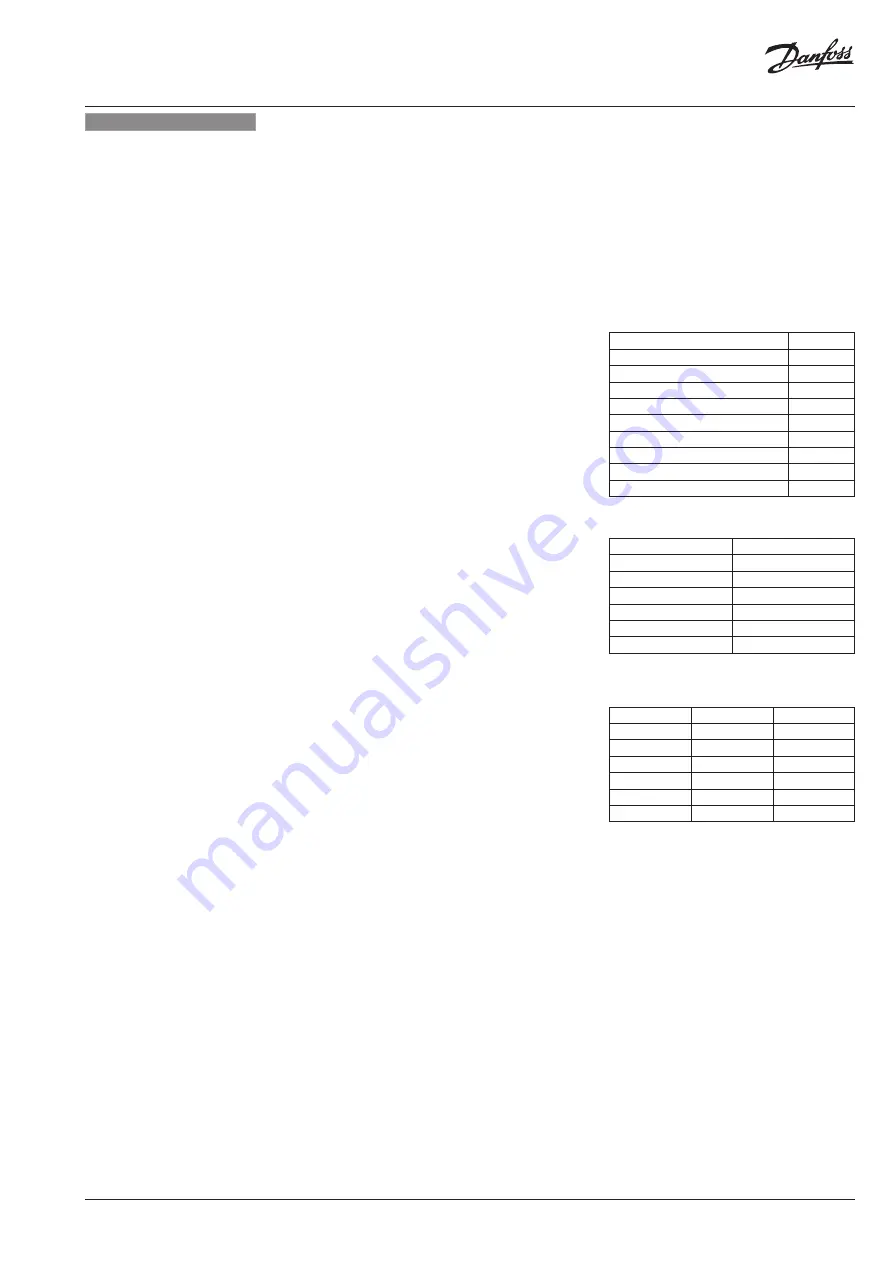
© Danfoss | 2016.03 | 9
VI.AA.A4.57
OBC 80 series
Application
The oil burner controls in the OBC 80 series are used to
control and monitor one or two-stage oil burners with
or without a preheater. The OBC 84.10 is used for burn-
ers with oil firing rates of 30 kg/h or above, and for hot
air devices. Other OBC controls are used for oil burners
with oil firing rates below 30 kg/h.
Mounting
Push the control’s contact plugs into the base with 12
connection terminals. The control and base are held to-
gether by a spring system and can be released by press-
ing a screwdriver into the slot; see fig. 1. A front plate
with knockouts or a front plate designed for PG 11
screwed connections can be used; see fig. 2.
See fig. 3 for electrical connections in the base for the
various types.
• If using an LD or LDS photo unit, the blue wire must
be connected to terminal 11 and the black wire to ter-
minal 12. If using a UV sensor, the blue wire must be
connected to terminal 11, the black wire to terminal
12, and the brown wire to terminal 1.
• If preheater is not used, short-circuit terminals 3 and 8.
• If the control is equipped with a remote reset switch
connected to terminal 9, this switch must only be acti-
vated manually.
• On some OBC 80 models, the ignition unit may be
freely connected to either terminal 6 (TT1) or terminal
7 (TT2).
Note: On the OBC 85 the boiler thermostat (TR) must always
be connected to terminal 7, and the high temperature cut-
out (TB) must always be connected to terminal 1.
Function
The OBC controls the cut-in and cut-out of the oil
burner’s components and monitors that the combustion
cycle is performed safely. See function diagrams, fig. 3.
When the boiler thermostat (TR) cuts in, heating of the
oil in the oil preheater (OFV) will begin.
Once the release temperature is reached and the oil pre-
heater’s thermostat (OTR) cuts in, the burner motor will
start the pre-purge and power will simultaneously be
applied to the ignition (TT1/TT2). Following the pre-ig-
nition and pre-purge time, the oil will be released by
valve V1 being opened. On two-stage burners V2 will
subsequently be opened.
