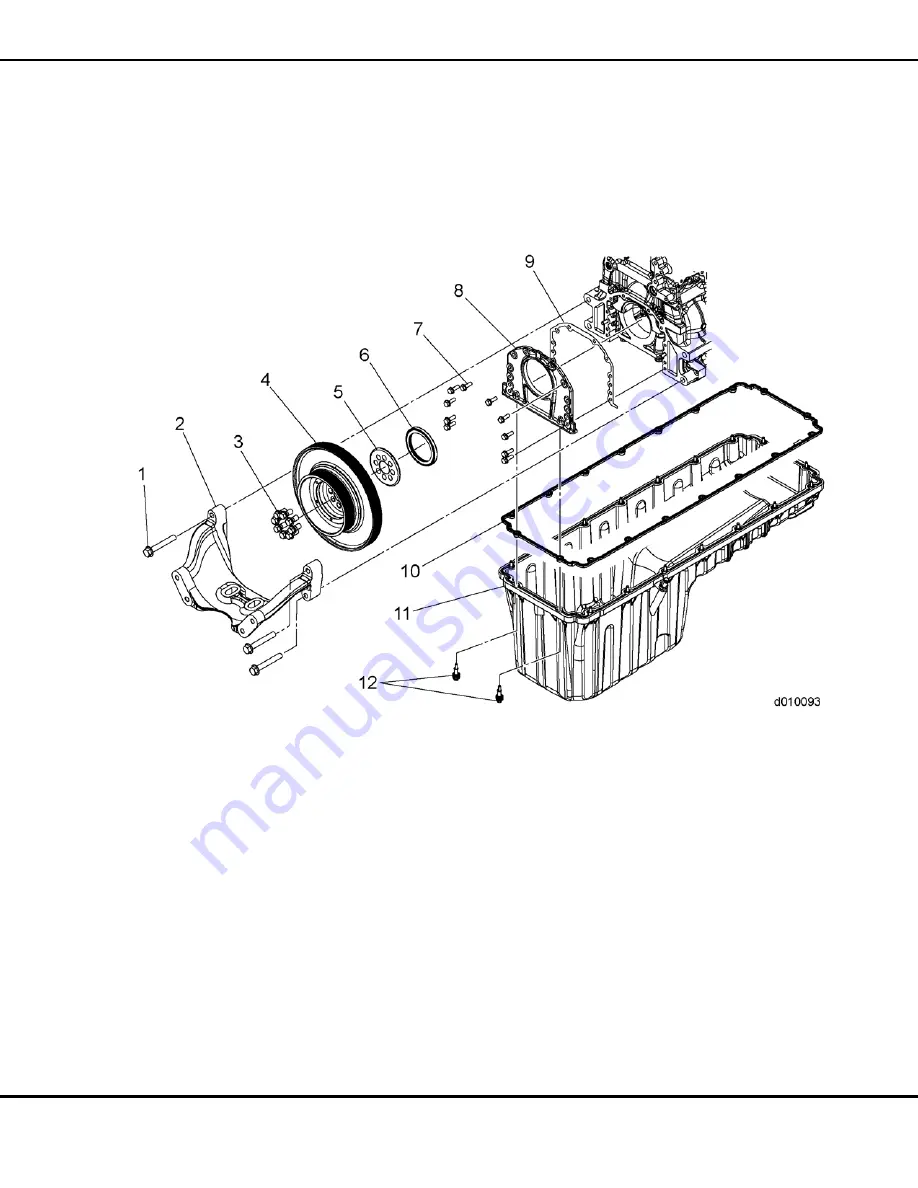
EPA07/10 DD PLATFORM WORKSHOP MANUAL - ENGINE
37.1 DESCRIPTION AND OPERATION OF THE FRONT ENGINE COVER
The front cover housing seals the cylinder block to the oil pan, while also holding the front radial
seal to the machined surface of the crankshaft nose. The front radial seal prevents oil leaks at
the crankshaft.
1. Front Mounting Bracket Bolt (4 qty.)
7. Front Cover Mounting Bolts (10 qty.)
2. Front Mounting Bracket
8. Front Cover
3. Vibration Damper Mounting Bolts (8 qty.)
9. Front Cover Gasket
4. Vibration Damper
10. Oil Pan Gasket
5. Splash Ring
11. Oil Pan
6. Front Radial Seal
12. Oil Pan Mounting Bolts (18 qty.)
Figure 37-1
Front Engine Cover and Related Components
All information subject to change without notice.
DDC-SVC-MAN-0081 2010
Copyright © 2010 DETROIT DIESEL CORPORATION
37-3
Содержание EPA07
Страница 1: ......
Страница 2: ......
Страница 100: ...All information subject to change without notice 7 2 DDC SVC MAN 0081 2010 Copyright 2010 DETROIT DIESEL CORPORATION ...
Страница 106: ...All information subject to change without notice 8 2 DDC SVC MAN 0081 2010 Copyright 2010 DETROIT DIESEL CORPORATION ...
Страница 116: ...All information subject to change without notice 9 2 DDC SVC MAN 0081 2010 Copyright 2010 DETROIT DIESEL CORPORATION ...
Страница 132: ...All information subject to change without notice 10 2 DDC SVC MAN 0081 2010 Copyright 2010 DETROIT DIESEL CORPORATION ...
Страница 140: ...All information subject to change without notice 11 2 DDC SVC MAN 0081 2010 Copyright 2010 DETROIT DIESEL CORPORATION ...
Страница 154: ...All information subject to change without notice 12 2 DDC SVC MAN 0081 2010 Copyright 2010 DETROIT DIESEL CORPORATION ...
Страница 162: ...All information subject to change without notice 13 2 DDC SVC MAN 0081 2010 Copyright 2010 DETROIT DIESEL CORPORATION ...
