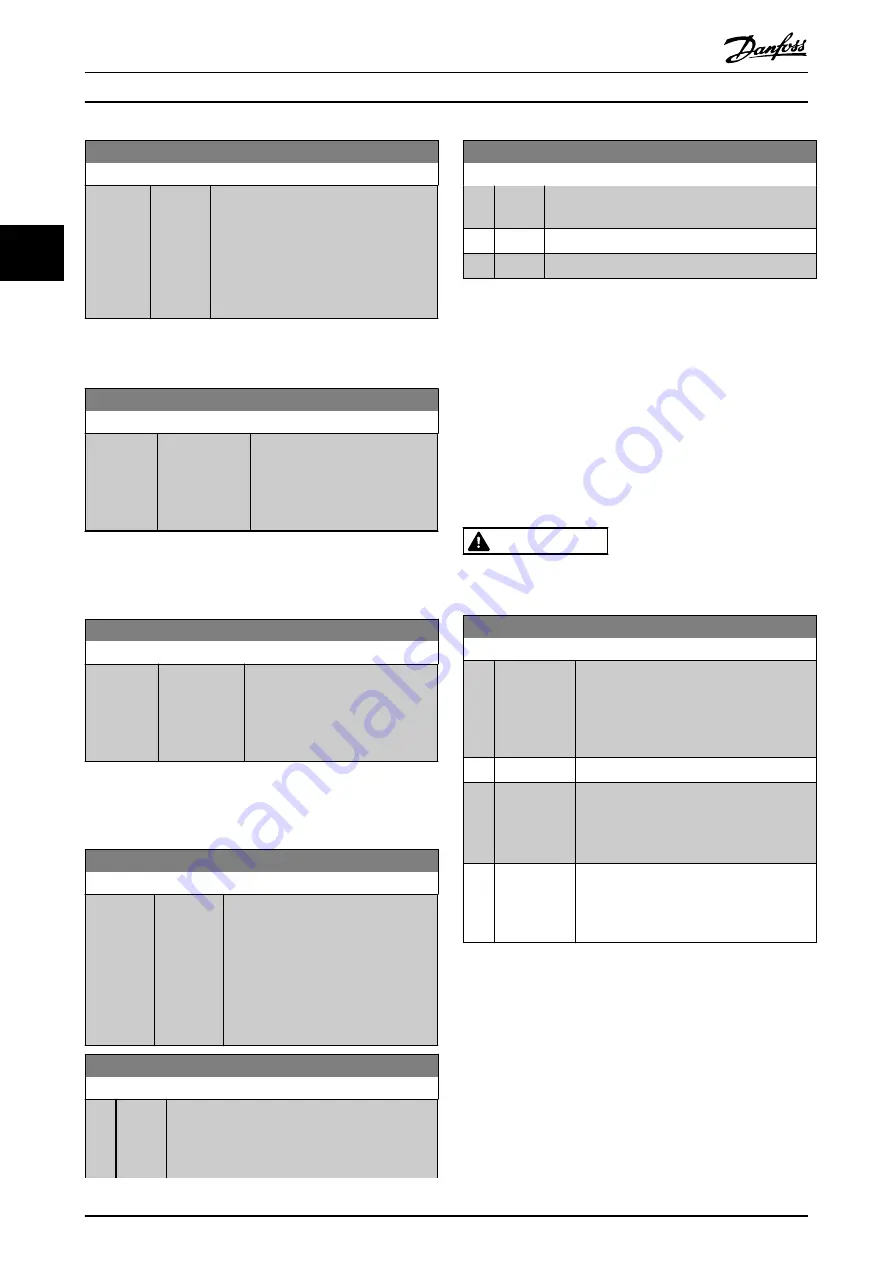
1-23 Motor Frequency
Range:
Function:
Size
related
*
[20 -
1000 Hz]
Select the motor frequency value from
the motor nameplate data. For 87 Hz
operation with 230/400 V motors, set the
nameplate data for 230 V/50 Hz. Adapt
4-13 Motor Speed High Limit [RPM]
and
3-03 Maximum Reference
to the 87 Hz
application.
NOTE
This meter cannot be changed while the motor is running.
1-24 Motor Current
Range:
Function:
Size
related
*
[ 0.10 -
10000.00 A]
Enter the nominal motor current
value from the motor nameplate
data. This data is used for
calculating motor torque, motor
thermal protection etc.
NOTE
This parameter cannot be changed while the motor is
running.
1-25 Motor Nominal Speed
Range:
Function:
Size related
*
[100 - 60000
RPM]
Enter the nominal motor speed
value from the motor nameplate
data. This data is used for
calculating automatic motor
compensations.
NOTE
This parameter cannot be changed while the motor is
running.
1-26 Motor Cont. Rated Torque
Range:
Function:
Size
related
*
[0.1 -
10000 Nm]
Enter the value from the motor
nameplate data. The default value
corresponds to the nominal rated
output. This parameter is available
when
is set to
[1] PM, non salient SPM
, i.e. the
parameter is valid for PM and
nonsalient SPM motors only.
1-28 Motor Rotation Check
Option:
Function:
Following installation and connection of the
motor, this function allows the correct motor
rotation direction to be verified. Enabling this
function overrides any bus commands or digital
1-28 Motor Rotation Check
Option:
Function:
inputs, except External Interlock and Safe Stop (if
included).
[0]
*
Off
Motor Rotation Check is not active.
[1]
Enabled Motor Rotation Check is enabled.
NOTE
Once the motor rotation check is enabled the display
shows: “Note! Motor may run in wrong direction”.
Pressing [OK], [Back] or [Cancel] will dismiss the message
and display a new message: “Press [Hand On] to start the
motor. Press [Cancel] to abort”. Pressing [Hand On] starts
the motor at 5 Hz in forward direction and the display
shows: “Motor is running. Check if motor rotation direction
is correct. Press [Off] to stop the motor”. Pressing [Off]
stops the motor and resets
. If
motor rotation direction is incorrect, two motor phase
cables should be interchanged.
WARNING
Mains power must be removed before disconnecting
motor phase cables.
1-29 Automatic Motor Adaptation (AMA)
Option:
Function:
The AMA function optimizes dynamic motor
performance by automatically optimizing
the advanced motor
to
) while the
motor is stationary.
[0]
*
Off
No function
[1]
Enable
Complete
AMA
Performs AMA of the stator resistance R
S
,
the rotor resistance R
r
, the stator leakage
reactance X
1
, the rotor leakage reactance X
2
and the main reactance X
h
.
[2]
Enable
Reduced
AMA
Performs a reduced AMA of the stator
resistance R
s
in the system only. Select this
option if an LC filter is used between the
frequency converter and the motor.
NOTE
1-29 Automatic Motor Adaptation (AMA)
will not have effect
when
= [1] PM, non salient SPM.
Activate the AMA function by pressing [Hand on] after
selecting [1] or [2]. See also the item
Automatic Motor
Adaptation
in the Design Guide. After a normal sequence,
the display will read: “Press [OK] to finish AMA”. After
pressing the [OK] key the frequency converter is ready for
operation.
Parameter Description
VLT
®
Refrigeration Drive Programming Guide
38
MG16H102 - VLT
®
is a registered Danfoss trademark
3
3