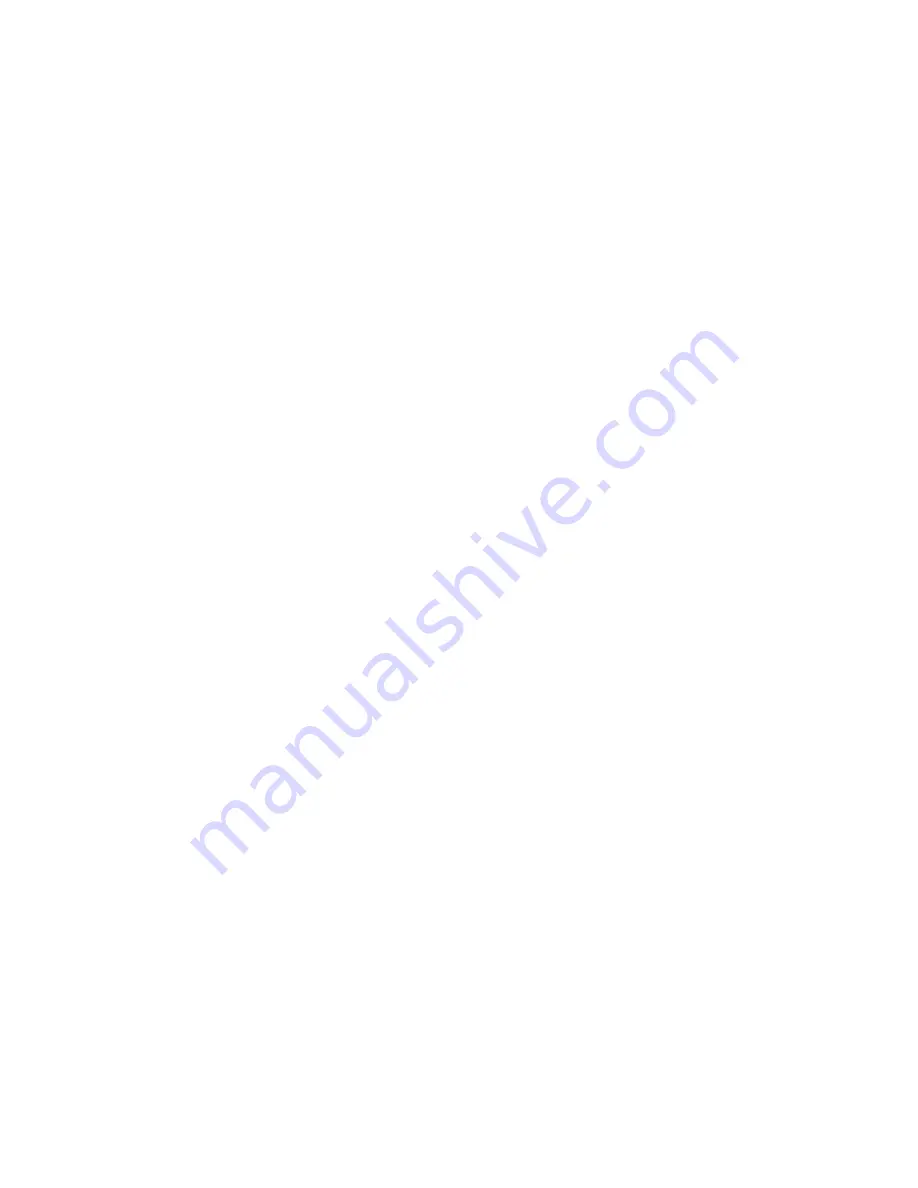
3. CALIBRATION
(cont.)
This section contains the instructions for calibrating the IL78A. Included is a functional description of
the instrument front-panel (see Figure 2). To perform calibration, proceed as follows.
Turn power ON to the IL78A DC Power input terminal (11 to 28 Vdc input) The
front-panel indicator should light green to indicate the application of dc power.
Allow 10 minutes of warmup for stabilization of transducer characteristics.
Remove the top cover of the unit to make the proper connections and adjustments.
Set the Coarse Zero
control to position 8 and the Coarse
Span control
to position 0.
