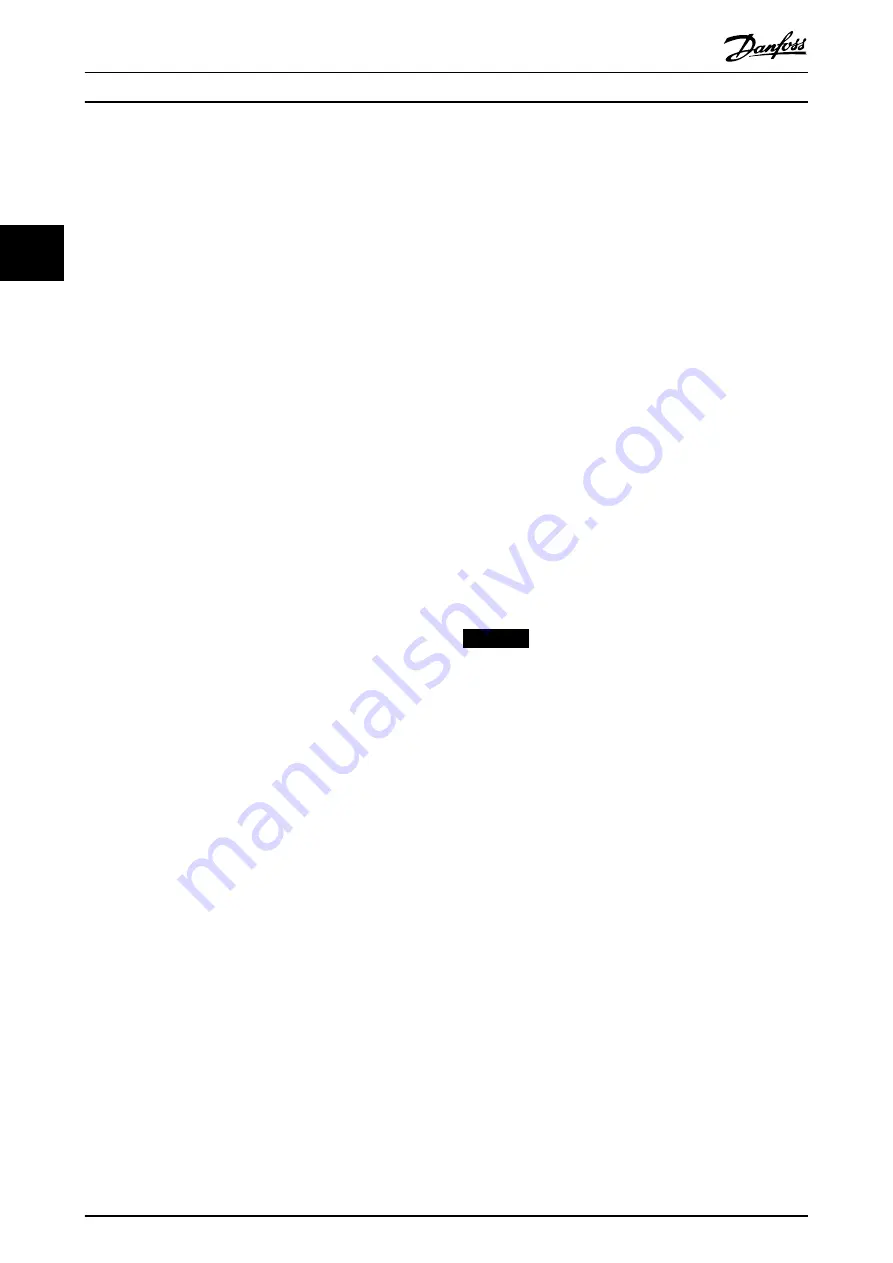
Static overload in VVC
+
mode
When the frequency converter is overloaded, the control
reduces the output frequency to reduce the load.
If the overload is excessive, a current can occur that makes
the frequency converter cut out after approximately 5–
10 s.
3.6 Ambient Conditions
3.6.1 Humidity
Although the frequency converter can operate properly at
high humidity (up to 95% relative humidity), condensation
must always be avoided. There is a specific risk of conden-
sation when the frequency converter is colder than moist
ambient air. Moisture in the air can also condense on the
electronic components and cause short circuits. Conden-
sation occurs to units without power. Install a cabinet
heater when condensation is possible due to ambient
conditions. Avoid installation in areas subject to frost.
Alternatively, operating the frequency converter in stand-
by mode (with the unit connected to the mains) reduces
the risk of condensation. However, ensure that the power
dissipation is sufficient to keep the frequency converter
circuitry free of moisture.
The frequency converter complies with the following
standards:
•
IEC/EN 60068-2-3, EN 50178 9.4.2.2 at 50
°
C.
•
IEC 600721 class 3K4.
3.6.2 Temperature
Minimum and maximum ambient temperature limits are
specified for all frequency converters. Avoiding extreme
ambient temperatures prolongs the life of the equipment
and maximises overall system reliability. Follow the
recommendations listed for maximum performance and
equipment longevity.
•
Although frequency converters can operate at
temperatures down to -10
°
C, proper operation at
rated load is only guaranteed at 0
°
C or higher.
•
Do not exceed the maximum temperature limit.
•
The lifetime of electronic components decreases
by 50% for every 10
°
C when operated above its
design temperature.
•
Even devices with IP54, IP55, or IP66 protection
ratings must adhere to the specified ambient
temperature ranges.
•
Extra air conditioning of the cabinet or instal-
lation site may be required.
3.6.3 Cooling
Frequency converters dissipate power in the form of heat.
Adhere to the following recommendations for effective
cooling of the units.
•
Maximum air temperature to enter the enclosure
must never exceed 40
°
C (104
°
F).
•
Day/night average temperature must not exceed
35
°
C (95
°
F).
•
Mount the unit to allow for unhindered cooling
airflow through the cooling fins. See
for correct mounting
clearances.
•
Provide minimum front and rear clearance
requirements for cooling airflow. See the
VLT
®
DriveMotor FCP 106 and FCM 106 Operating
Instructions
for proper installation requirements.
3.6.4 Aggressive Environments
A frequency converter contains many mechanical and
electronic components. All are to some extent vulnerable
to environmental effects.
NOTICE
Do not install the frequency converter in environments
with airborne liquids, particles, or gases capable of
affecting and damaging the electronic components.
Failure to take the necessary protective measures
increases the risk of stoppages, thus reducing the life of
the frequency converter.
Liquids can be carried through the air and condense in the
frequency converter and may cause corrosion of
components and metal parts. Steam, oil, and salt water
may cause corrosion of components and metal parts. In
such environments, use equipment with enclosure
protection rating IP54.
Airborne particles such as dust may cause mechanical,
electrical, or thermal failure in the frequency converter. A
typical indicator of excessive levels of airborne particles is
dust particles around the frequency converter fan. In dusty
environments, use equipment with enclosure protection
rating IP54 or a cabinet for IP20/Type 1 equipment.
In environments with high temperatures and humidity,
corrosive gases, such as sulphur, nitrogen, and chlorine
compounds, cause chemical processes on the frequency
converter components.
Such chemical reactions rapidly affect and damage the
electronic components. In such environments, mount the
System Integration
VLT
®
DriveMotor FCP 106/FCM 106
42
Danfoss A/S © 06/2016 All rights reserved.
MG03M202
3
3
Содержание VLT DriveMotor FCP 106
Страница 1: ...ENGINEERING TOMORROW Design Guide VLT DriveMotor FCP 106 FCM 106 vlt drives danfoss com...
Страница 2: ......