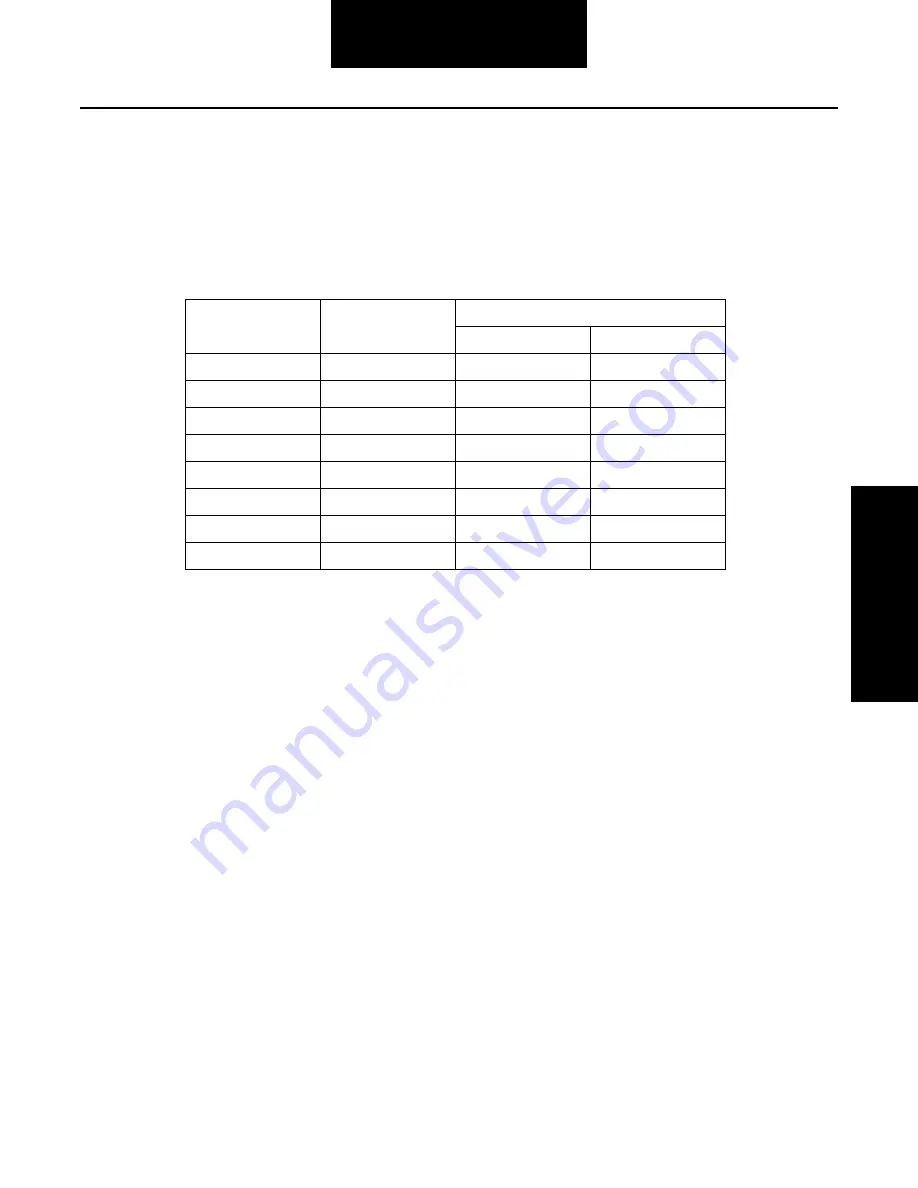
12
Installation Techniques
Compound Angle
Vibrations
Angle Size
The magnitude of a vibration created by a universal joint operating angle is proportional to the size of the universal joint operating
angle. Spicer Engineers recommend true universal joint operating angles of 3 degrees or less.
Obtain the true universal joint operating angle, as explained above, and if it is greater than 3 degrees, compare it to this chart.
The angles shown on this chart are the maximum universal joint operating angles recommended by Spicer Engineers and are di-
rectly related to the speed of the driveshaft. Any universal joint operating angle greater than 3 degrees will lower universal joint
life and may cause a vibration. Remember to check maximum safe driveshaft RPM by using the Spicer Safe Operating Speed Cal-
culator.
Driveshaft Maximum
Interaxle
RPM
Operating Angle
Parallel
Intersecting
5000
3.2°
-
-
4500
3.7°
-
-
4000
4.2°
3.8°
3.8°
3500
5.0°
4.4°
4.4°
3000
5.8°
5.1°
4.8°
2500
7.0°
6.0°
4.8°
2000
8.7°
6.0°
4.8°
1500
11.5°
6.0°
4.8°
Содержание ZSP
Страница 64: ......
Страница 66: ......
Страница 67: ...DRIVELINE INSTALLATION J3311 1 DSSP AUGUST 2008 Supersedes J3311 1 HVTSS Dated February 2005 ...
Страница 89: ......
Страница 130: ......
Страница 133: ......
Страница 135: ...7 31 1200503 ...
Страница 136: ...7 32 1200503 ...
Страница 139: ...7 35 1200503 ...
Страница 140: ...7 36 1201002 ...
Страница 142: ...7 66 ...
Страница 143: ...7 65 ...
Страница 144: ......
Страница 146: ......
Страница 147: ......
Страница 148: ......
Страница 149: ......
Страница 150: ......
Страница 151: ......