Position the front panel switches to the desired settings for the application. Refer
to Figure 2 for details. If using Shunt method, refer to step (k).
(b)
(a)
(c)
the Coarse and Fine SPAN controls. If not, adjust the Symmetry control
to obtain the negative Equivalent Input value.
If dead weight calibration is not practical and the transducer calibration
data is unknown, the Equivalent Input value for the factory-installed
calibration resistor can be approximated
mv/v sensitivity rating of the transducer
known.
as follows, assuming that
and the bridge resistance
the
are
13
(m)
With the transducer unloaded, adjust the Coarse Zero control and the Fine Zero control until
the desired analog output is achieved. If greater zero authority is desired, place the front panel
Switch 7 - "Zero Adj" to the extended range. This will allow the user to obtain 100% zero offset
control. The Normal postion of switch 7 allows for approximately 25% Zero authority.
(d)
the Coarse and Fine SPAN controls. If not, adjust the Symmetry control
to obtain the negative Equivalent Input value.
If dead weight calibration is not practical and the transducer calibration
data is unknown, the Equivalent Input value for the factory-installed
calibration resistor can be approximated
mv/v sensitivity rating of the transducer
known.
as follows, assuming that
and the bridge resistance
the
are
13
(m)
Load the transducer in the positive direction with a convenient dead weight value (greater than one
half of full scale). Adjust Coarse Span for a nominal corresponding output. Adjust the PHASE control,
until a maximum output value is obtained. (Once set for your transducer, this PHASE ADJUSTMENT
step need not be repeated unless a change in cable length – or transducer – is required). Unload the
sensor and re-Zero as needed.
(e)
(f)
I
f the calibration will utilized a known "dead-weight", re-load the sensor and adjust the Coarse and
Fine Span controls for the expected analog output value. Unload - Zero and Load - Span operations
may need to be repeated for analog output precision.
Note: With sensor unloaded, activate & record "SHP" value for furture calibration verification.
If the calibration will utilize the "Shunt" calibration method, refer to step (k).
recommended calibration resistor.
the Coarse and Fine SPAN controls. If not, adjust the Symmetry control
to obtain the negative Equivalent Input value.
If dead weight calibration is not practical and the transducer calibration
data is unknown, the Equivalent Input value for the factory-installed
calibration resistor can be approximated
mv/v sensitivity rating of the transducer
known.
as follows, assuming that
and the bridge resistance
the
are
13
(g)
(m)
the Coarse and Fine SPAN controls. If not, adjust the Symmetry control
to obtain the negative Equivalent Input value.
If dead weight calibration is not practical and the transducer calibration
data is unknown, the Equivalent Input value for the factory-installed
calibration resistor can be approximated
mv/v sensitivity rating of the transducer
known.
as follows, assuming that
and the bridge resistance
the
are
13
(m)
the Coarse and Fine SPAN controls. If not, adjust the Symmetry control
to obtain the negative Equivalent Input value.
If dead weight calibration is not practical and the transducer calibration
data is unknown, the Equivalent Input value for the factory-installed
calibration resistor can be approximated
mv/v sensitivity rating of the transducer
known.
as follows, assuming that
and the bridge resistance
the
are
13
(m)
If the transducer is to be also used in the negative realm, load the transducer in
the negative direction with the same dead weight value as used in step (f) and confirm
that the dead weight reading obtained is the same, but negative polarity, as that of step
(f). If not, see steps (i) thru (j).
A Symmetry adjustment is provided to compensate for transducers that do not have
symmetrical sensitivity characteristics. This adjustment is factory set assuming
symmetrical characteristics. If step (h) indicates that a field adjustment is necessary,
proceed as follows.
recommended calibration resistor.
the Coarse and Fine SPAN controls. If not, adjust the Symmetry control
to obtain the negative Equivalent Input value.
If dead weight calibration is not practical and the transducer calibration
data is unknown, the Equivalent Input value for the factory-installed
calibration resistor can be approximated
mv/v sensitivity rating of the transducer
known.
as follows, assuming that
and the bridge resistance
the
are
13
(h)
(i)
(m)
Calibration IL78A.3
AC Strain Gage Conditioner
Module
IL78A