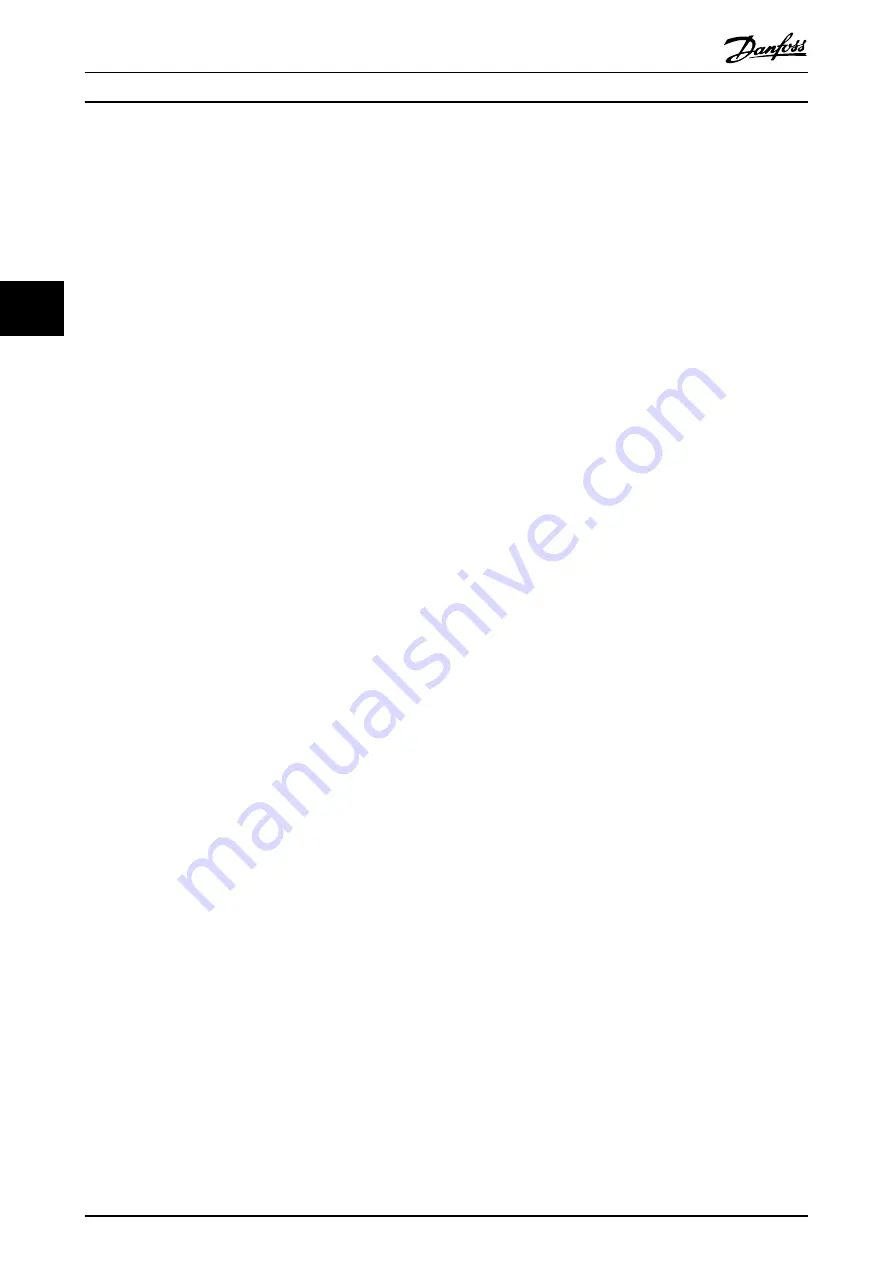
4 Positioning Control
4.1 Introduction
FC 360 supports positioning control. To use the function,
set
parameter 37-00 Application Mode
to
[2] Position control
.
When positioning control is enabled, the frequency
converter runs in VVC
+
control mode. It is important to
perform an AMA with correct motor data prior to
positioning control.
Position feedback signals are sent to FC 360 via MCB102 or
MCB103. 24 V encoder to terminals 32/33 is not supported
in position control mode.
Positioning control in FC 360 provides the following
features:
•
Supports both relative and absolute positioning.
•
Can be controlled via digital outs or PROFIBUS.
•
Supports direct positioning (via PROFIBUS) and
indexed positioning (via digital inputs).
•
Up to 8 fixed positions.
•
Supports homing function (without z index).
•
Uses MCB102 or MCB103 as signal feedback
source.
•
Supports both software and hardware limit
settings.
4.2 Programming
4.2.1 Preparation
Complete the following tasks before starting the
positioning control.
•
Check the motor phase
In
Hand on
mode, set the frequency to a low
positive value. For example, +3 Hz. Make sure the
motor rotates in the positive direction. If it
rotates in the negative direction, exchange the
motor phases.
•
Remove all signals to inputs.
•
Select Off mode via the local control panel (LCP
or GLCP).
•
Initialise the frequency converter in
14-22
Operation Mode
.
•
Perform an AMA.
•
Set
37-00 Application Mode
to
[2] Position Control
.
•
Select the feedback source in
37-01 Pos. Feedback
Source
and
7-00 Speed PID Feedback Source
.
•
MCB102
Set
17-10 Signal Type
and
17-11
Resolution (PPR)
according to the specifi-
cation of the actual encoder used.
•
MCB103
Set
17-50 Poles
,
17-51 Input Voltage
,
17-52 Input Frequency
, and
17-53
Transformation Ratio
according to the
specification of the resolver.
Set
17-59 Resolver Interface
to
[1] Enabled
to enable MCB103 for capture resolver.
Monitor the value of
34-50 Actual Position
, rotate
the motor shaft manually in the positive
direction, then
34-50 Actual Position
should show
an increasing value. If the value is descending
with an incremental encoder, exchange the
feedback encoder track A+ with B+, and A- with
B-. If no value is displayed, check the wiring of
the encoder.
•
Set ramp time
Set the activated ramp-up time in
3-41 Ramp 1
Ramp Up Time
,
3-51 Ramp 2 Ramp Up Time
,
3-61
Ramp 3 Ramp up Time
, and
3-71 Ramp 4 Ramp up
Time
to be 75% of the minimum value in
37-05
Pos. Ramp Up Time
.
Set the activated ramp-down time in
3-42 Ramp 1
Ramp Down Time
,
3-52 Ramp 2 Ramp Down Time
,
3-62 Ramp 3 Ramp down Time
and
3-72 Ramp 4
Ramp Down Time
to be 75% of the minimum
value in
37-06 Pos. Ramp Down Time
.
•
Select Auto On mode via LCP or GLCP.
•
Ensure that there are no alarms.
4.2.2 Basic Settings
Selecting the positioning control source
Select
[0] DI
or
[1] Fieldbus
in
37-14 Pos. Ctrl. Source
.
Limit settings
Block 1 direction, or set position or velocity limits to
achieve better safety.
•
Direction block
If necessary, block forward or reverse direction in
37-15 Pos. Direction Block
.
•
Position limit
There are 2 types of position limits: hardware
limits and software limits. Hardware limits are set
by digital inputs. Software limits are set via
parameter settings.
Positioning Control
VLT
®
AutomationDrive FC 360
14
Danfoss A/S © 11/2014 All rights reserved.
MG06E102
4
4