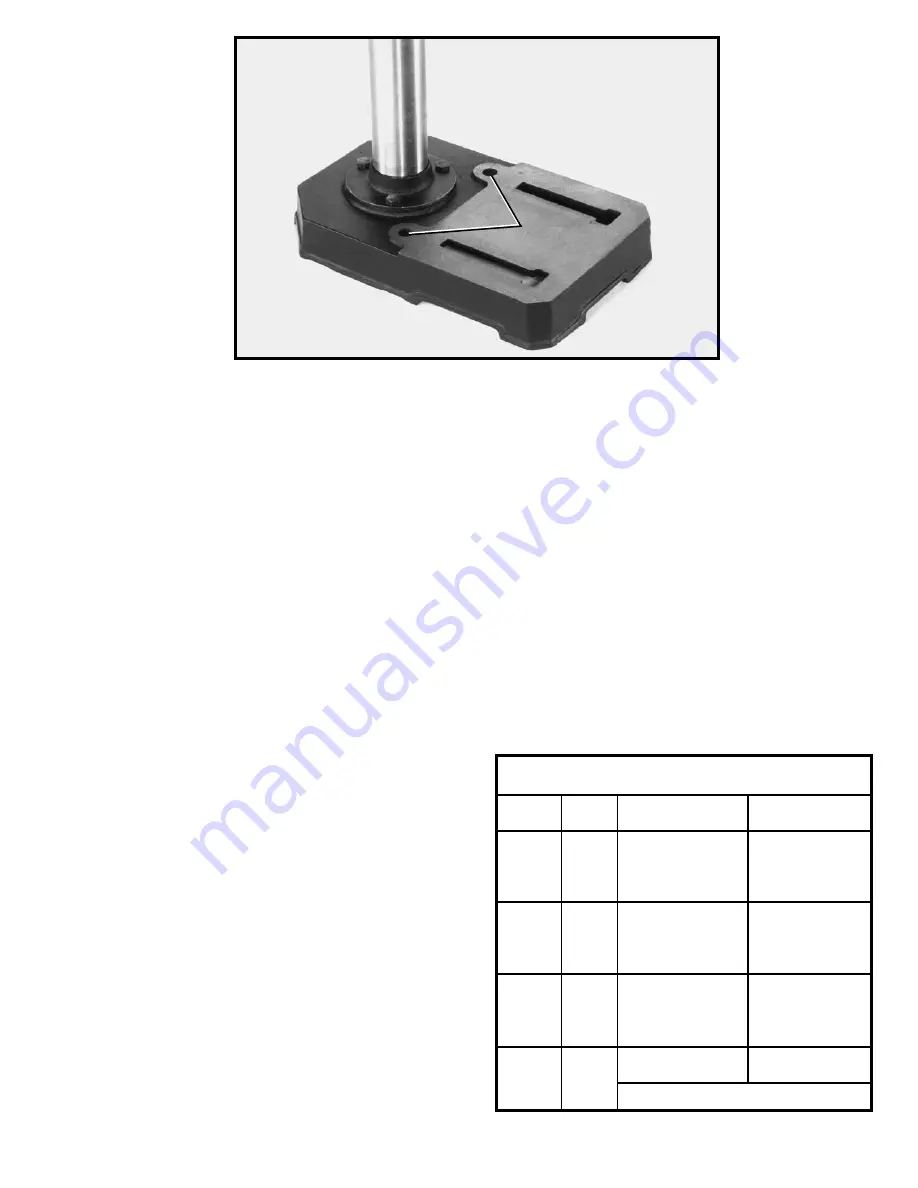
7
Use proper extension cords. Make sure your extension
cord is in good condition. When using an extension
cord, be sure to use one heavy enough to carry the
current to your tool. An undersized cord will cause a
drop in line voltage resulting in loss of power and
overheating. Fig. 15 shows the size cord to use
depending on cord length.
If in doubt, use the next heavier gauge. The smaller the
gauge number, the larger the cord size. Use only 3 wire
extension cords which have 3-prong grounding type
plugs and 3-pole receptacles which will accept the tools
plug.
Fig. 15
FASTENING DRILL PRESS TO
SUPPORTING SURFACE
If during operation there is any tendency for the drill press to tip over, slide or walk on the supporting surface, the drill
press base must be secured to the supporting surface with fasteners through the two holes (A) Fig. 14, located in the
drill press base.
CONNECTING DRILL PRESS TO POWER SOURCE
POWER CONNECTIONS
A separate electrical circuit should be used for your tools. This circuit should not be less than #12 wire and should be
protected with a 20 Amp fuse. Have a certified electrician replace or repair a damaged or worn cord immediately.
Before connecting the motor to the power line, make sure the switch is in the “OFF” position and be sure that the
electric current is of the same characteristics as stamped on motor nameplate. Running on low voltage will damage
the motor.
Fig. 14
EXTENSION CORDS
A
MINIMUM GAUGE EXTENSION CORD
RECOMMENDED SIZES FOR USE WITH STATIONARY ELECTRIC TOOLS
Ampere Volts Total Length of Gauge of
Rating Cord in Feet Extension Cord
0-6 120 up to 25
18 AWG
0-6
120 25-50 16 AWG
0-6 120 50-100 16 AWG
0-6 120 100-150 14 AWG
6-10 120 up to 25 18 AWG
6-10 120 25-50 16 AWG
6-10 120 50-100 14 AWG
6-10 120 100-150 12 AWG
10-12 120 up to 25 16 AWG
10-12 120 25-50 16 AWG
10-12 120 50-100 14 AWG
10-12 120 100-150 12 AWG
12-16 120 up to 25 14 AWG
12-16 120 25-50 12 AWG
12-16 120
GREATER THAN 50 FEET NOT RECOMMENDED
Содержание 11-900
Страница 15: ...15 NOTES ...