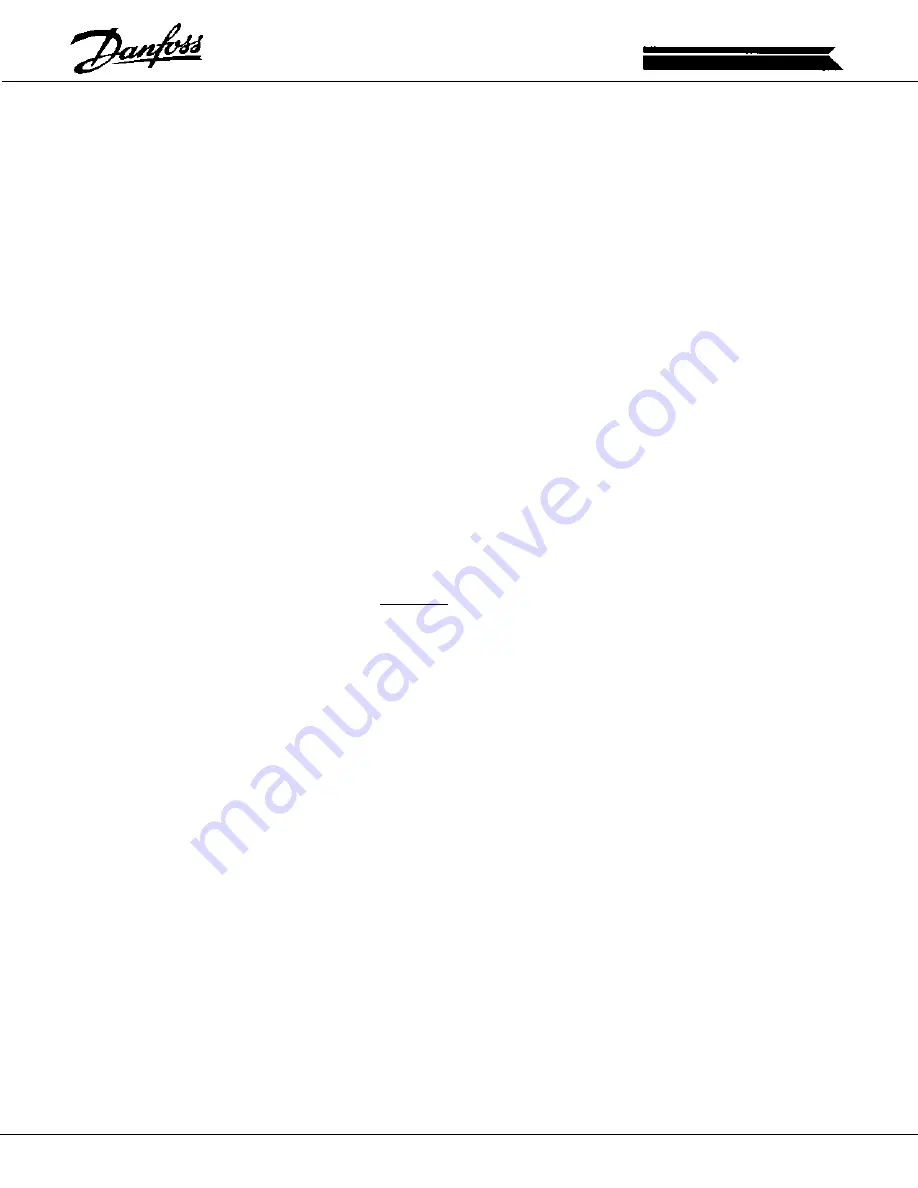
27
TESTING THE HEATSINK
TEMPERATURE SENSOR
The heatsink temperature sensor is a NTC (negative temperature
coefficient) resistor rated for 10K ohm at 25
°
C. As the temperature
rises, the resistance decreases. Conversely, as the temperature falls,
the resistance increases. The interface board monitors this resistance
and initiates a fault when the resistance is less than 787 ohms. This
corresponds to a heatsink temperature of approximately 95
°
C. By
unplugging connector MK16 on the interface board, the resistance of
the sensor may be read.
The sensors' resistance must be between 787 ohms - 105 K ohms to
be free of a fault condition.
In the case of an open reading or very high resistance, the connections
between the plug and the sensor should also be checked.
When testing phase imbalances, it is practical to measure both voltage
and current. A balanced voltage reading, but unbalanced current,
indicates the motor is drawing uneven current. This could be caused
by a fault in the motor windings or in the wiring connections between
the drive and motor. When both voltage and current are unbalanced,
it indicates a switching problem or a faulty connection within the unit
itself. This can be caused by improper gate drive signals as a result of
a faulty interface board or gate drive board. A faulty IGBT or loose
wire connection between the IGBT and the output terminals may also
be the cause.
CAUTION: Allow sufficient time for the DC Bus to fully discharge
before beginning testing. The presence of bus voltage can be
tested by setting your voltmeter for 500VDC and reading the
terminals labeled 88 (–) and 89 (+).
NOTE: When monitoring output voltage an analog voltmeter should
be used. Digital meters are sensitive to the switching frequency and
usually read erroneously.
1.
Remove the motor leads from the output terminals of the unit.
2.
Conduct the Inverter Test Procedure in Section Three on page
26.
3.
If the Inverter Test Procedure proves good, power the unit back
up. Initiate a Run command with a speed reference greater than
40Hz.
4.
Read the phase-to-phase output voltage. The actual value of the
readings is of less importance than the phase-to-phase balance.
This balance should be within 8 volts per phase.
5.
If a greater-than-8-volt imbalance exists, measure the gate drive
firing signals. See page 28.
6.
If the phase-to-phase output voltage is balanced, recheck motor
and connections for faults. Consult the factory for additional
assistance.
DYNAMIC TEST PROCEDURES
TESTING FOR OUTPUT PHASE
IMBALANCE