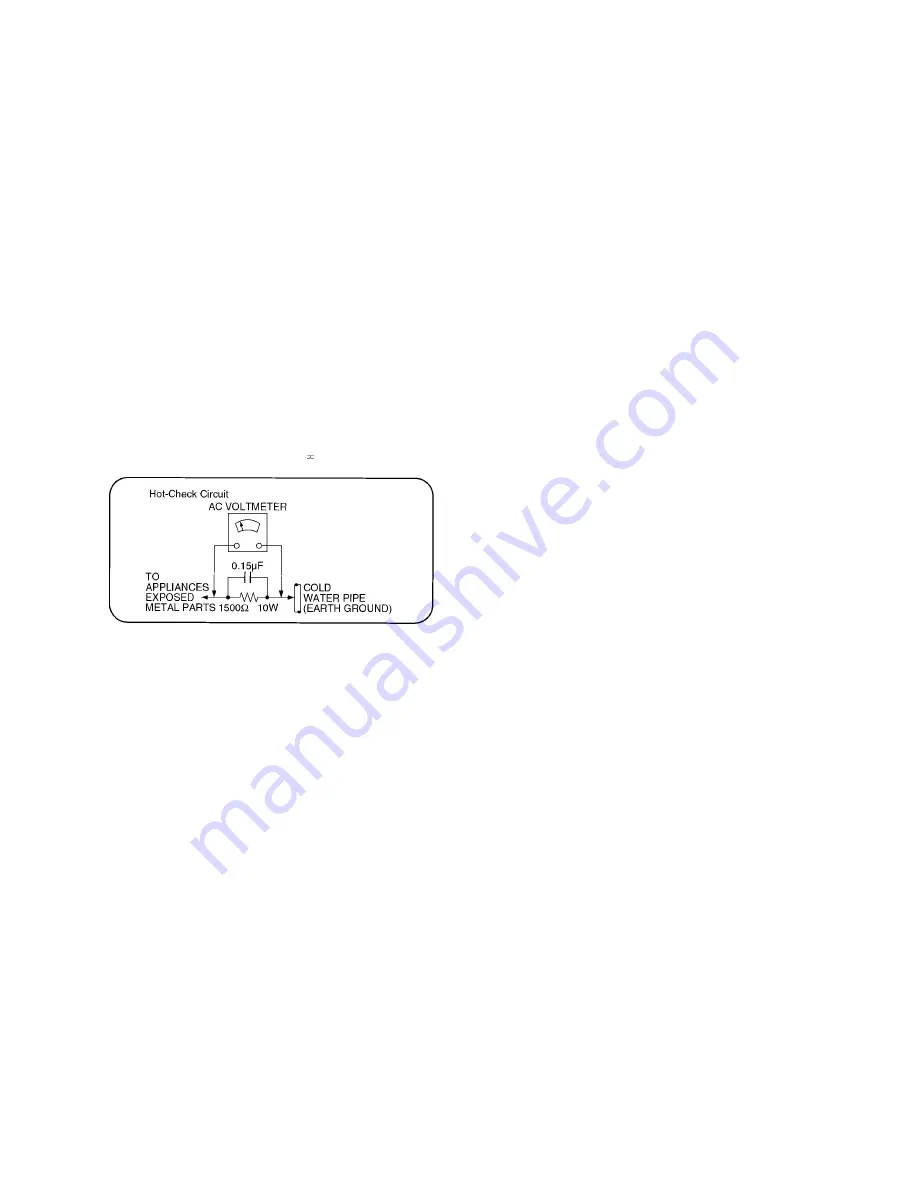
3
1.1.1.
LEAKAGE CURRENT COLD
CHECK
1. Unplug the AC cord and connect a jumper between the two
prongs on the plug.
2. Measure the resistance value, with an ohmmeter, between
the jumpered AC plug and each exposed metallic cabinet
part on the equipment such as screwheads, connectors,
control shafts, etc. When the exposed metallic part has a
return path to the chassis, the reading should be between
1M
:
and 5.2M
:
.
When the exposed metal does not have a return path to
the chassis, the reading must be
.
Figure 1
1.1.2.
LEAKAGE CURRENT HOT CHECK
(See Figure 1 .)
1. Plug the AC cord directly into the AC outlet. Do not use an
isolation transformer for this check.
2. Connect a 1.5k
:
, 10 watts resistor, in parallel with a 0.15µF
capacitors, between each exposed metallic part on the set
and a good earth ground such as a water pipe, as shown in
Figure 1.
3. Use an AC voltmeter, with 1000 ohms/volt or more
sensitivity, to measure the potential across the resistor.
4. Check each exposed metallic part, and measure the
voltage at each point.
5. Reverse the AC plug in the AC outlet and repeat each of the
above measurements.
6. The potential at any point should not exceed 0.75 volts
RMS. A leakage current tester (Simpson Model 229 or
equivalent) may be used to make the hot checks, leakage
current mu3st not exceed 1/2 milliamp. In case a
measurement is outside of the limits specified, there is a
possibility of a shock hazard, and the equipment should be
repaired and rechecked before it is returned to the
customer.
