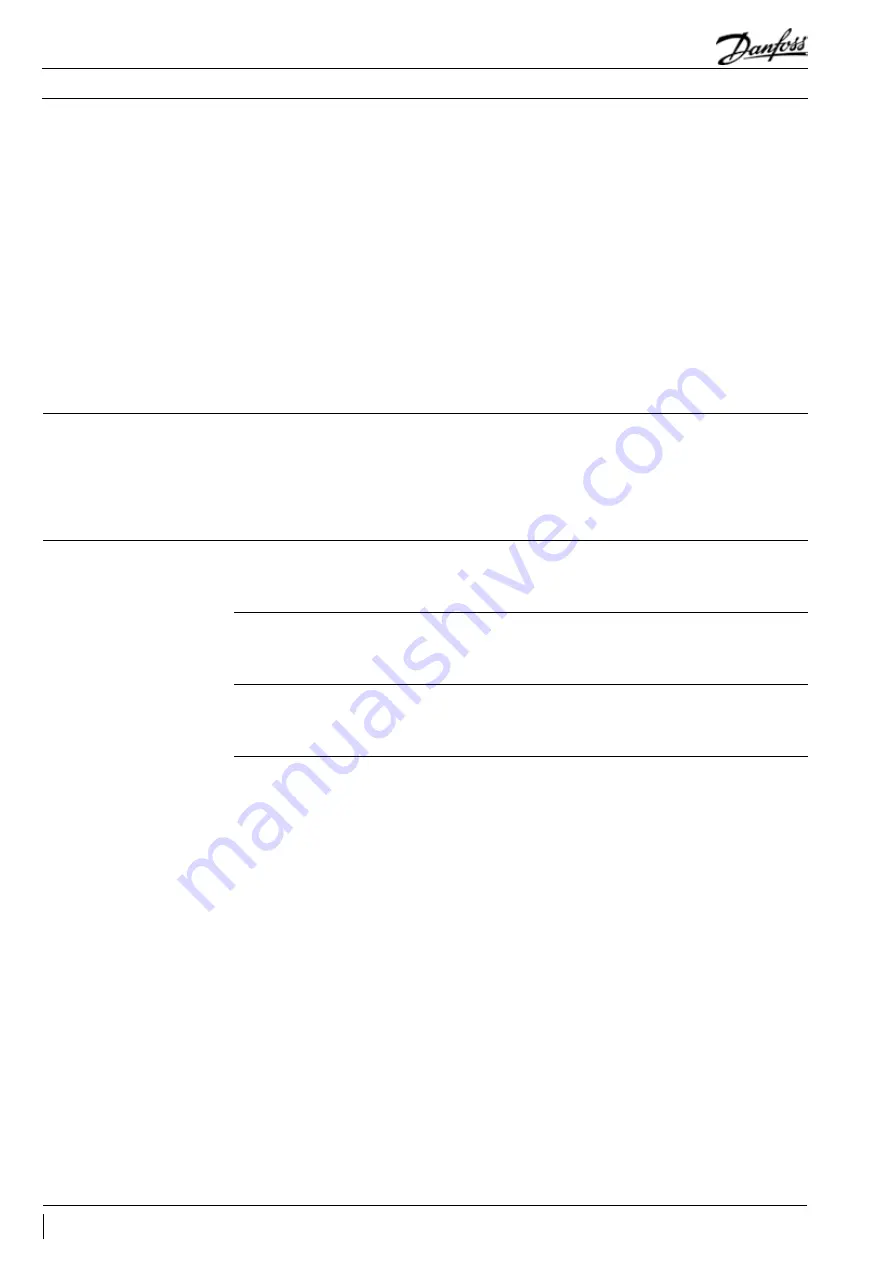
Installation
The presence of non-condensable substances
and system contaminants such as metal
shavings, solder and flux, have a negative
impact on compressor service life. Many of these
contaminants are small enough to pass through a
mesh screen and can cause considerable damage
within a bearing assembly.
The use of highly hygroscopic polyolester oil
in R410A compressors requires that the oil be
exposed to the atmosphere as little as possible.
System contamination is one of main factors
affecting equipment reliability and compressor
service life. It is important therefore to take
system cleanliness into account when assembling
a refrigeration system.
During the manufacturing process, circuit
contamination may be caused by:
• Brazing and welding oxides,
• Filings and particles from the removal of burrs in
pipe-work,
• Brazing flux,
• Moisture and air.
Consequently, when building equipment
and assemblies, the precautions listed in the
following paragraphs must be taken.
Only use clean and dehydrated refrigeration
grade copper tubing. Tube-cutting must be
carried out so as not to deform the tubing
roundness and to ensure that no foreign debris
remains within the tubing. Only refrigerant grade
fittings should be used and these must be of
both a design and size to allow for a minimum
pressure drop through the completed assembly.
Follow the brazing instructions on next pages.
Never drill holes into parts of the pipe-work
where filings and particles can not be removed.
Tubing
Do not bend the compressor discharge or suction
lines or force system piping into the compressor
connections, because this will increase
stresses that are a potential cause of failure.
Recommended brazing procedures and material,
are described section “Compressor connection”.
Brazing and soldering
When brazing copper-to-copper connections,
the use of copper/phosphorus brazing alloy
containing 5% silver or more with a melting
temperature of below 800°C is recommended. No
flux is required during brazing.
Copper to copper
Connections
When manipulating dissimilar metals such as
copper and brass or steel, the use of silver solder
and anti-oxidant flux is necessary.
Dissimilar metals
Connection
Compressor connection
When brazing the compressor fittings, do not
overheat the compressor shell, which could
severely damage certain internal components
due to excessive heating. Use of a heat shield
and/or a heat-absorbent compound is highly
recommended. Due to the relatively sizable
tubing and fitting diameters a double-tipped
torch using acetylene is recommended for
brazing operation on PSH compressors.
For soldering the injection valve connections, wet
rag and/or running water is recommend to keep
the valve body cool (not exceed 120°C) during
brazing. The inside of motor, however should
keep it dry.
For brazing the suction and discharge
connections, the following procedure is advised:
• Make sure that no electrical wiring is connected
to the compressor.
• Protect the terminal box and compressor
painted surfaces from torch heat damage (see
diagram).
• Remove the Teflon gaskets when brazing
rotolock connectors with solder sleeves.
• Use only clean refrigeration-grade copper
tubing and clean all connections.
• Use brazing material with a minimum of 5%
silver content.
• Purge nitrogen or CO2 through the compressor
in order to prevent against oxidation and
flammable conditions. The compressor should
not be exposed to the open air for extended
periods.
• Use of a double-tipped torch is recommended.
32
FRCC.PC.022.A4.02
Application Guidelines
Содержание PSH019
Страница 1: ...Danfoss scroll compressors PSH019 to PSH039 50 60 Hz R410A Application guidelines http cc danfoss com...
Страница 2: ......
Страница 42: ......
Страница 43: ......