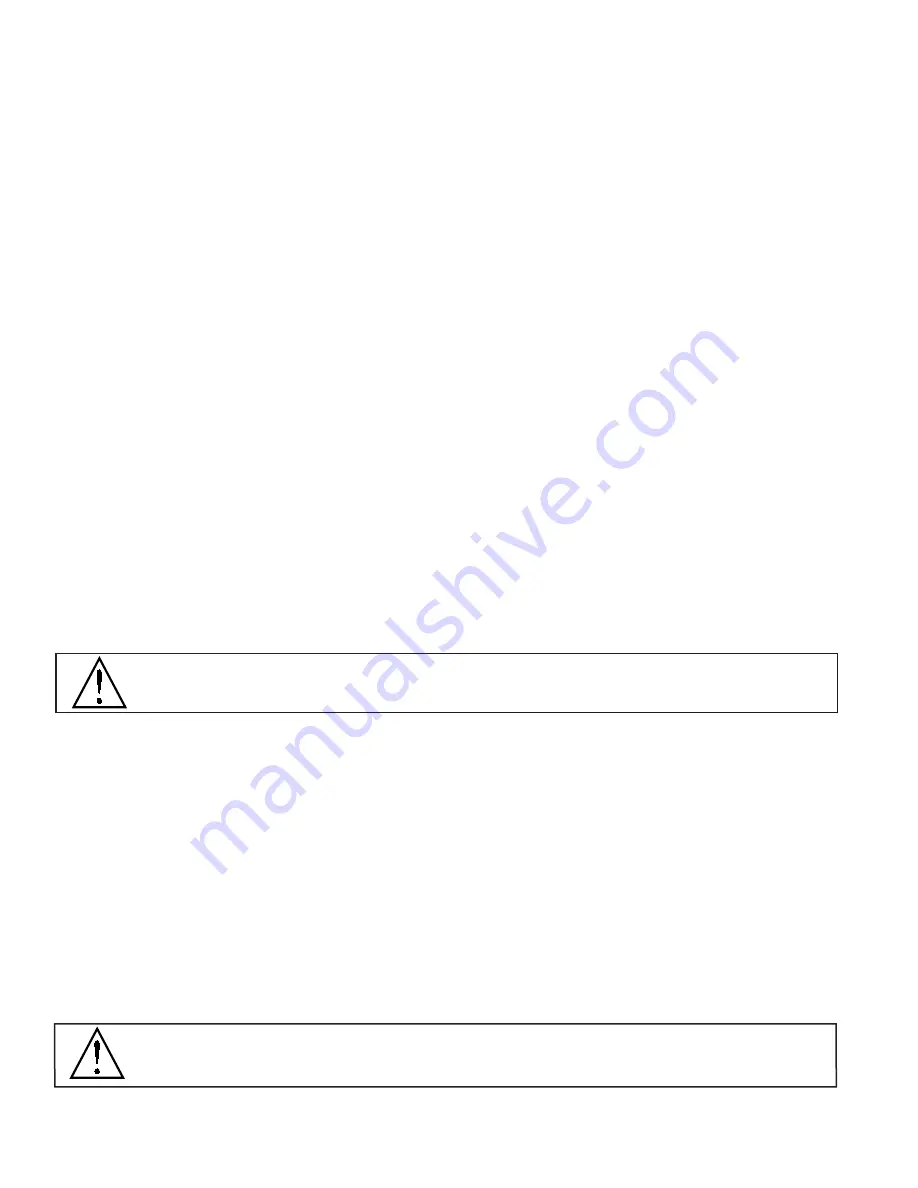
14
2.5 Humidifi er Piping
The optional humidifi er offered on Mini Ceiling systems is a steam generator type with a disposable
cylinder. The humidifi er makeup water should be brought to the humidifi er through the fi eld connection
opening using 1/4” copper tubing. A compression fi tting is provided at the humidifi er. A shutoff valve
should be provided outside the unit to allow disconnection of service. An in-line water pressure
regulator and strainer should be installed. Water pressure should be set between 30 and 80 PSI.
The humidifi er has a drain at the bottom which is factory piped to the main condensate drain line.
The dispersion tube also has a drain line. No additional fi eld piping is required.
2.6 Leak
Testing
No installation is complete until the entire system has been thoroughly checked for leaks. This
includes checking refrigerant tubing, fl are fi ttings, pressure controls, shrader fi ttings and compressor
rotalock service valves.
In addition to the refrigeration system, check all condenser water lines, humidifi er makeup lines,
condensate lines, condensate pumps, chilled water lines, centrifugal pumps and fl uid coolers as
applicable.
When handling and recovering refrigerant, it is not permissible to release refrigerant into the
atmosphere. Many leak-test methods recommended in the past are no longer possible. Current
standard practices must be used.
Pressurize system circuit to 150 PSIG (1034kPa) by using dry nitrogen with a trace of refrigerant.
Check the entire system for leaks with suitable leak fi nder, (per local code) including but not limited
to all braze joints, caps and fi ttings, and fl are nuts on both fi eld and factory furnished components.
After completion of leak testing, release test pressure and pull a vacuum on the system.
Tightening of fi ttings and valves is the responsibility of the installing contractor.
2.7 Evacuation
Evacuate the refrigerant lines, condenser coil, and evaporator coil to 250 microns or lower (a micron
gauge and 2-stage vacuum pump are required). Valve off and turn off the vacuum pump and wait for
at least 15 minutes to make sure the micron gauge reading does not go back up above 700 microns.
If it does, re-start the vacuum pump and evacuate until the system reaches 250 microns. If the system
still does not hold the pressure below 700 microns the system needs to be rechecked for leaks.
After the system has been satisfactorily evacuated the unit(s) can be charged with refrigerant.
Connect the pressure gauge manifold set to the high and low ports near the compressor, connect
the charging line to the refrigerant tank and set it for liquid feed. Open the refrigerant tank valve
and purge the line at the manifold, then open the high side valve on the manifold only, and allow
the refrigerant fl ow until the system pressure equalize, at this point the system will have 75 to 80%
of the total refrigerant charge. Start the blower and then the compressor checking the operating
pressure and temperatures.
Do not apply power to the compressor when in a vacuum.