft regulator
(supplied with the furnace) must be installed, in order to ensure
proper draft through the furnace. The barometric damper must
be mounted with the hinge pins in a horizontal position and the
face of the damper vertical for proper functioning (see
instructions included with the damper.) After the furnace has
been firing for at least five minutes, the draft regulator should
be set to between -0.025" and -0.060" W.C.
3.3.9 Restart after Burner Failure
1.
Set the thermostat lower than room temperature;
2.
Press the reset button on the burner primary control
(relay);
3.
Set the thermostat higher than room temperature;
4.
If the burner motor does not start or ignition fails, turn
off the disconnect switch and CALL A QUALIFIED
SERVICE TECHNICIAN.
3.3.5
Overfire pressure test
The overfire draft that is taken through the observation port,
located above the burner, is a measurement necessary to
determine if there is a blockage in the heat exchanger or the
flue pipe. Refer to the Technical Specifications in this manual
for overfire pressure values. A high pressure condition may be
caused by excessive combustion air, due to the air band being
too wide open, or a lack of flue draft (chimney effect) or some
other blockage, such as soot in the secondary section of the
heat exchanger or the use of an oversize nozzle input or high
pressure pump.
CAUTION
Do not attempt to start the burner when excess oil has
accumulated, when the furnace is full of vapour or when
the combustion chamber is hot.
3.3.6 Vent Temperature Test
1.
After having adjusted the burner combustion, insert a
thermometer into the test hole in the breech pipe;
Содержание AMP098SD
Страница 17: ...Figure 9 Furnace dimensions 17 ...
Страница 18: ...Figure 10 Wiring diagram 4 speed motor PSC 18 ...
Страница 19: ...Figure 11 Wiring diagram variable speed motor ECM 19 ...
Страница 20: ...Figure 12 Parts list with 4 speed motor PSC 20 B50064H ...
Страница 22: ...Figure 13 Parts list with variable speed motor ECM 22 B50074H ...