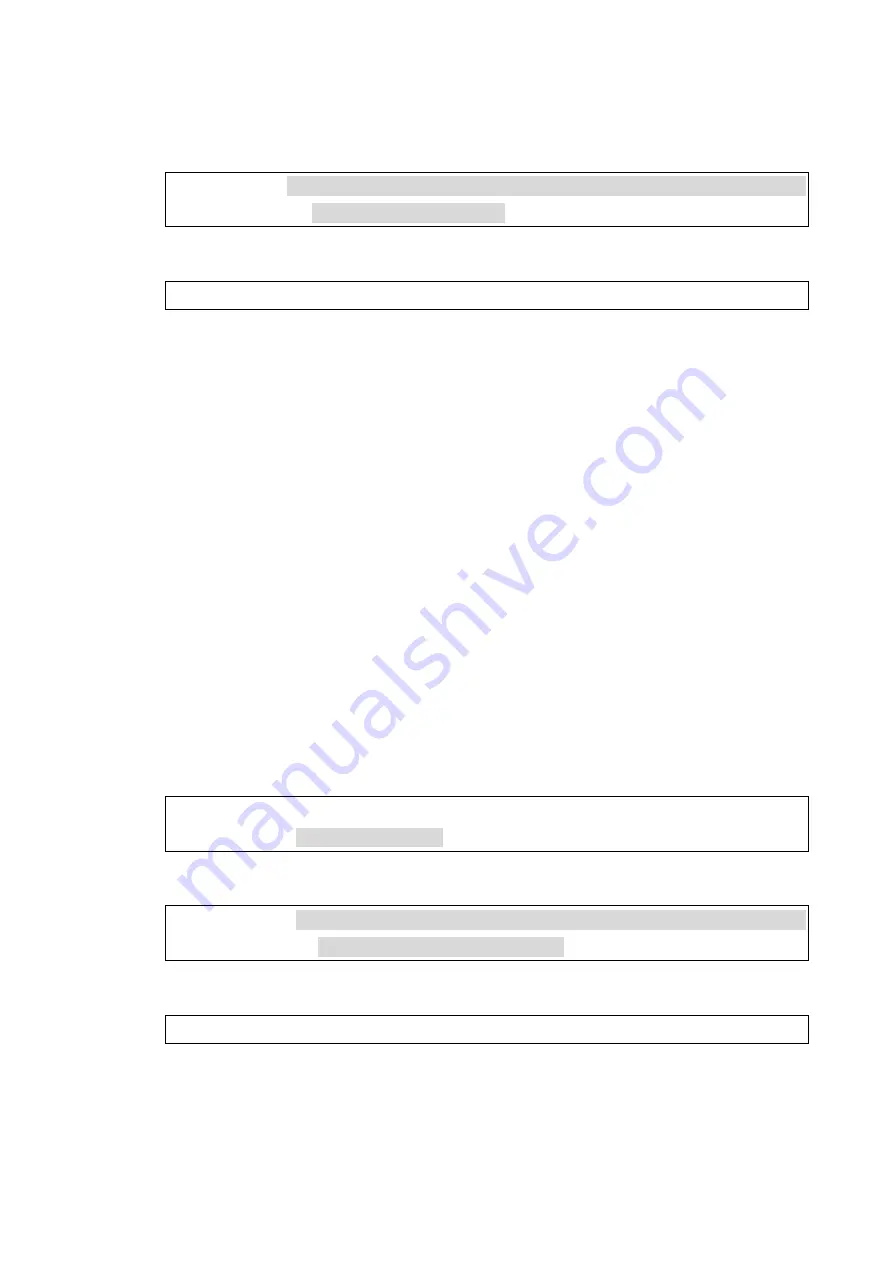
Chapter 3 Flow of machine Adjustment
|
HES Series
3-7
Step 3.Check Pressure Feedback Signal
Firs, set input voltage Pr. 00-04 = 11 PO
Selection of Display Mode
Pr. 00-04
11:
Display the signal of PO analog input terminal, with 0~10V
corresponding to 0~100%.
Set Pr. 00-08=corresponding pressure settings of the 10V pressure sensor
Maximum value of pressure feedback
Pr. 00-08
0~250Bar
Set Rotation speed command to 10rpm and press
【
RUN
】
. Check the pressure value is >0
on the pressure gauge.
When the pressure value is
0
≦
,
;
Gradually increase the rotation speed.
;
Check that each directional valve is closed.
When the pressure value is
>
0
;
Check that the voltage reading displayed on the operation panel is consistent with the
pressure reading on the pressure gauge.
Example:
10V on the pressure sensor corresponds to 250bar. When the pressure gauge
reading is 50 bar, the output voltage on the pressure sensor should be
approximately 50/250*10=2V. So the voltage displayed on the operation panel will
be 20.0(%).
Meanwhile, observe if there is any oil leak.
Step 4. Check Pressure and Flow Commands
This action does not need to start the servo oil pump.
Pr. 00-09 = 1 refers to the pressure control mode
Pressure Control Mode
Pr. 00-09
0: Speed control
1: Pressure control
Pr. 00-04 = 12 sets the PI input voltage
Selection of Display Mode
Pr. 00-04
12: Display the signal value of the PI analog input terminal, with
0~10V corresponding to 0~100%.
Pr. 00-07 = corresponding pressure value with 10V on the pressure controller command
Maximum pressure command
Pr. 00-07
0~250Bar
With the maximum pressure set by the controller, observe the associated value displayed
on the operation panel and set it to 00-14.
With the controller setting at half the maximum pressure, observe the associated value
displayed on the operation panel and set it to 00-15.
With the controller setting at the lowest pressure, observe the associated value displayed
Call 1(800)985-6929 for Sales
deltaacdrives.com
Call 1(800)985-6929 for Sales
deltaacdrives.com