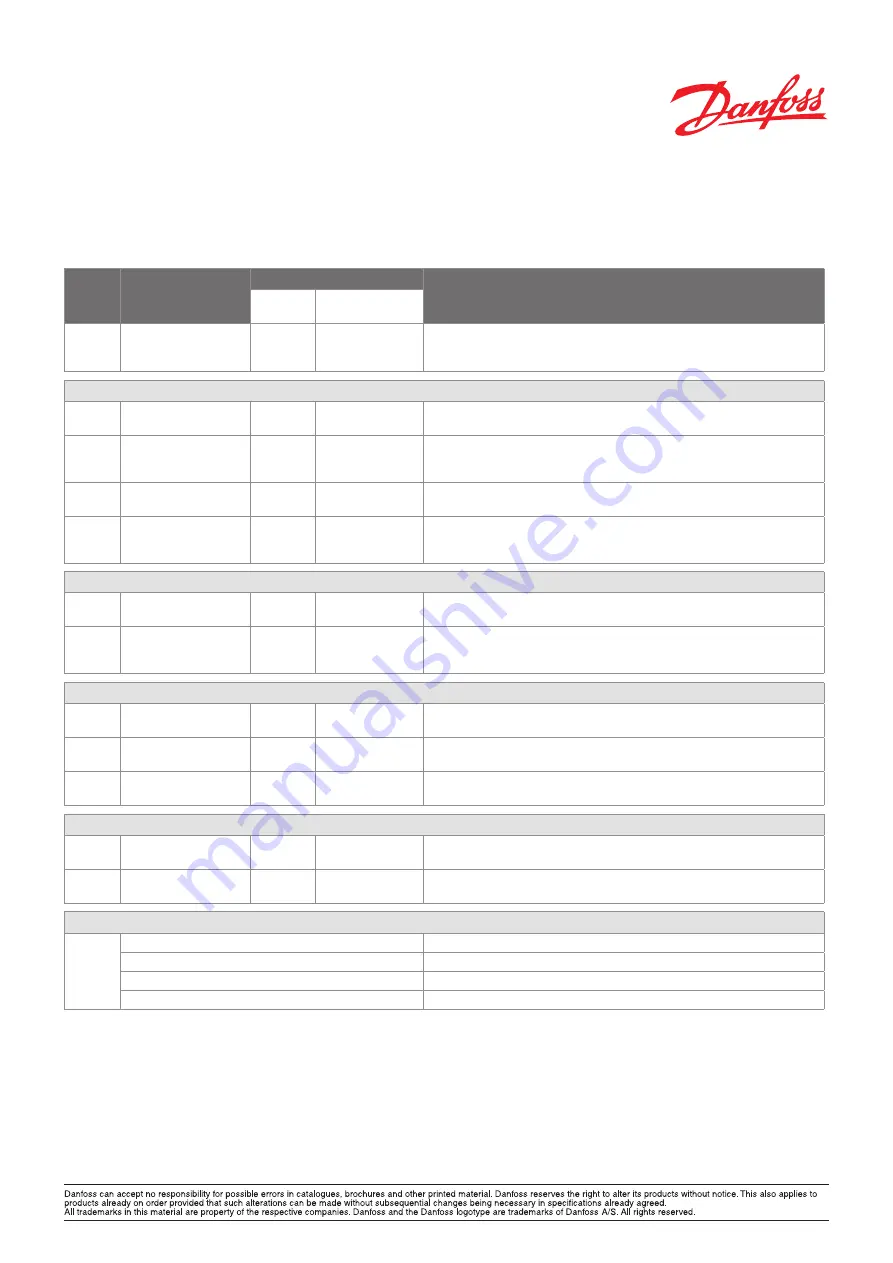
Danfoss Drives
, Ulsnaes 1, DK-6300 Graasten, Denmark, Tel. +45 74 88 22 22, Fax +45 74 65 25 80, www.danfoss.com/drives • E-mail: [email protected]
MF004A02
VLT® is a trademark of Danfoss A/S
Produced by KKM 2007.10
Programming for No-Flow detection
is simplified with a number of para-
meters that are pre-programmed into
the drive. Prior to programming this
feature, commission the drive by
using the parameters in the Quick
Menu Q2 Quick Set-Up. Then perform
the following steps for programming
No-Flow detection:
Par.#
Description
Settings
Comments
Factory
setting
Recommended
setting
22-20
Low Power Auto Set-up Disable
Enable
Close the outlet valve for the pump before starting Auto Set-up. Select Enable
and follow the instruction on the LCP. After Auto Set-up is complete, open the
pump outlet valve.
The following parameters are accessed through the Main Menu and will be stored after pressing the [OK] key to save the results after the auto-tuning
22-33
Low Speed
[Hz]
When Low Power Auto Set-up is used, 50% of the drive’s maximum frequency
will be stored here. This can be manually edited, if desired.
22-34
Low Speed Power [kW]
When Low Power Auto Set-up is used, the output power measured under
no-flow conditions at 50% speed will be stored here. This can be manually
edited, if desired.
22-37
High Speed
[Hz]
When Low Power Auto Set-up is used, 85% of the drive’s maximum frequency
will be stored here. This can be manually edited, if desired.
22-3
High Speed Power [kW]
When Low Power Auto Set-up is used, the output power measured under
no-flow conditions at 85% speed will be stored here. This can be manually
edited, if desired.
These parameters are used after Auto Set-up and the No-Flow feature is operating
22 - 30
No-Flow Power
When the drive is running, this parameter will show the power level that will
be interpreted as producing no flow at the current motor speed.
22 - 31
Power Correction
Factor
100%
110%
This parameter is used to raise or lower the no-flow power curve to the
percentage entered here. Values above 100% help ensure the drive reliably
detects no-flow.
The following parameters determine the action that the drive will take if a no flow condition is detected
22-21
Low Power
Detection
Disable
Enable
To activate no-flow based on power
22-23
No-Flow Function
Off
Sleep Mode/
Warning/Alarm
Select action
22-24
No-Flow Delay
10 sec.
Set the time delay before the drive will perform the No-Flow Function.
Generally set longer than the decel ramp time.
The following parameters give and indication to a BMS if a no flow condition is detected
5-40
Function Relay
[190] No-Flow
Program one of the relays to selection [190], No-Flow. The selected relay will
be activated when No-Flow occurs.
Digital Output
[190] No-Flow
A digital output can be used to indicate a no flow condition. Use the
parameter that sets the function of the desired digital output.
The following are used if No-Flow is reported via serial communications
Protocol
Warning Word
BACnet
BV:77 No Flow
LonWorks
nvoWarningword Bit 37
Modbus RTU
TU
Register 16930 Bit 6 = 1
Programming No-Flow detection