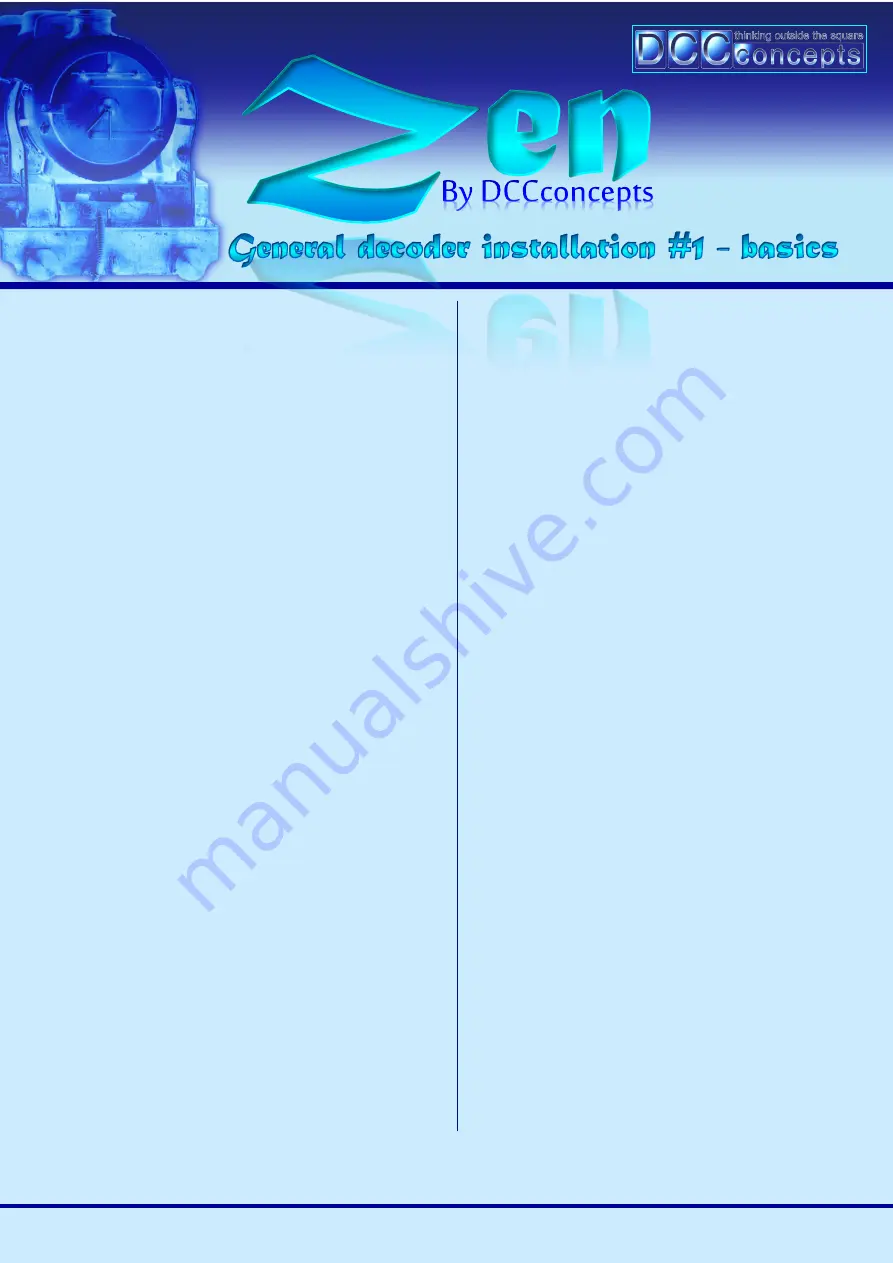
DCCconcepts Pty Ltd, 3/13 Lionel St., Naval Base WA 6165 Australia. * www.dccconcepts.com * +61 8 9437 2470 * [email protected]
Joining wires to each other… to the motor, the chassis.
and tips for reliably connecting them in other places,
(some of which hate solder) but that will still need them!
Basically the procedure for all stripping and tinning
is as we have already described. Stripping slightly
long, twisting, tinning then cutting is the best way to
guarantee a nice clean wire ends and safe joints.