On OBC controls without post-purge, power will be cut
off when the boiler thermostat opens after the heating
period and all relays at the outputs will open and be
ready for the next start-up cycle.
On the OBC 85 control the power is
not
cut off when
the boiler thermostat opens, as power is still needed for
the burner motor so that post-purge can occur. Instead,
a timer function ensures that the burner motor continues
to run until the end of the post-purge time. If the ther-
mostat cuts in before the end of the postpurge time, the
control will interrupt the postpurge and start a new cy-
cle with pre-heating.
Operating information
OBC 80 controls are equipped with a twocoloured LED
which displays both the operating status and can indi-
cate the causes of errors leading to lockout.
In the event of operating lockout, the cause of error can
be read out as a flash code by holding down the reset
button for at least 5 seconds and then releasing it.
Undervoltage will, however, be displayed automatically.
Reset can be performed directly in alarm mode (constant
red light) or in flash code mode by pressing the reset
button for at least 0.5 seconds but no more than 3 sec-
onds.
In flash code mode it is possible to return to alarm
mode by holding down the reset button again for at
least 5 seconds.
Normal operation
When the boiler thermostat (TR) cuts in, the reset button
flashes green. As soon as the preheater thermostat
(OTR) cuts in, the reset button lights up constant green;
see fig. 4.
When the boiler thermostat cuts out, the green light
turns off. On the OBC 85, the light does not turn off until
the post-purge period ends.
Errors during operation (flash codes; see fig. 5):
• If the mains voltage falls below 185 V before start-up,
the control will be blocked from starting. If the mains
voltage falls below 170 V during operation, the oil
supply and burner will be stopped. In both cases, the
reset button will automatically flash 8 times. When the
mains voltages reaches 185 V, the control will re-
start as normal. Please note that the control cannot be
reset if the mains voltage is below 170 V.
• If the mains voltage exceeds 264 V, the control will
automatically enter alarm mode. The purpose of the
overvoltage cut out is not simply to protect the elec-
tronics in the control, but also the other components
in the burner.
• If light is registered in the final stage of the pre-purge
time, the control will not release oil and will enter
alarm mode.
• If no flame is established at the start, i.e. by the end of
the safety time, the control will enter alarm mode.
• In the event of a flame failure during operation, the oil
supply will be cut off after no more than 1 second and
the control will restart the burner. If flame failure oc-
curs more than three times in the same operating pe-
riod (TR connected), the control will enter alarm mode.
Only one restart is allowed in the same operating period
for OBC 84.10.
• If the release temperature in the preheater is not
reached within 10 minutes, the control will enter
alarm mode.
The OBC 80 series’ processors also monitor the outputs
at TT1/TT2, V1 and V2. If errors like electrical noise (EMC)
are registered at the outputs, the control will enter
alarm mode.
Troubleshooting
The OBC 80 series is approved in accordance with the
latest EN 298:2012 norm, which sets more stringent re-
quirements for the monitoring of safety functions than
previous norms. It is therefore important to ensure
proper connection in accordance with the diagrams
shown in order to avoid alarms.
When replacing the control in connection with service,
please ensure that:
• LD/LDS photo unit is connected to terminals 11 and
12. Common 0 on terminal 2 or connected auxiliary
terminals must not be used. Replacing the photo unit
is always recommended when replacing the control.
• If a certain function is not used, e.g. remote reset on
terminal 9, the connection cannot be used as an auxil-
iary terminal. Instead, the extra auxiliary terminals in
the base must be used.
• The ignition is connected to terminal 6, though this
does not apply to controls with alternate outputs for
ignition on terminal 7 (TT2).
• If an inverter which converts 12/24 V DC to 230 V AC is
used, ensure that the inverter is capable of producing
sinusoidal AC voltage. If the voltage is not sinusoidal,
the electronics will be overloaded (burn out). There is
also a risk that the control will detect an undervoltage.
• The photo unit/UV sensor is positioned correctly in
the burner so that the correct flame signal is generated.
UV sensors are particularly sensitive, as they are very
directional to prevent the ignition spark from being
regarded as false light.
• The photo unit/UV sensor is not sooty.
• The insulation of the associated wiring is not degraded,
as this can cause leakage currents that the control will
register as errors at the inputs or outputs.
• The boiler thermostat switch contacts are not worn or
coated, as this can cause periodic supply power cuts.
• The cables to and from the control are positioned so
that they cannot generate electrical noise. Please be
particularly aware that high voltage cables from the
electronic ignition must not be placed against or wound
around the other electrical or electronic components,
such as the control itself and the pump’s solenoid
valve.
Note: Automatic controls in the OBC 80 series can only be
reset while the supply voltage is connected.
Approvals
The controls in the OBC 80 series are approved in ac-
cordance with EN 298:2012:
Technical data
Rated voltage
230 V~
Voltage range
195 - 253 V~
Frequency
50 - 60 Hz
Supply fuse
max. 10 A
Enclosure
IP 40
Ambient temperature
-20 - +60°
C
Transportation & storage temperature
-30 - +70°
C
Undervoltage protection
< 170 V
Protection class
II
Pollution degree
2
Terminal loads
Terminal
Max. operating current
3
5 A
4
1 A
5
1 A
6 / 7
1 A
8
5 A
10
1 A
Note: Total operating current max. 5 A.
Conversion / Service
BHO 60 series
BHO 70 series
OBC 80 series
-
BHO 71.10
OBC 81.10
-
BHO 71A.10
OBC 81A.10
BHO 64
BHO 72.10
OBC 82.10
BHO 64.1
BHO 72.11
OBC 82.11
BHO 64 A
BHO 73.10
OBC 82A.12
LOA 44
BHO 74.10
OBC 84.10
GB