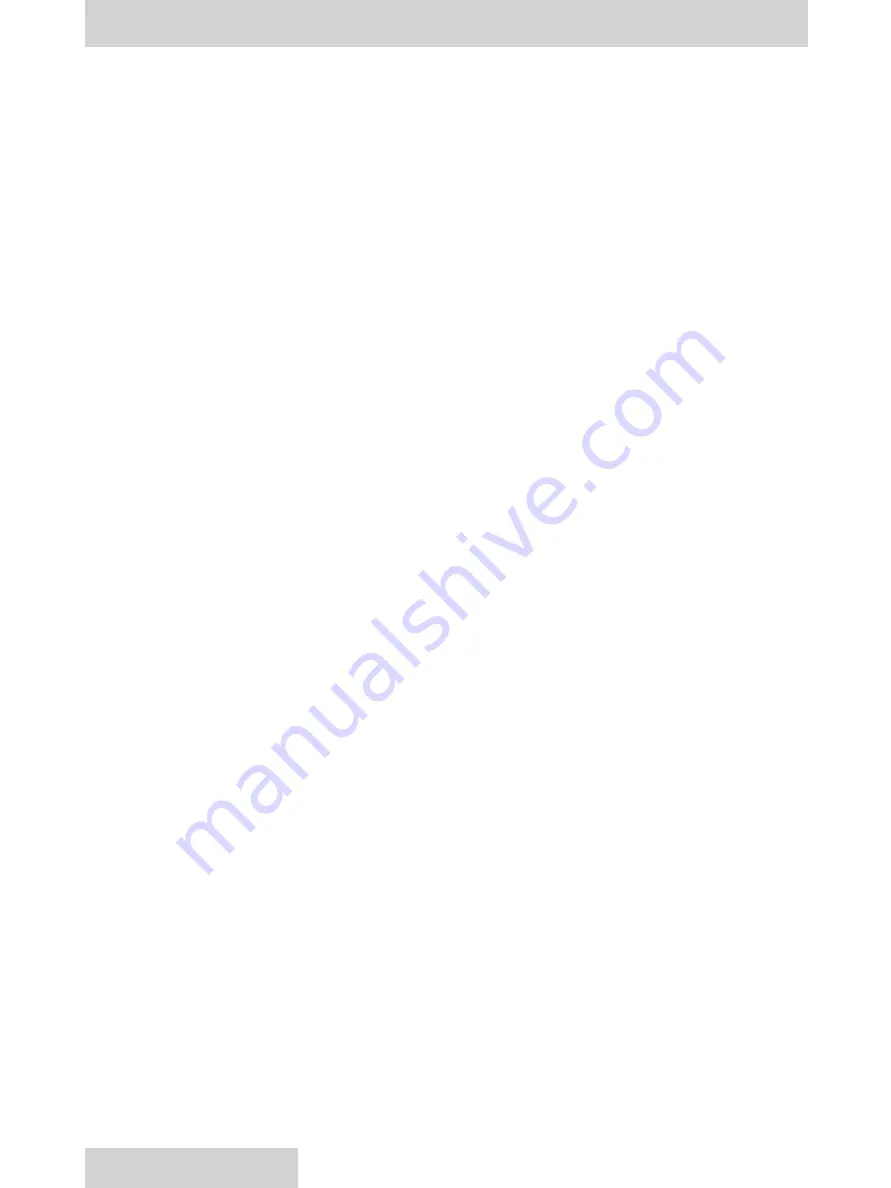
The instructions contained in this manual cover complete disassembly and reassembly of the con-
trols. Before proceeding with the disassembly or reassembly of any unit, this manual should be
studied in order to become familiar with proper order and parts nomenclature.
A piloted three-way valve spool and sleeve combination is the nucleus of the control function. For
the compensator, torque limiter and load sensing controls, system pressure is applied to the input
port of the valve, and to one end of the spool. A small orifice feeds this pressure to the other end of
the spool,. A spring on this end biases the spool to normally port the control piston to pump case .
This control piston links to the pump cam. On the opposite side of the control piston, a spring and
a piston connected to system pressure along with pump timing forces, combine to put the pump
on stroke.