Joining two wires:
If two wires are to be joined, then hold one steady on the
bench and add flux to it again. Before joining two wires,
we need to think about proper insulation of the joint, so
add about 7mm of fine heat-shrink to the second wire
before you solder them together.
Please note: Less is more when it comes to solder. If you
are using our S179 it will flow really easily and you should
need little or no added solder. If your soldering Iron tip is
bright and clean, and the Iron hot, the entire joint should
be able to be made in less than two seconds.
There is NO need to twist wires together.. .and two pre-
stripped/tinned wires need almost NO additional solder!
Just add flux, hold together and with a clean and shiny
soldering Iron tip, apply heat... The whole process should
ideally take one second, and always take less than two.
Always use fine heat-shrink on any joint. It is the ONLY
way to guarantee zero short circuits in wire joints. Note:
These wires are small and old or young, you will find add-
ed light and some magnification really will help.
Adding wires to the motor brushes:
The motor wires will be
Orange and Grey
.
If you have
not already done it, plan their ideal length and cut them.
Strip & tin them using the techniques already mentioned.
Most of the time, the motor brushes will be mounted into
the motor using a hard thermoplastic but that does not
mean you can use lots of heat. If there is a usable tag on
it, use it. Linger too long and the brush holder will melt or
soften and throw the brush alignment out of line.
(1) Clean the brush holder with a fibreglass brush or simi-
lar if it is not already tinned. If it is tinned, add a tiny bit
of flux and remove old solder. Use a “solder mop” if
you have one to absorb the excess.
(2) Add flux (a cotton bud is best). Hold the wire onto the
brush holder as flat as possible. Make sure the solder-
ing Iron tip is clean, pick up a TINY bit of solder on the
tip and apply heat to the already fluxed joint area.
(3) The solder should flow immediately. Remove the tip of
the soldering Iron as soon as it does, hold the wire still
for a second or so and the joint will harden.
(4) Using the correct solder and a quality flux and of
course also using a clean soldering Iron tip, this whole
process should take less than TWO seconds.
Time to talk about soldering wires to power pickups and
heat sensitive parts…. and to “Un-Solderable bits” too.
Power pickups are usually Phosphor Bronze.
Phosphor bronze is used because its springier than brass
and has good wearing characteristics, but it’s springiness
will be lost if you heat it too much… so be careful.
Its often attached to some heat sensitive plastic that’s
within the chassis. so what’s the best way to handle it?
Pre-tin any wire you will want to connect to it.
Before you start, clean it with a fibreglass brush or similar
to expose bright, bare fresh metal (even clean-looking
phosphor bronze has an oxide layer). Add no-clean flux
and tin with a tiny amount of our 179 solder. Be quick.
Add more flux, hold the wire to it and just touch with the
Iron - solder will flow and the wire will be neatly attached.
Attaching wires to the chassis for power collection is
often required - but how can you manage it, because
Chassis metal is an alloy that just can’t be soldered!
The metal used in chassis’ is a “low temp” casting alloy.
In an ideal world it would be Pewter but much lower cost
alloys have almost always been used, and now that
health and safety rules have excluded elements like
Lead, what we now have is usually a combination of Zinc,
Antimony, magnesium, Aluminium and Cadmium.
As a result is will NOT take solder, no matter how you try!
However you’ll often need to attach wires to it for
power pickup / other purposes, so how do you do it?
(1) Drill and tap. Also not quite so easy as the alloy has a
tendency to “grab” at taps and snap them. If you want
to tap it use a lubricant like kerosene and keep it wet.
(2) Drill and screw or drill and plug. Much more practical
for most of us. Again, lubricate when drilling. Find a
drill for a hole a bit smaller than an offcut of brass rod.
Taper the end of the rod a wee bit. Pre-tin the end of
the brass rod with flux and 179 solder ready for later.
To further prepare the hole, countersink it.
When the hole is ready, drive in the brass rod and cut
it off only a little bit above the chassis surface.
When all that is done, Hold the pre-tinned wire in the
hole, add flux and a bit more solder with a hot Iron.
The solder will fill the countersink and the wire will be
really tidily attached to the brass rod.
(3) Add a Screw to solder to. Brass is best but steel is
fine. Do as for 2, but countersink to match the screw.
File any plating off the screw head. Drive it the screw
and solder your wire to the screw head.
For detailed light function wiring and more advanced wiring ideas visit our website @ www.dccconcepts.com