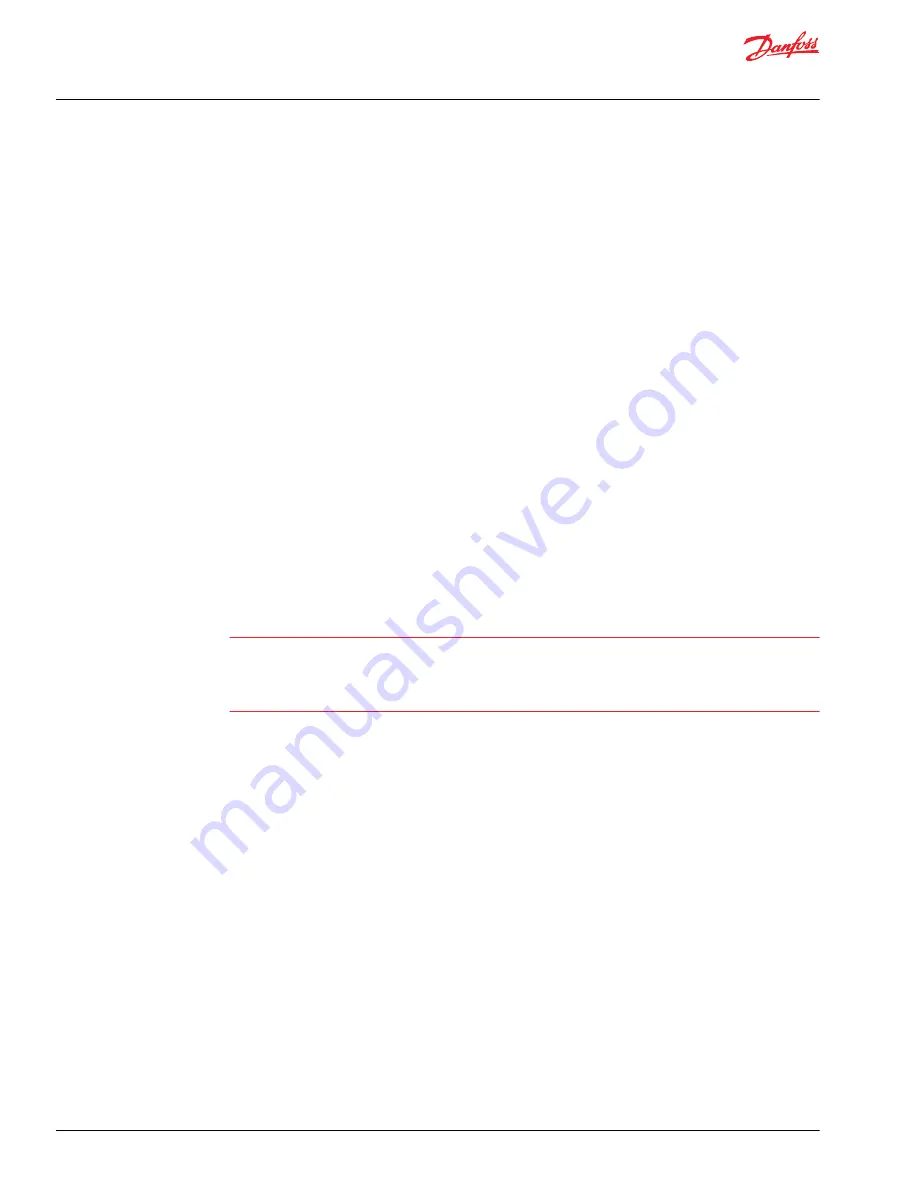
•
Protect wires from mechanical abuse, run wires in flexible metal or plastic conduits.
•
Use 85˚ C (185˚ F) wire with abrasion resistant insulation and 105˚ C (221˚ F) wire should be
considered near hot surfaces.
•
Use a wire size that is appropriate for the module connector.
•
Separate high current wires such as solenoids, lights, alternators or fuel pumps from sensor and other
noise-sensitive input wires.
•
Run wires along the inside of, or close to, metal machine surfaces where possible, this simulates a
shield which will minimize the effects of EMI/RFI radiation.
•
Do not run wires near sharp metal corners, consider running wires through a grommet when
rounding a corner.
•
Do not run wires near hot machine members.
•
Provide strain relief for all wires.
•
Avoid running wires near moving or vibrating components.
•
Avoid long, unsupported wire spans.
•
Ground electronic modules to a dedicated conductor of sufficient size that is connected to the
battery (-).
•
Power the sensors and valve drive circuits by their dedicated wired power sources and ground
returns.
•
Twist sensor lines about one turn every 10 cm (4 in).
•
Use wire harness anchors that will allow wires to float with respect to the machine rather than rigid
anchors.
Machine welding guidelines
W
Warning
High voltage from power and signal cables may cause fire or electrical shock, and cause an explosion if
flammable gasses or chemicals are present.
Disconnect all power and signal cables connected to the electronic component before performing any
electrical welding on a machine.
The following is recommended when welding on a machine equipped with electronic components:
•
Turn the engine off.
•
Remove electronic components from the machine before any arc welding.
•
Disconnect the negative battery cable from the battery.
•
Do not use electrical components to ground the welder.
•
Clamp the ground cable for the welder to the component that will be welded as close as possible to
the weld.
PLUS+1
®
USB/CAN Gateway
Communication (software uploads and downloads and service and diagnostic tool interaction) between
PLUS+1
®
modules and a personal computer (PC) is accomplished using the vehicle's PLUS+1
®
CAN
network.
The PLUS+1
®
CG150-2 USB/CAN gateway provides the communication interface between a PC USB port
and the vehicle CAN bus. When connected to a PC, the gateway acts as a USB slave. In this configuration,
all required electrical power is supplied by the upstream PC host. No other power source is required.
Refer to the
PLUS+1
®
GUIDE Software User Manual
, AQ00000026, for gateway set-up information. Refer to
the
CG150-2 USB/CAN Gateway Data Sheet
, AI00000190, for electrical specifications and connector pin
details.
Technical Information
PLUS+1® MC0XX-1XX Controller Family
Product installation and start-up
26 |
©
Danfoss | April 2018
L1321895 | BC00000227en-US0401
Содержание PLUS+1 MC012-110
Страница 1: ...Technical Information PLUS 1 MC0XX 1XX Controllers Family www danfoss com ...
Страница 27: ...Technical Information PLUS 1 MC0XX 1XX Controller Family Danfoss April 2018 L1321895 BC00000227en US0401 27 ...
Страница 28: ...Technical Information PLUS 1 MC0XX 1XX Controller Family 28 Danfoss April 2018 L1321895 BC00000227en US0401 ...
Страница 29: ...Technical Information PLUS 1 MC0XX 1XX Controller Family Danfoss April 2018 L1321895 BC00000227en US0401 29 ...