1 SAFETY PRECAUTIONS
1.1. GENERAL GUIDELINES
1. When servicing, observe the original lead dress. If a short circuit is found, replace all parts which have been overheated or
damaged by the short circuit.
2. After servicing, see to it that all the protective devices such as insulation barriers, insulation papers shields are properly
installed.
3. After servicing, make the following leakage current checks to prevent the customer from being exposed to shock hazards.
2 PREVENTION OF ELECTRO STATIC DISCHARGE (ESD)
TO ELECTROSTATICALLY SENSITIVE (ES) DEVICES
Some semiconductor (solid state) devices can be damaged easily by static electricity. Such components commonly are called
Electrostatically Sensitive (ES) Devices. Examples of typical ES devices are integrated circuits and some field-effect transistors and
semiconductor "chip" components. The following techniques should be used to help reduce the incidence of component damage
caused by electro static discharge (ESD).
1. Immediately before handling any semiconductor component or semiconductor-equipped assembly, drain off any ESD on your
body by touching a known earth ground. Alternatively, obtain and wear a commercially available discharging ESD wrist strap,
which should be removed for potential shock reasons prior to applying power to the unit under test.
2. After removing an electrical assembly equipped with ES devices, place the assembly on a conductive surface such as alminum
foil, to prevent electrostatic charge buildup or exposure of the assembly.
3. Use only a grounded-tip soldering iron to solder or unsolder ES devices.
4. Use only an anti-static solder removal device. Some solder removal devices not classified as "anti-static (ESD protected)" can
generate electrical charge sufficient to damage ES devices.
5. Do not use freon-propelled chemicals. These can generate electrical charges sufficient to damage ES devices.
6. Do not remove a replacement ES device from its protective package until immediately before you are ready to install it. (Most
replacement ES devices are packaged with leads electrically shorted together by conductive foam, alminum foil or comparable
conductive material).
7. Immediately before removing the protective material from the leads of a replacement ES device, touch the protective material
to the chassis or circuit assembly into which the device will be installed.
Содержание DVD-1600
Страница 10: ...10 5 12 3 List of the Extention Cables...
Страница 21: ...21 8 8 Self diagnosis Function and Service Modes...
Страница 23: ...23...
Страница 24: ...24 8 10 Servo Process Flow...
Страница 25: ...25 8 11 Servo Process Display Mode 8 12 ADSC Internal Ram Data Display...
Страница 33: ...33 4 Cut the antistatic flexible sheet for the optical pickup unit Fig 6...
Страница 60: ...60 15 2 POWER SECTION MOTHER P C B 1 5 SCHEMATIC DIAGRAM...
Страница 61: ...61...
Страница 62: ...62 15 3 VIDEO OUT SECTION MOTHER P C B 2 5 SCHEMATIC DIAGRAM...
Страница 63: ...63...
Страница 64: ...64 15 4 AUDIO OUT 1 SECTION MOTHER P C B 3 5 SCHEMATIC DIAGRAM...
Страница 65: ...65...
Страница 66: ...66 15 5 AUDIO OUT 2 SECTION MOTHER P C B 4 5 SCHEMATIC DIAGRAM...
Страница 67: ...67...
Страница 68: ...68 15 6 OPERATION SECTION MOTHER P C B 5 5 SCHEMATIC DIAGRAM...
Страница 69: ...69...
Страница 70: ...70 15 7 FEP SECTION MODULE P C B 1 8 SCHEMATIC DIAGRAM...
Страница 71: ...71...
Страница 72: ...72 15 8 SODC SECTION MODULE P C B 2 8 SCHEMATIC DIAGRAM...
Страница 73: ...73...
Страница 74: ...74 15 9 AV DECORDER SECTION MODULE P C B 3 8 SCHEMATIC DIAGRAM...
Страница 75: ...75...
Страница 76: ...76 15 10 VIDEO D A SECTION MODULE P C B 4 8 SCHEMATIC DIAGRAM...
Страница 77: ...77...
Страница 78: ...78 15 11 AUDIO D A CONVERTER SECTION MODULE P C B 5 8 SCHEMATIC...
Страница 79: ...79 15 12 PROGRESSIVE SECTION MODULE P C B 6 8 SCHEMATIC DIAGRAM...
Страница 80: ...80...
Страница 81: ...81 15 13 WM SECTION MODULE P C B 7 8 SCHEMATIC DIAGRAM...
Страница 82: ...82 15 14 CPU SECTION MODULE P C B 8 8 SCHEMATIC DIAGRAM...
Страница 83: ...83...
Страница 84: ...84 15 15 TERMINAL SCHEMATIC DIAGRAM...
Страница 85: ...85 15 16 FRONT 1 FRONT 2 AND FRONT 3 SCHEMATIC DIAGRAM...
Страница 86: ...86...
Страница 97: ...97 17 EXPLODED VIEWS 17 1 Casing Parts Mechanism Section Exploded View...
Страница 98: ...98 17 2 Mechanism Section Exploded View...
Страница 99: ...99 17 3 Packing Accessories Section Exploded View...