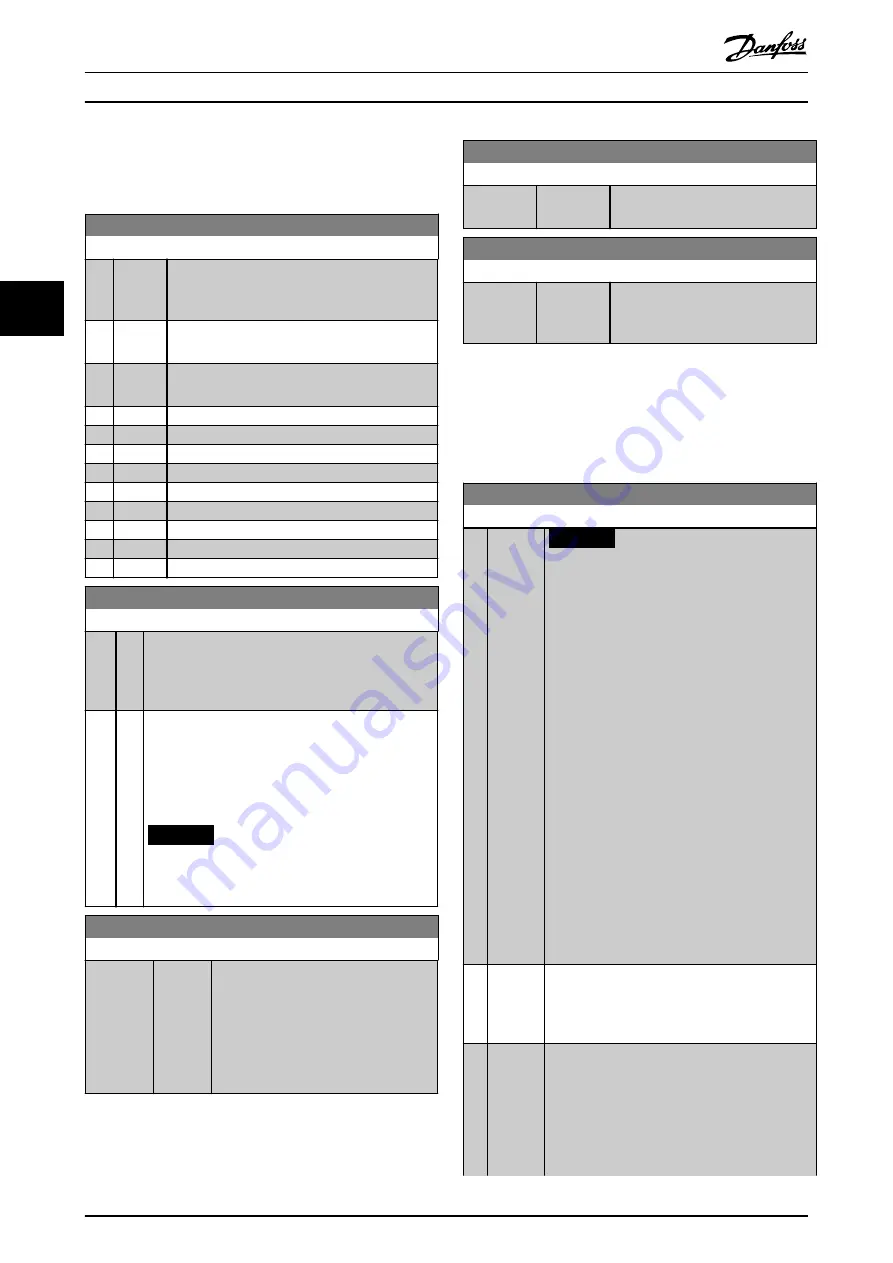
4.13 Parameters: 14-** Special Functions
4.13.1 14-0* Inverter Switching
14-01 Switching Frequency
Option:
Function:
Select the inverter switching frequency. Changing
the switching frequency helps to reduce acoustic
noise from the motor.
[0]
Ran3
3 kHz true random PWM (white noise
modulation).
[1]
Ran5
5 kHz true ramdom PWM (white noise
modulation).
[2]
2.0 kHz
[3]
3.0 kHz
[4]
4.0 kHz
[5]
5.0 kHz
[6]
6.0 kHz
[7]
8.0 kHz
[8]
10.0 kHz
[9]
12.0 kHz
[10] 16.0 kHz
14-03 Overmodulation
Option: Function:
[0]
Off To avoid torque ripple on the motor shaft, select
[0]
Off
for no overmodulation of the output voltage. This
feature may be useful for applications such as grinding
machines.
[1]
*
On Select
[1] On
to enable the overmodulation function
for the output voltage. This is the right selection when
it is required that the output voltage is > 95% of the
input voltage (typical when running over-synchro-
nously). The output voltage is increased according to
the degree of overmodulation.
NOTICE
Overmodulation leads to increased torque
ripple as harmonics are increased.
14-07 Dead Time Compensation Level
Range:
Function:
Size
related
*
[0 -
100 ]
Level of applied deadtime compensation
in percentage. A high level (>90%)
optimises the dynamic motor response; a
level from 50% to 90% is good for both
motor-torque-ripple minimisation and the
motor dynamics; a zero level turns the
deadtime compensation off.
14-08 Damping Gain Factor
Range:
Function:
Size related
*
[0 - 100 %] Damping factor for DC link voltage
compensation.
14-09 Dead Time Bias Current Level
Range:
Function:
Size related
*
[0 - 100 %] Set a bias signal (in [%]) to add to
the current-sense signal for deadtime
compensation for some motors.
4.13.2 14-1* Mains On/Off
Parameters for configuring mains failure monitoring and
handling. If a mains failure appears, the frequency
converter tries to continue in a controlled way until the
power in the DC link is exhausted.
14-10 Mains Failure
Option:
Function:
NOTICE
cannot be
changed while motor is running.
is typically used
where very short mains interruptions (voltage
dips) are present. At 100% load and a short
voltage interruption, the DC voltage on the main
capacitors drops quickly. For larger frequency
converters it only takes a few milliseconds before
the DC level is down to about 373 V DC and the
IGBTs cut off and loses control of the motor. When
mains is restored, and the IGBTs start again, the
output frequency and voltage vector do not
correspond to the speed/frequency of the motor,
and the result is normally an overvoltage or
overcurrent, mostly resulting in a trip lock.
can be programmed
to avoid this situation.
Select the function to which the frequency
converter must act when the threshold in
parameter 14-11 Mains Voltage at Mains Fault
has
been reached.
[0]
*
No
function
The frequency converter does not compensate for
a mains interruption. The voltage on the DC-link
drops quickly and the motor is lost within
milliseconds to seconds. Trip lock is the result.
[1] Ctrl.
ramp-
down
The frequency converter remains control of the
motor and does a controlled ramp-down from
parameter 14-11 Mains Voltage at Mains Fault
level.
If
is
[0] Off
or
[2] AC
brake
, the ramp follows the overvoltage ramping.
If
is
[1] Resistor
Brake
, the ramp follows the setting in
Parameter Descriptions
VLT
®
AutomationDrive FC 360
94
Danfoss A/S © 7/2015 All rights reserved.
MG06C602
4
4