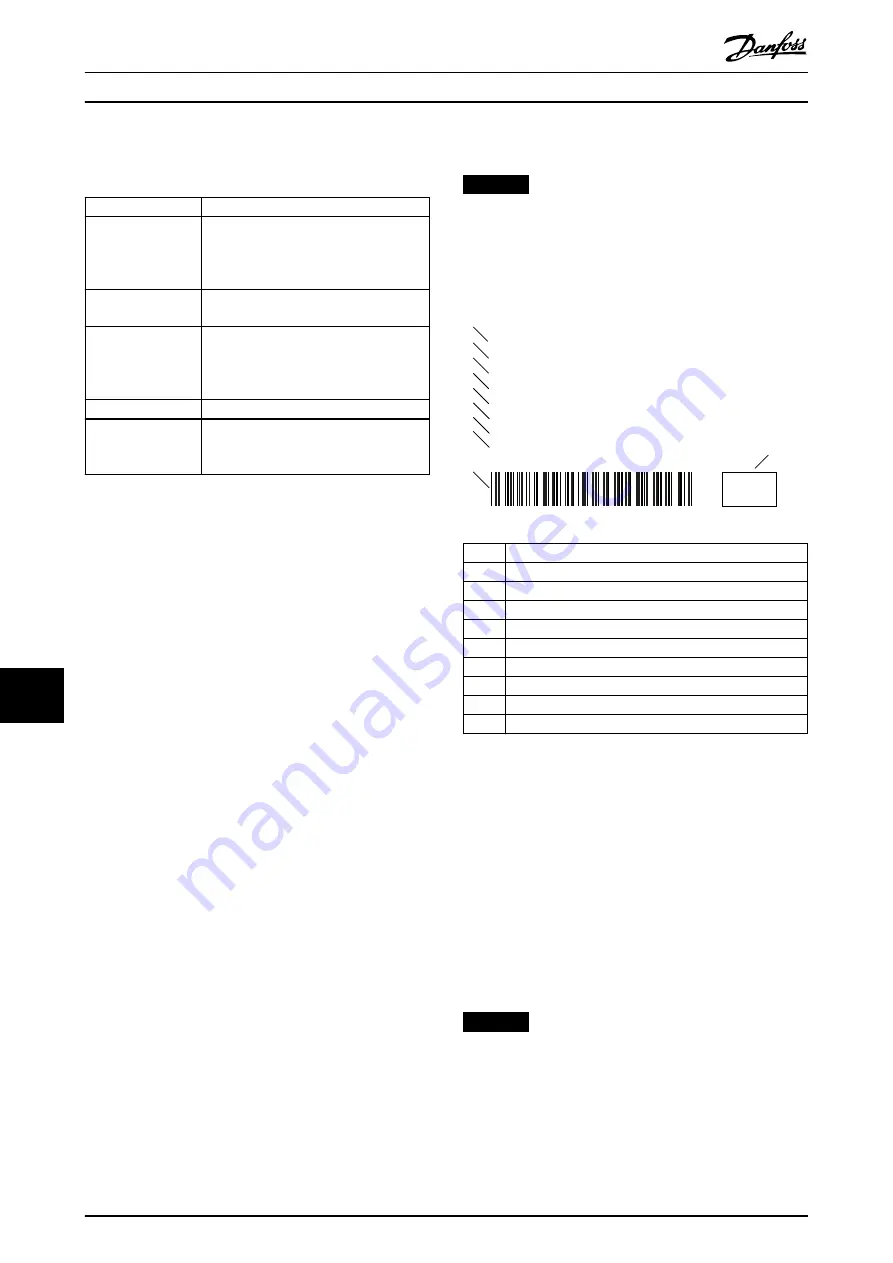
11.2.4 General Specifications and
Environmental Conditions
Protection rating
IP20
Vibration test
Random vibration: 1.14 g (2h/axis
according to EN 60068-2-64)
Sinusoidal vibration: 0.7 g (2h/axis
according to EN 60068-2-6)
Maximum relative
humidity
Storage/transport and stationary use:
5–93% (non-condensing)
Ambient
temperature range
5–50
°
C operating temperature
(24 hour average maximum 45
°
C)
Transport: -25 to +70
°
C
Storage: -25 to +55
°
C
Installation elevation Maximum 1000 m above sea level
EMC standard for
emission and
immunity
EN 61800-3
Table 11.8 General Specifications and Environmental Conditions
SAB
11.3 Cables
NOTICE
See the
VLT
®
Integrated Servo Drive ISD
®
510 System
Design Guide
for cable dimensions and drawings.
All cables supplied by Danfoss have a nameplate as per
the example in
.
130BE658.10
1
2
3
4
5
6
7
8
9
10
Danfoss ISD 510 Hybrid xxxx Cable
Length: xxxx
Ordering no. 175Gxxxx Rev. x.
1
7
5
G
8
9
X
X
Specification no. 175Rxxxx Rev. xxx.
Signal rating Ethernet: 2 x 2 x AWG24 300V
yy.mm.dd
Power rating: 5 x 2.5mm 1000V 18A
2
Signal rating: 2 x 0.5mm 300V
2
1
Cable type
2
Ordering code
3
Revision of specification
4
Manufacturing date
5
Length
6
Power rating
7
Signal rating
8
Signal rating for Ethernet
9
Barcode
10
Manufacturer logo
Illustration 11.11 Example of a Cable Nameplate
11.4 Storage
Store the servo drives and the SAB in a dry, dust-free
location with low vibration (v
eff
≤
0.2 mm/s).
Do not store the packaged system components on top of
each other.
The storage location must be free from corrosive gases.
Avoid sudden temperature changes.
11.4.1 Long-Term Storage
NOTICE
To recondition the electrolytic capacitors, servo drives
and SABs not in service must be connected to a supply
source once per year to allow the capacitors to charge
and discharge. Otherwise the capacitors could suffer
permanent damage.
Specifications
VLT
®
Integrated Servo Drive ISD
®
510 System
92
Danfoss A/S © 12/2015 All rights reserved.
MG75K102
11
11
Содержание VLT Integrated Servo Drive ISD 510 System
Страница 2: ......
Страница 101: ...Index Operating Instructions MG75K102 Danfoss A S 12 2015 All rights reserved 99...