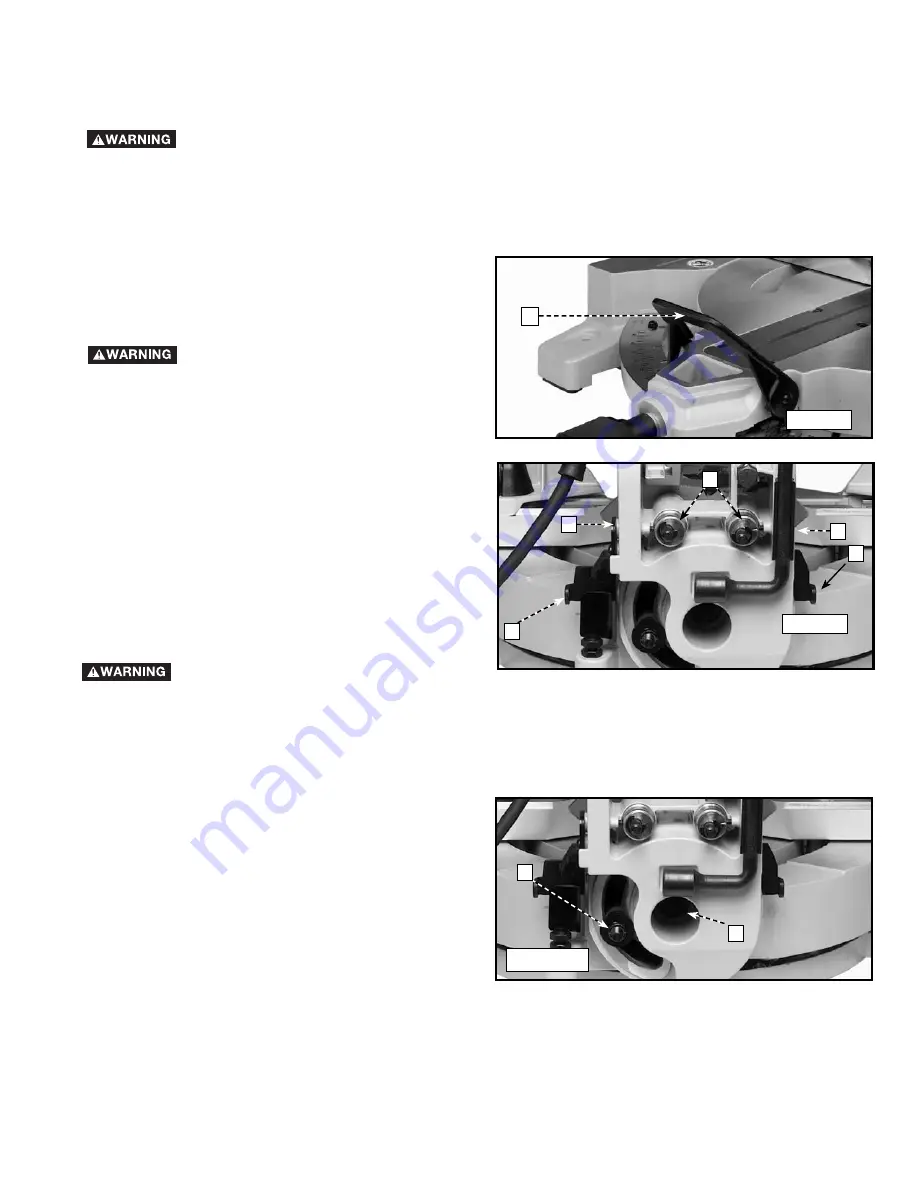
13
ADJUSTING THE BEVEL MOVEMENT
The bevel-locking force has been set at the factory. After
a period of time, you may need to adjust the locking
mechanism. To adjust:
1. Unlock the bevel locking handle (A) Fig. 22.
2. Tighten the pivot head nut (C) Fig. 25 such that the
force to bevel the cutting head by pushing on the
switch handle is 6-10 pounds.
To check the locking action of the bevel lock handle:
1. Lock the bevel locking handle (A) Fig. 22.
2. Check the force to bevel the cutting head by pushing
on the handle with the cutting head in the full upright
position. With the bevel locking handle (A) Fig. 22
down, this force should be 33-35 pounds.
3. If the bevel action needs adjusting, unlock the bevel
handle (A) Fig. 22 and loosen or tighten the nut (A)
Fig. 25 depending on whether you want the bevel
action tighter or looser.
4. Close the bevel handle and check the force it takes to
move the head, as explained in Step 2.
5. Repeat
if
necessary.
ADJUSTING 0°, 33.9°, AND 45° BEVEL POSITIVE STOPS
The bevel adjustment utilizes a sliding plate (A) Fig. 20, pin (B), and bushing (C) design feature that can be adjusted to fine-
adjust the bevel angle. The position of the pin within the bushing is adjustable and, when set, determines the bevel angle. To
adjust, loosen the pin locking screws, move to desired location, and tighten securely.
DISCONNECT MACHINE FROM POWER SOURCE.
1. Position the bevel detent plate so that the desired angle (A) Fig. 23 is exposed.
2. Lift the bevel lock lever (A) Fig. 22 to disengage the bevel lock.
3. Tilt the cuttinghead left until it stops on the plate (A) Fig. 23.
4. To adjust, loosen the pin locking set screws (D) Fig. 23 (shown from the rear, the screw is located on the side of the
trunnion between two metal ribs) and rotate the bushing (C) until the red pointer (B) Fig. 19 is at the proper angle. Rotate
the bushing clockwise to decrease and counterclockwise to increase the bevel angle. Tighten screws (D) securely.
Make sure that the fence is clear of the
guard and blade before operating the
saw.
Fig. 22
A
DISCONNECT MACHINE FROM POWER
SOURCE.
D
A
C
D
A
Fig. 23
NOTE:
The right bushing adjustment is opposite the
left.
A
C
Fig. 25