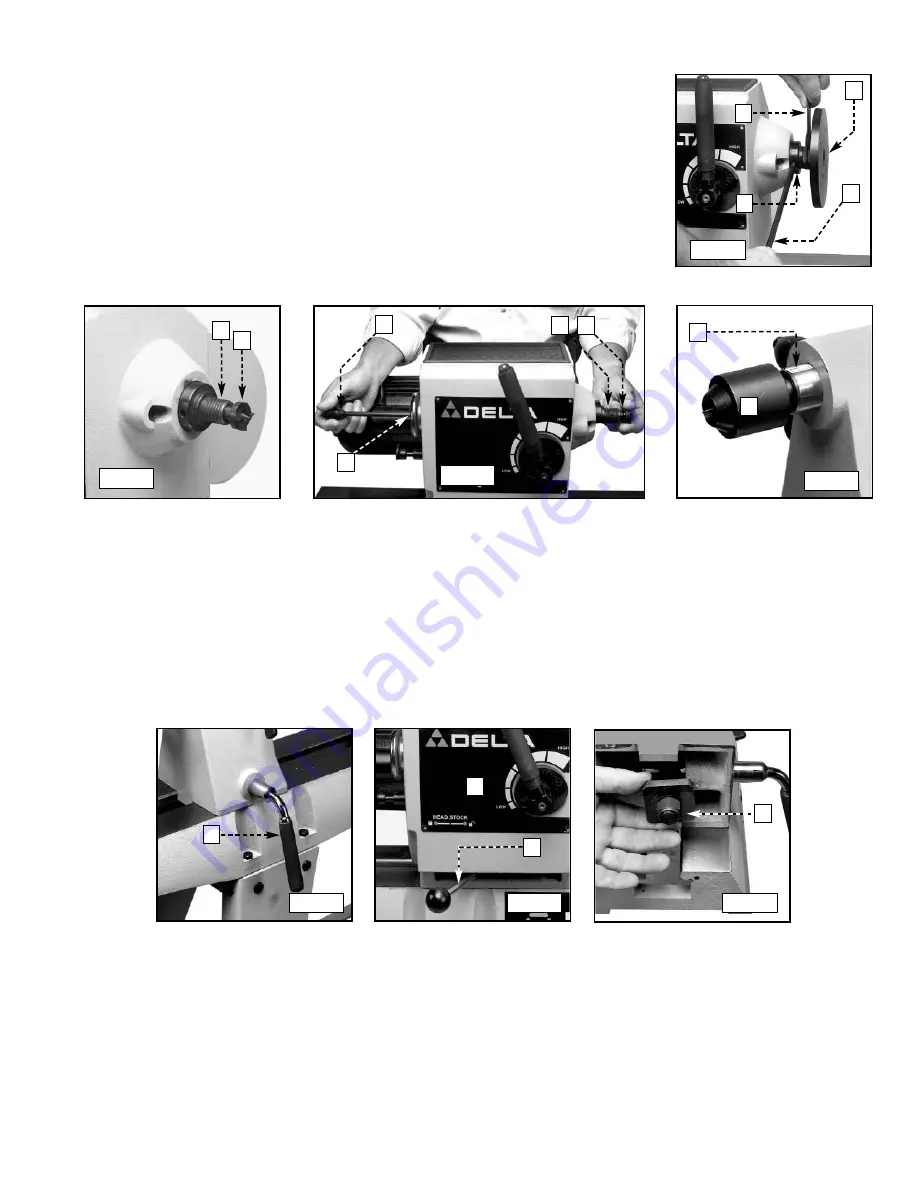
9
HEADSTOCK SPUR CENTER
The 46-715 comes with a faceplate attached. Before inserting the spur center in the spindle,
remove this faceplate. Insert the knockout bar (A) Fig. 10 in the side hole of the spindle (B)
Fig. 10 to hold the spindle in place. Use the supplied wrench (C) Fig. 10 to loosen the
faceplate. Remove the faceplate (D) by turning it counter-clockwise with your hand. The
spur center (A) Fig.11 is equipped with a No. 2 Morse Taper shank. Insert this shank into the
headstock spindle (B).
NOTE:
Before inserting the spur center (A), clean both the shank of the spur center and the
inside of the headstock spindle to remove any grease or debris. To remove the tapered
shank spur center (A) Fig. 11 from the headstock spindle (B) Fig. 11, use the knockout bar
(C) Fig. 12 through the hole (D) in the opposite end of the spindle to push the spur center
out.
IMPORTANT: Never drive the workpiece into the spur center when it is mounted in the
headstock.
See instructions on setting the spur center into the workpiece in the
“OPERATION“
section
of this manual under “
CENTERING THE WORK
.”
Fig. 10
Fig. 11
Fig. 12
Fig. 13
TAILSTOCK LIVE CENTER
The tailstock live center (A) Fig. 13, supplied with your lathe, is equipped with a No. 2 Morse Taper shank.
NOTE:
Before inserting the live center, clean both the shank and the inside of the tailstock to remove any grease or debris. To remove
the live center (A) from the tailstock spindle (B), use the knockout bar (C) Fig. 12 (supplied) through the hole (D) in the opposite end
of the spindle.
D
C
B
A
B
A
A
B
B
A
C
D
ADJUSTING CLAMPS ON THE HEADSTOCK AND TAILSTOCK
The headstock and tailstock can be moved along the lathe bed. A downward push on the handle (A) Fig. 14 locks the mechanism,
while an upward movement of the handle releases the securing action. The clamps are pre-set at the factory. However, should either
need adjusting, use an 11/16” wrench to slightly loosen or tighten the nut (A) Fig. 16 on the tailstock.
NOTE:
Clamp the headstock and tailstock firmly while operating the lathe.
Fig. 14
Fig. 15
Fig. 16
A
A
B
A
TOOL REST
The tool rest (A) and tool rest base (B) are shown in Fig. 17. To position the tool rest on the lathe bed, lift the clamp handle (C), move
the tool rest base and lock it in place by pushing down on the handle (C). To adjust the tool rest (A) for the correct height, loosen
the locking lever (D), move the tool rest (A) up or down and tighten the locking lever (D).
NOTE:
The locking lever (D) Fig. 17 can be positioned on the left or right side of the tool rest base (B). To reposition the tool rest
locking lever (D), unscrew the lever counterclockwise. A threaded hole is provided in the left side of tool rest base (B) to accept the
locking lever (D).
NOTE:
Clamp the tool rest firmly while operating the lathe.
Содержание 46-715
Страница 23: ...23 NOTES...