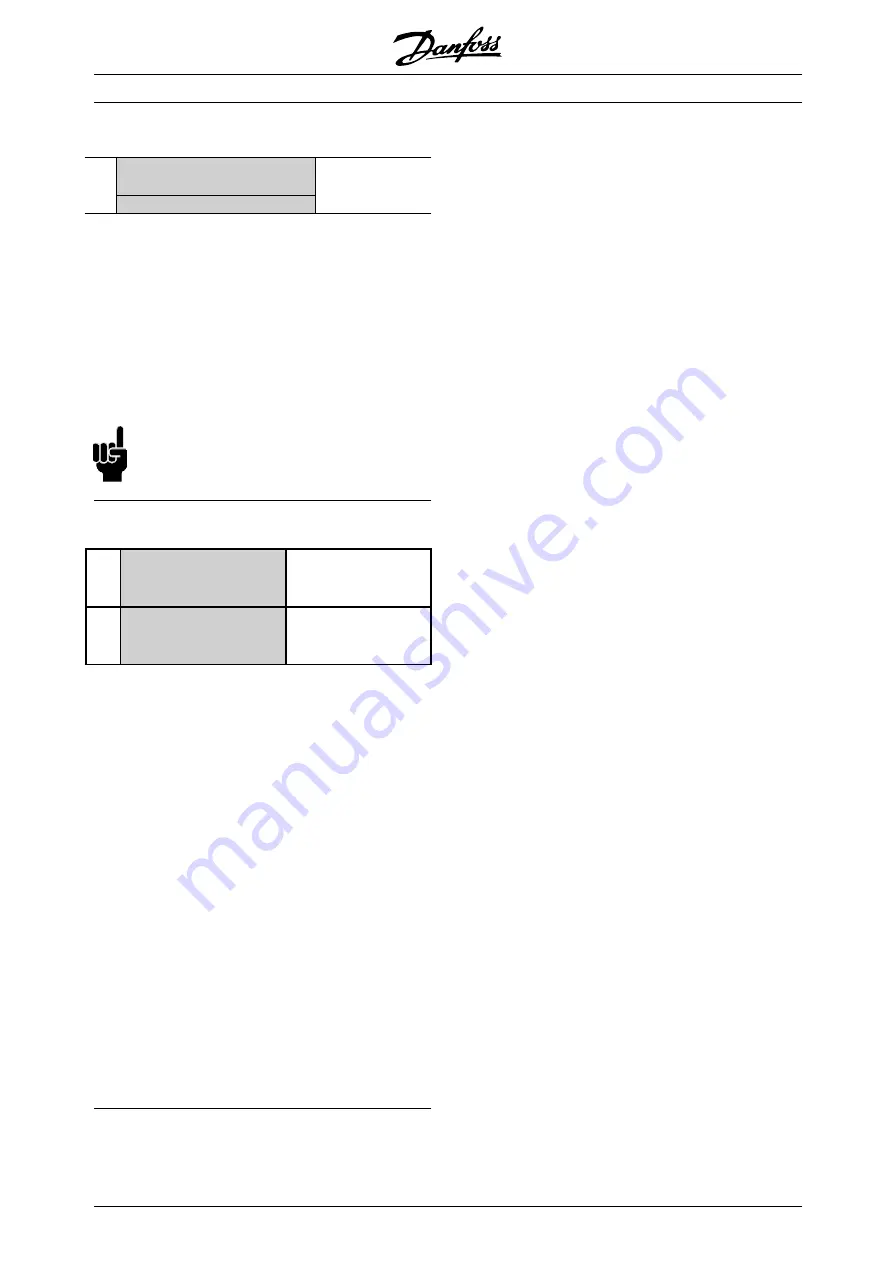
VLT
®
FCD Series
■
Brake resistor
No.
81 (optional
function)
82 (optional
function)
Brake resistor
terminals
R-
R+
The connection cable to the brake resistor must
be screened/armoured. Connect the screen to the
metal cabinet of the frequency converter and to the
metal cabinet of the brake resistor by means of
cable clamps. Dimension the cross-section of the
brake cable to match the brake torque.
See chapter
Dynamic Braking
in the
Design Guide
MG.90.FX.YY
for dimensionering of brake resistors.
NB!:
Please note that voltages up to 850 V
DC occur on the terminals.
■
Control of mechanical brake
No.
122 (optional
function)
123
(optional
function)
MBR+
MBR-
Mechanical brake
(UDC=0.45 X Mains
Voltage) Max 0.8 A
In lifting/lowering applications you need to be able
to control an electromagnetic brake. The brake
is controlled using the special mechanical brake
control/supply terminals 122/123.
When the output frequency exceeds the brake cut
out value set in par. 138, the brake is released if the
motor current exceeds the preset value in parameter
140. When stopping the brake is engaged when
the output frequency is less than the brake engaging
frequency, which is set in par. 139.
If the frequency converter is at alarm status
or in an overvoltage situation the mechanical
brake is cut in immediately.
If not using the special mechanical brake control/supply
terminals (122-123), select
Mechanical brake control
in parameter 323 or 341 for applications with
an electromagnetic brake.
A relay output or digital output (terminal 46)
can be used. See
Connection of mechanical
brake
for further details.
MG.04.B7.02 - VLT is a registered Danfoss trademark
18