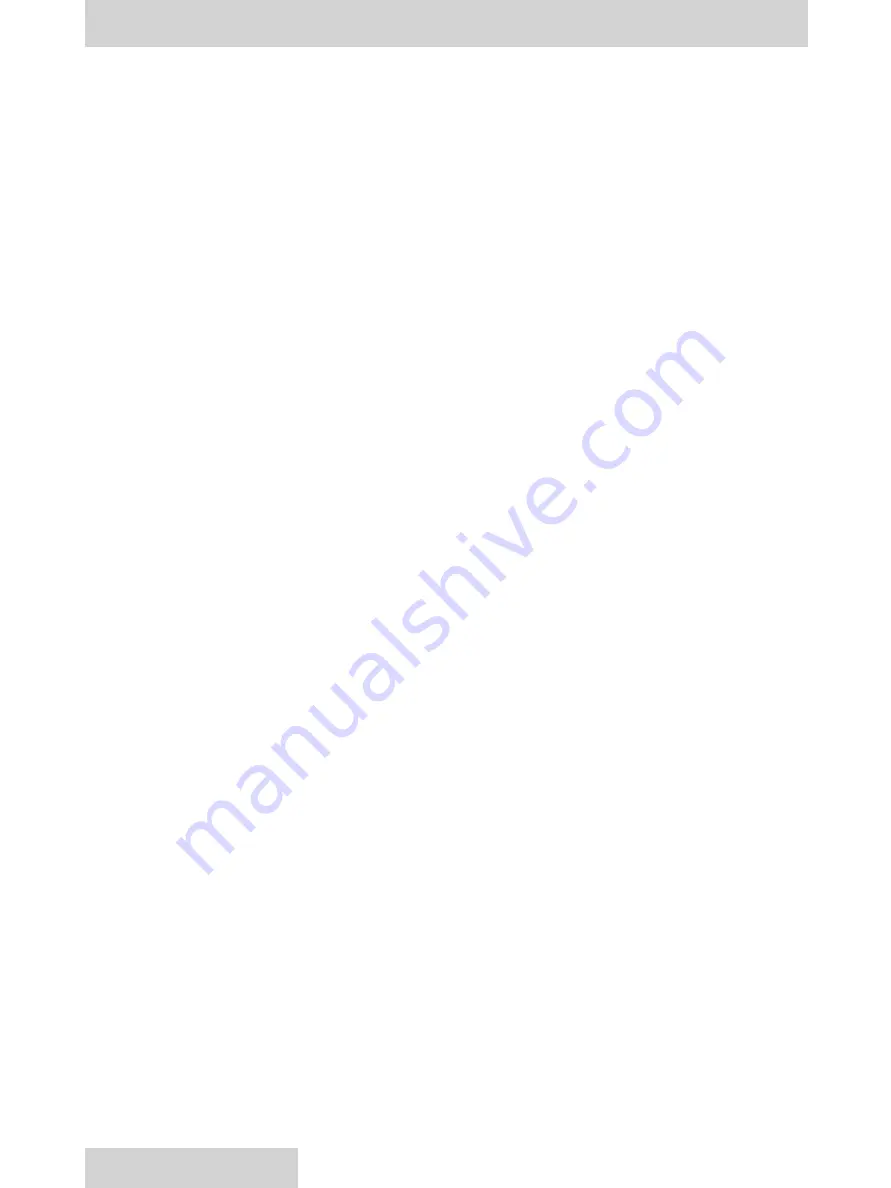
1. See Figure 3. Back off max. volume screw or handwheel to full displacement.
Remove max. volume screw or handwheel assembly.
2. Remove bolts holding cap to pump.
3. Remove plug (15) and attached parts. Remove spring (11) and spool (18).
4. Remove adjusting plug (2) and attached parts. Remove seal piston (5). Note: a 10-
24 screw may be used to assist in pulling the piston. Remove spring (7) and cone (8).
5. Do not remove sleeve in body (1). Sleeve is pressed into cap and finished to size. If
sleeve or cap is worn, replace the cap-sleeve assembly (1).
6. Examine seat (10) for wear. Do not remove unless damaged.
1. Install Avseal plugs (9) and orifice (27) in body.
2. Press seat (10) into bore squarely against shoulder in bore.
3. Install spool (18) into bore as shown. Install spring (11) over end of spool. Install O-
ring (6) on seal (16). Lubricate and install into plug (15). Install plug (15) into cap. Install
screw (3), nut (4) and acorn nut (17).
4. Install O-ring (6) on seal piston (5).
5. Lubricate O-ring and install cone (8), spring (7) and seal piston into bore in cap (1),
being careful that cone enters seat (10). Install remaining parts. Torque plug (29) to 60
Nm. Torque plug (21) to 35 Nm.
6. Note proper location for cap on pump. Install O-rings on interface between cap and
pump control pad.
7. Install on pump control pad, guiding the control piston into the bore. Install maxi-
mum volume stop assembly.
8. Torque mounting bolts to 102 Nm.
Compensator is to be tested on pump. Adjust maximum volume stop to full displace-
ment by backing off stop till there is no contact with the control piston.
1. Install gages on system pressure and on compensator vent ports.
2. Turn compensator adjustment screw (25) CCW until there is no contact with spring,
then adjust 1/2 turn CW after contact is made with spring.
3. Turn differential adjustment screw (3) CCW until there is no contact with spring,
then adjust 1/2 turn CW after contact is made with spring.
4. System relief valve should be set at 35 bar. If testing on application, apply a load to
pump.
5. Start prime mover. Pump should be at full displacement at 35 bar.
6.
Increase system relief valve until compensator de-strokes pump to zero displace-
ment. Set compensator to 103 bar.
7. Adjust compensator differential spool pressure to 13,8 bar. This is accomplished by
adjusting the differential screw until the difference in pressure readings between the sys-
tem pressure and compensator vent gages installed in the compensator cap is 13,8 bar.
(It may be necessary to change differential to gain stability. Use caution when exceeding
17 bar to avoid spring going solid, preventing compensator action.)
8. Set the compensator to 207 bar, 414 bar, and 500 bar.
9. At each condition, increase the system pressure until the pump fully de-strokes. At
no time should the system pressure vary more than 10,3 bar from the compensator set-
ting. The control should be steady and stable at all conditions.
10. Reduce pressure to 10,3 bar below the compensator setting. Pump should return to
full stroke. Repeat two or more times. Compensator setting should be repeatable.
11. Set compensator adjustment to the required setting, or 414 Bar if not otherwise
noted.
PRESSURE COMPENSATOR
COMPENSATOR DISASSEMBLY
ASSEMBLY
COMPENSATOR TEST AND
ADJUSTMENT
8
www.comoso.com