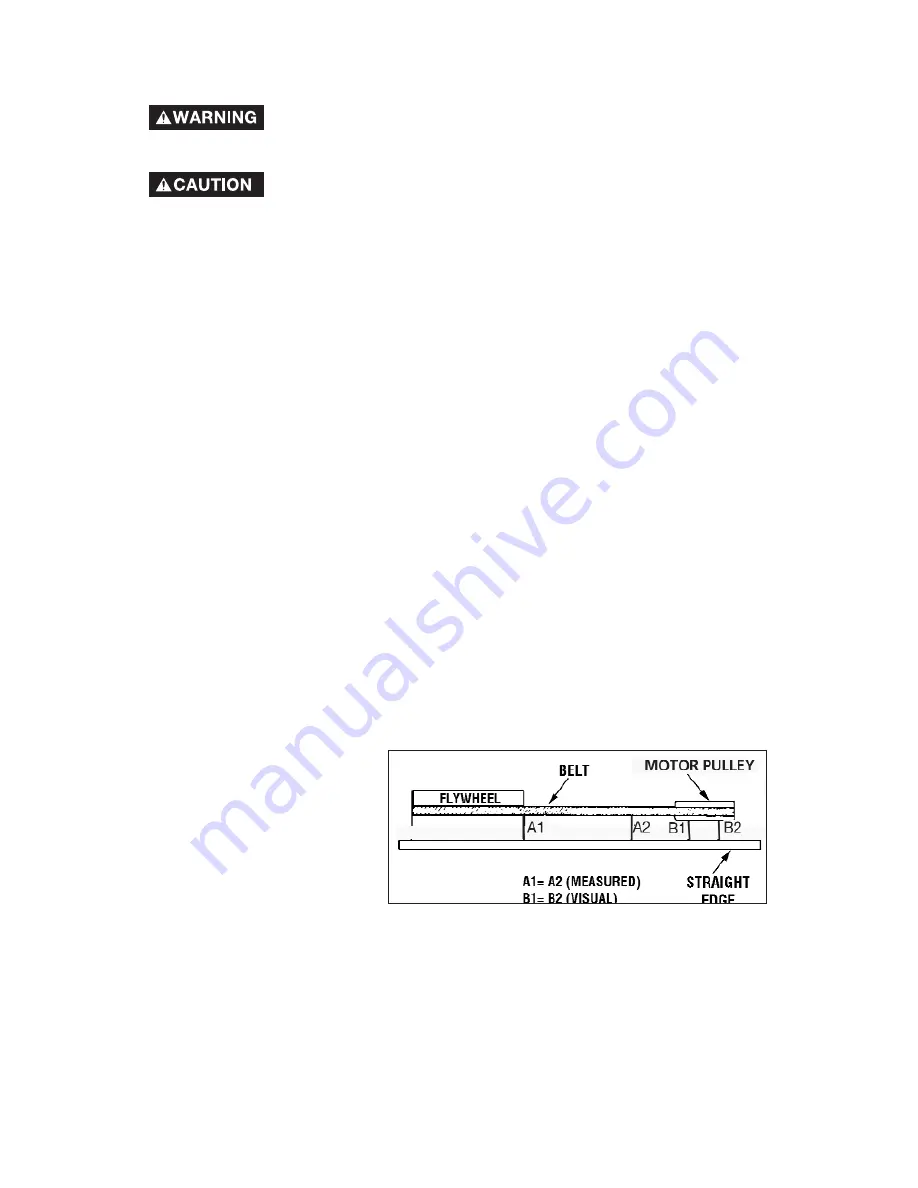
18-ENG
D26269
Air Filter - Inspection and Replacement
Hot surfaces. Risk of burn. Compressor heads are
exposed when filter cover is removed. Allow compressor
to cool prior to servicing.
Keep the air filter clean at all times. Do not operate the air
compressor with the air filter removed.
A dirty air filter will not allow the compressor pump to operate at full capacity.
Before using the compressor pump, check the air filter to make sure it is clean
and in place.
If it is dirty, replace it with a new filter.
1.
Using a pair of needle nose pliers or a screwdriver pull or pry out the old
filter and carefully clean the filter area.
2.
Push the new air filter in place. Refer to the "Repair Parts" for the correct
part number.
IMPORTANT
: Do not operate the compressor with the air filter removed.
3.
Place new air filter into filter cover. Refer to the "Repair Parts" for the
correct part number.
4.
Replace air filter cover and lock into place.
Motor Pulley/Flywheel Alignment
NOTE:
Once the motor pulley has been moved from its factory set location,
the grooves of the flywheel and pulley must be aligned to within 1/16" to
prevent excessive belt wear.
The air compressor flywheel and motor pulley must be in-line (in the same
plane) within 1/16" to assure belt retention within flywheel belt grooves. To
check alignment, perform the following steps:
1.
Unplug air compressor from power source.
2.
Remove belt guard
3.
Place a straightedge
against the outside of the
flywheel and the motor
drive pulley.
4. Measure the distance
between the edge of the
belt and the straightedge
at points A1 and A2 in
figure. The difference between measurements should be no more than
1/16".
5.
If the difference is greater or less than 1/16" loosen the set screw holding
the motor drive pulley to the shaft and adjust the pulley’s position on the
shaft until the A1 and A2 measurements are within 1/16" of each other.
6.
Tighten the motor drive pulley set screw to 70-80 in.-lbs.
Содержание 66-750
Страница 28: ...28 ENG D26269 PUMP DIAGRAM...