Страница 170: ...All information subject to change without notice 14 2 DDC SVC MAN 0081 2010 Copyright 2010 DETROIT DIESEL CORPORATION ...
Страница 204: ...All information subject to change without notice 15 2 DDC SVC MAN 0081 2010 Copyright 2010 DETROIT DIESEL CORPORATION ...
Страница 222: ...All information subject to change without notice 16 2 DDC SVC MAN 0081 2010 Copyright 2010 DETROIT DIESEL CORPORATION ...
Страница 232: ...All information subject to change without notice 17 2 DDC SVC MAN 0081 2010 Copyright 2010 DETROIT DIESEL CORPORATION ...
Страница 251: ...18 LUBRICATION SYSTEM Section Page 18 1 DESCRIPTION AND OPERATION OF THE LUBRICATION SYSTEM AND RELATED COMPONENTS 18 3 ...
Страница 252: ...All information subject to change without notice 18 2 DDC SVC MAN 0081 2010 Copyright 2010 DETROIT DIESEL CORPORATION ...
Страница 256: ...All information subject to change without notice 19 2 DDC SVC MAN 0081 2010 Copyright 2010 DETROIT DIESEL CORPORATION ...
Страница 268: ...All information subject to change without notice 20 2 DDC SVC MAN 0081 2010 Copyright 2010 DETROIT DIESEL CORPORATION ...
Страница 274: ...All information subject to change without notice 21 2 DDC SVC MAN 0081 2010 Copyright 2010 DETROIT DIESEL CORPORATION ...
Страница 280: ...All information subject to change without notice 22 2 DDC SVC MAN 0081 2010 Copyright 2010 DETROIT DIESEL CORPORATION ...
Страница 287: ...23 OIL FILTER Section Page 23 1 REPLACEMENT OF THE OIL FILTER 23 3 ...
Страница 288: ...All information subject to change without notice 23 2 DDC SVC MAN 0081 2010 Copyright 2010 DETROIT DIESEL CORPORATION ...
Страница 292: ...All information subject to change without notice 24 2 DDC SVC MAN 0081 2010 Copyright 2010 DETROIT DIESEL CORPORATION ...
Страница 297: ...25 OIL FILLER NECK Section Page 25 1 REMOVAL OF THE OIL FILLER NECK 25 3 25 2 INSTALLATION OF THE OIL FILLER NECK 25 4 ...
Страница 298: ...All information subject to change without notice 25 2 DDC SVC MAN 0081 2010 Copyright 2010 DETROIT DIESEL CORPORATION ...
Страница 302: ...All information subject to change without notice 26 2 DDC SVC MAN 0081 2010 Copyright 2010 DETROIT DIESEL CORPORATION ...
Страница 313: ...27 PRIMING THE LUBRICATION SYSTEM Section Page 27 1 PRIMING THE ENGINE LUBRICATION SYSTEM 27 3 ...
Страница 314: ...All information subject to change without notice 27 2 DDC SVC MAN 0081 2010 Copyright 2010 DETROIT DIESEL CORPORATION ...
Страница 319: ...28 COOLING SYSTEM Section Page 28 1 DESCRIPTION AND OPERATION OF COOLING SYSTEM AND RELATED COMPONENTS 28 3 ...
Страница 320: ...All information subject to change without notice 28 2 DDC SVC MAN 0081 2010 Copyright 2010 DETROIT DIESEL CORPORATION ...
Страница 324: ...All information subject to change without notice 29 2 DDC SVC MAN 0081 2010 Copyright 2010 DETROIT DIESEL CORPORATION ...
Страница 330: ...All information subject to change without notice 30 2 DDC SVC MAN 0081 2010 Copyright 2010 DETROIT DIESEL CORPORATION ...
Страница 338: ...All information subject to change without notice 31 2 DDC SVC MAN 0081 2010 Copyright 2010 DETROIT DIESEL CORPORATION ...
Страница 344: ...All information subject to change without notice 32 2 DDC SVC MAN 0081 2010 Copyright 2010 DETROIT DIESEL CORPORATION ...
Страница 348: ...All information subject to change without notice 33 2 DDC SVC MAN 0081 2010 Copyright 2010 DETROIT DIESEL CORPORATION ...
Страница 352: ...All information subject to change without notice 34 2 DDC SVC MAN 0081 2010 Copyright 2010 DETROIT DIESEL CORPORATION ...
Страница 366: ...All information subject to change without notice 35 2 DDC SVC MAN 0081 2010 Copyright 2010 DETROIT DIESEL CORPORATION ...
Страница 372: ...All information subject to change without notice 36 2 DDC SVC MAN 0081 2010 Copyright 2010 DETROIT DIESEL CORPORATION ...
Страница 376: ...All information subject to change without notice 37 2 DDC SVC MAN 0081 2010 Copyright 2010 DETROIT DIESEL CORPORATION ...
Страница 382: ...All information subject to change without notice 38 2 DDC SVC MAN 0081 2010 Copyright 2010 DETROIT DIESEL CORPORATION ...
Страница 396: ...All information subject to change without notice 39 2 DDC SVC MAN 0081 2010 Copyright 2010 DETROIT DIESEL CORPORATION ...
Страница 408: ...All information subject to change without notice 40 2 DDC SVC MAN 0081 2010 Copyright 2010 DETROIT DIESEL CORPORATION ...
Страница 418: ...All information subject to change without notice 41 2 DDC SVC MAN 0081 2010 Copyright 2010 DETROIT DIESEL CORPORATION ...
Страница 426: ...All information subject to change without notice 42 2 DDC SVC MAN 0081 2010 Copyright 2010 DETROIT DIESEL CORPORATION ...