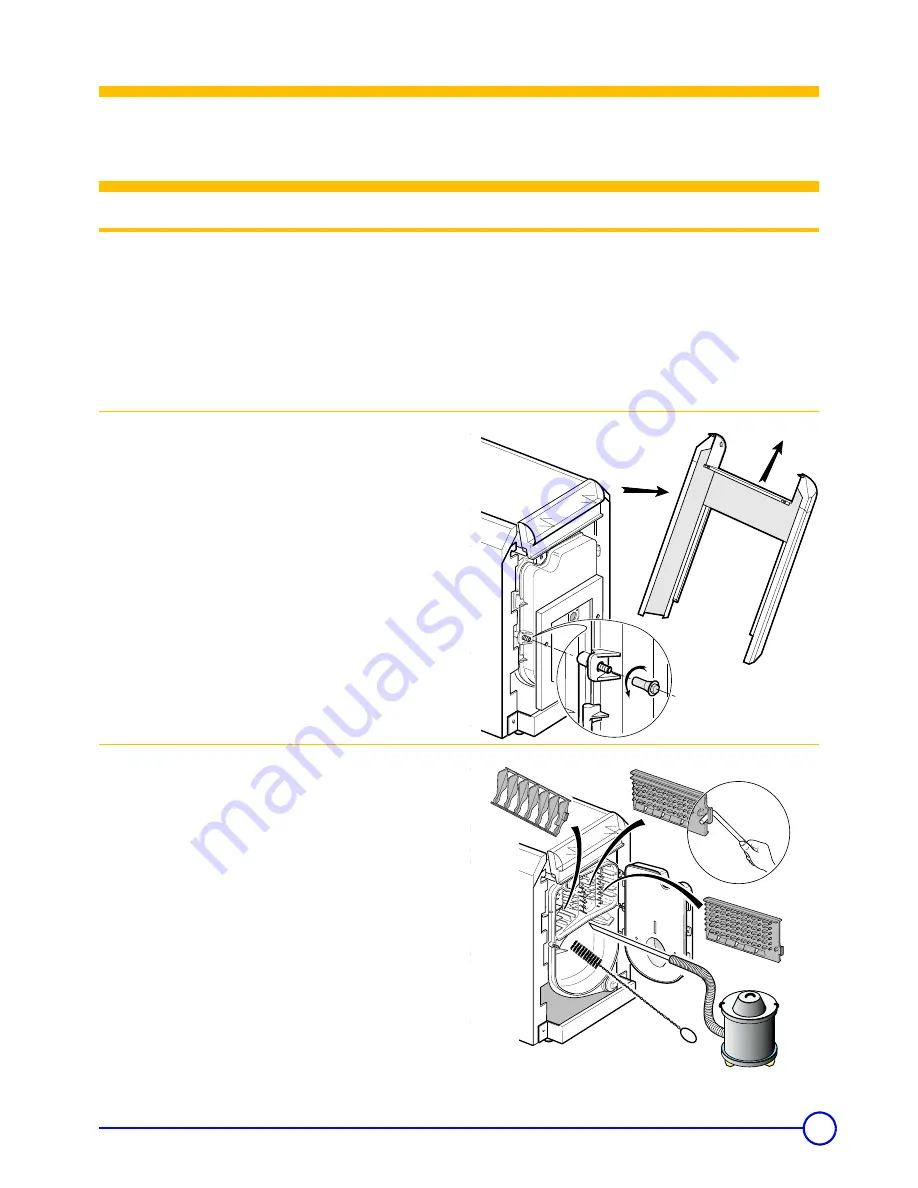
33
21/08/06 - 94863106 - 82274096E
GT 210 A
Electrical connections
See the specific instructions supplied with the control panel of the
boiler.
Maintenance
1 Boiler
Draining
We advise you against draining the installation, unless it is absolutely
necessary. Check the water level in the installation regularly and top
up if required, making sure you do not suddenly add cold water into
a hot boiler.
Cleaning
Please note that an efficient boiler is a boiler with clean
exchange surfaces.
The boiler should be cleaned as and when required,
at least once a
year
, depending upon applicable regulations and specific needs.
The operation should not be required more than a few times each
season and should not involve large quantities of water. Otherwise,
look for the leak and repair it immediately.
The operations described below shall only be performed
with the boiler and power supply off.
To have access to the exchange surfaces:
• take off the front of the casing,
• open the door by unscrewing the two flanged nuts (17 mm wrench).
• remove the convection accelerators in the flues of the boiler with the
supplied removal hook
• carefully sweep the flues with the brush supplied for that purpose
• brush out the furnace as well
• vacuum the soot from beneath the flues and in the furnace with a
sweeping brush or a vacuum cleaner with a tube diameter less than
11/2
• put back the convection accelerators
• close the door and put back the front panel.
Refer to the instructions supplied with the burner for burner
maintenance.
1
2
3
Warning
Label all wires prior to disconnecting when servicing
controls. Wiring errors can cause improper and dangerous
operation. Verify proper operation after servicing.