A spring-loaded cone and seat connected to the spring end of the three-way spool establishes an
adjustable pressure limit on this end of the spool. When system pressure reaches this value, flow
through the spool creates a pressure difference across the spool. At approximately 200 psi, 13,8
bar difference, the spool shifts toward the spring, re-directing the control cylinder port to pressure.
This pressure applied to the control piston overcomes the forces putting the pump on stroke,
causing the pump to reduce displacement. When the pump pressure drops, the spool shifts the
other way to maintain the pump pressure at approximately 200 psi, 13,8 bar above the controlled
pressure on the spring side. The spring end of this three-way spool may also be connected to a
remote pressure control, through the vent port, V. Flow through this port, when controlling, is
approximately 0.5 gpm, 1,9 l/m.
For load sensing, this “V” port is connected to the load. The valve between the pump and the load
meters the flow. The pump provides the flow to develop 200 psi, 13,8 bar drop across the valve
independent of the load pressure and thus establishes a constant flow independent of operating
pressure. Adjustment of spring load on the three-way spool allows precise control of the differential
pressure.
Where the approximately 0.5 gpm, 1,9 l/m vent flow is unacceptable, and where multiple loads are
to be controlled, a load sensing control is available. In the load sensing control, the vent flow is
modulated by a valve which senses load pressure and establishes the pump compensator pres-
sure at 300 psi, 21 bar above load pressure. There is essentially no flow in the sensing line.
For constant torque, system pressure and pump displacement are interrelated by the formula
P•V=C. As pressure increases, displacement must reduce, and vice versa.
A linkage to the pump control piston slides a spool over a pin.. The pin contains a cross drilled
hole, and a connecting drilling to one end. This pin passes through a bore in the torque limiter
housing connecting to the vent port of the compensator. The pressure in the vent port applies a
force on the pin, which is resisted on the other end by a two spring combination.
The pin positions itself to where the vent pressure force on the one end is balanced by the spring
force on the other end. When the cross drilled hole opens, it causes the three-way spool to shift to
direct system pressure into the control piston, reducing stroke. The linkage to the control piston
causes the spool to move in the direction to close the cross-drilled hole. Thus, for every position of
the pin, there is a corresponding position for the control piston. The position of the pin is deter-
mined by the pressure, the spring rate, and the initial adjustment on the springs. As pressure
increases, pump stroke must reduce.
At low pressure, only the outer spring contacts the spool. As pressure increases, the second spring
also makes contact. Thus the rate of change of pressure starts at a low initial rate when the pump
is at full stroke and changes to a high rate at reduced stroke, to approximate the P•V=C relation-
ship. The normal compensator function is retained to provide a maximum pressure limit.
The rotary servo control is mounted on the off-stroke side of the control piston. The control piston
has a large diameter on this side, and a smaller diameter on the opposite side. Servo pressure is
connected to the input port on the three-way valve, and also to the smaller diameter side of the
control piston.
When the three-way spool is at rest, this end of the control piston is ported to tank, and servo pres-
sure applied to the opposite, smaller diameter piston causes the rocker cam to stroke to minimum.
When the three-way spool shifts, pressure is directed into the larger diameter of the control piston
causing the cam to shift towards full stroke.
The pin as described for the torque limiter, is spring loaded against a mechanism which converts
rotary motion of the input shaft to linear motion of the pin, thus positioning pump stroke proportion-
ately to input shaft rotation.
In the hydraulic stroker, a spring loaded piston is attached to this pin. A control pressure of 50 psi,
3,45 bar causes the piston to commence to move against the spring, to position the pin in propor-
tion to the control pressure, and thus cause the pump to stroke in proportion to control pressure.
Full stroke is achieved at 210 psi, 14,5 bar control pressure.
INTRODUCTION
GENERAL
DESCRIPTION OF OPERATION
PRESSURE COMPENSATOR
PRESSURE COMPENSATOR
LOAD SENSING CONFIGURA-
TION
LOAD SENSING CONTROL
TORQUE LIMITER
ROTARY SERVO CONTROL
HYDRAULIC STROKER
4
www.comoso.com
Содержание P05
Страница 47: ...47 NOTES www comoso com ...