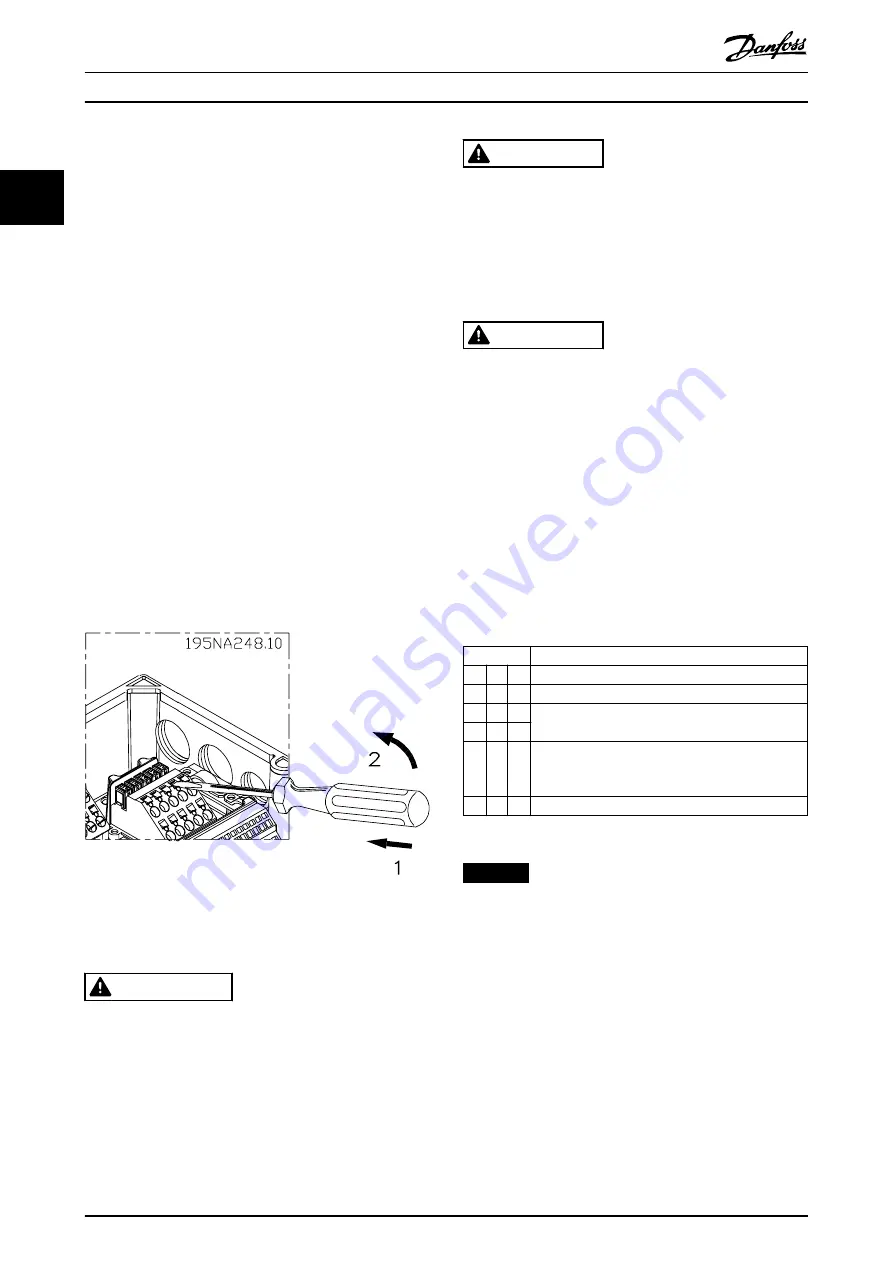
For both small and large unit, the service switch is
optional. The switch is shown mounted on the motor side.
Alternatively, the switch can be located on the mains side,
or omitted.
For the large unit, the circuit breaker is optional. The large
unit can be configured with either service switch or circuit
breaker, not both. The illustration shown is not config-
urable in practice, but is displayed to show the respective
positions of components only.
2.4.3 Terminal Types
Motor, control, and mains terminals are spring loaded
(CAGE-CLAMP) type.
1.
Open the contact by inserting a small screwdriver
into the slot above the contact, as shown in
.
2.
Insert the stripped wire into the contact.
3.
Remove the screwdriver to fasten the wire into
the contact.
4.
Ensure that the contact is firmly established and
not loose. Loose wiring can result in equipment
faults or injury.
Illustration 2.14 Opening the Terminals
2.4.4 Motor Connection
WARNING
INDUCED VOLTAGE
Run output motor cables from multiple frequency
converters separately. Induced voltage from output
motor cables run together can charge equipment
capacitors even with the equipment turned off and
locked out. Failure to run output motor cables separately
could result in death or serious injury.
CAUTION
WIRING ISOLATION
Run input power, motor wiring, and control wiring in
three separate metallic conduits. Alternatively, use
separated shielded motor and control cables for high
frequency noise isolation. Failure to isolate power, motor
and control wiring can result in sub-optimal performance
of the frequency converter and associated equipment.
CAUTION
MOTOR PROTECTION
Protection against motor overload is not included in the
factory setting. If this function is desired, set
parameter 1-90 Motor Thermal Protection
to trip or
warning. Refer to the VLT
®
Decentral Drive FCD 302
Programming Guide MG04GXYY
for further information.
•
Connect the motor to terminals 96, 97, 98.
•
Connect earth to PE-terminal.
•
Make sure that the screen of the motor cable is
properly earthed at both ends (motor and
frequency converter).
•
For correct dimensioning of cable cross-section,
see
No.
96 97 98 Motor voltage 0-100% of mains voltage
U
V W 3 wires out of motor
U1 V1 W1
6 wires out of motor
W2 U2 V2
U1 V1 W1 6 wires out of motor, Star connected
Connect U2, V2, W2 separately (optional terminal
block)
PE
Earth connection
Table 2.1 Motor Terminals
NOTICE
Do not install power factor correction capacitors
between the frequency converter and the motor.
Do not wire a starting or pole-changing device between
the frequency converter and the motor.
Parallel connection of motors
The frequency converter can control several parallel-
connected motors. The total current consumption of the
motors must not exceed the rated output current I
M,N
for
the frequency converter.
Installation
VLT
®
Decentral Drive FCD 302
18
Danfoss A/S © 05/2016 All rights reserved.
MG04F402
2
2