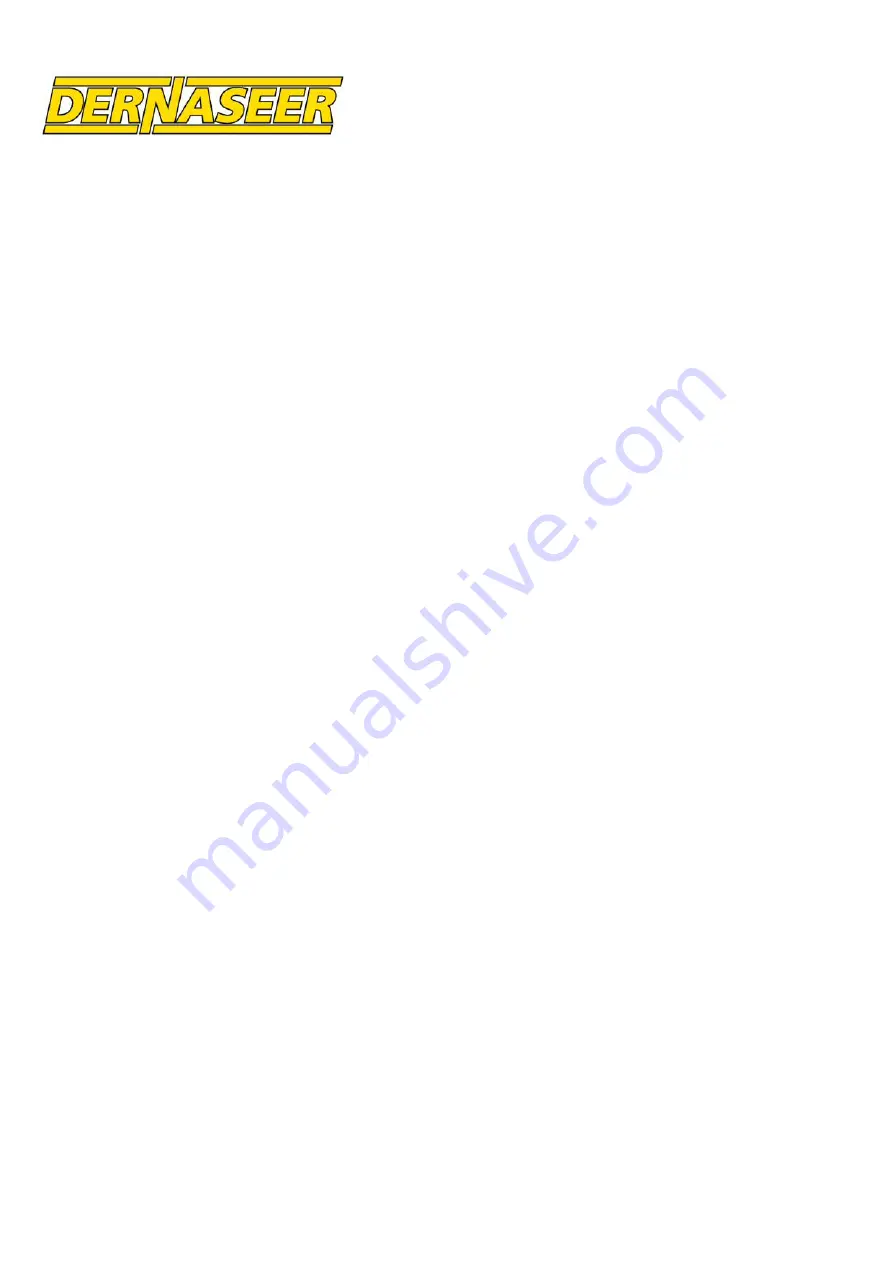
TF220s
11
ELECTRICAL AND ENGINE SAFETY
1.
Never work on the electrical system of any equipment unless you are thoroughly
familiar with system details.
2.
Work on the electrical system must only be carried out by a qualified electrician.
3.
The electrical equipment of the machine should be inspected at regular intervals.
Damaged cables or loose connections must be corrected immediately. Use only
original fuses with the specified current rating.
4.
It is recommended that an earth leakage safety switch be fitted in the supply line to
the power point on site. Special care should be taken to ensure that earth wires are
correctly connected.
5.
Disconnect the battery ground leads whenever performing any electrical
maintenance or servicing to your engine.
6.
Battery posts, terminals and related accessories contain lead and lead
compounds, chemicals known to the State of California to cause cancer and
reproductive harm. Wash hands after handling.
7.
Never short across the starter terminals of a battery as this can cause a fire and
could also damage the electrical system.
8.
Battery electrolyte contains acid and can cause serious injury. Avoid contact with
skin and eyes. Use gloves and protective glasses.
9.
Diesel engine exhaust emissions contain products of combustion which may be
harmful to your health. Always operate the machine in a well ventilated area and if
operating in an enclosed area, vent the emissions outside.
10.
Do not touch any part of the engine or exhaust system. Allow the engine and
exhaust to cool before performing any repair or maintenance.
11.
Never fill the fuel tank with the engine running, while smoking or when near an
open flame.
12.
Never overfill the tank or spill fuel. If fuel is spilled, clean it up immediately.
Содержание TF 220s
Страница 2: ...TF220s 1 BLANK PAGE ...
Страница 4: ...TF220s 3 BLANK PAGE ...
Страница 6: ...TF220s 5 BLANK PAGE ...
Страница 7: ...TF220s 6 SAFETY ...
Страница 8: ...TF220s 7 BLANK PAGE ...
Страница 17: ...TF220s 16 TECHNICAL INFORMATION ...
Страница 18: ...TF220s 17 BLANK PAGE ...
Страница 24: ...TF220s 23 2930 25 25667 10356 2930 1615 3910 27525 WORKING DIMENSIONS ...
Страница 27: ...TF220s 26 ...
Страница 28: ...TF220s 27 BLANK PAGE ...
Страница 29: ...TF220s 28 OPERATION ...
Страница 30: ...TF220s 29 BLANK PAGE ...
Страница 38: ...TF220s 37 BLANK PAGE ...
Страница 39: ...TF220s 38 MAINTENANCE ...
Страница 40: ...TF220s 39 BLANK PAGE ...
Страница 54: ...TF220s 53 BLANK PAGE ...
Страница 55: ...TF220s 54 TROUBLESHOOTING ...
Страница 56: ...TF220s 55 BLANK PAGE ...
Страница 61: ...TF220s 60 APPENDIX ...
Страница 62: ...TF220s 61 BLANK PAGE ...
Страница 68: ...TF220s 67 BLANK PAGE ...
Страница 72: ...TF220s 71 BLANK PAGE ...
Страница 73: ...TF220s 72 SPARE PARTS ...
Страница 74: ...TF220s 73 BLANK PAGE ...
Страница 75: ...TF220s 74 ...