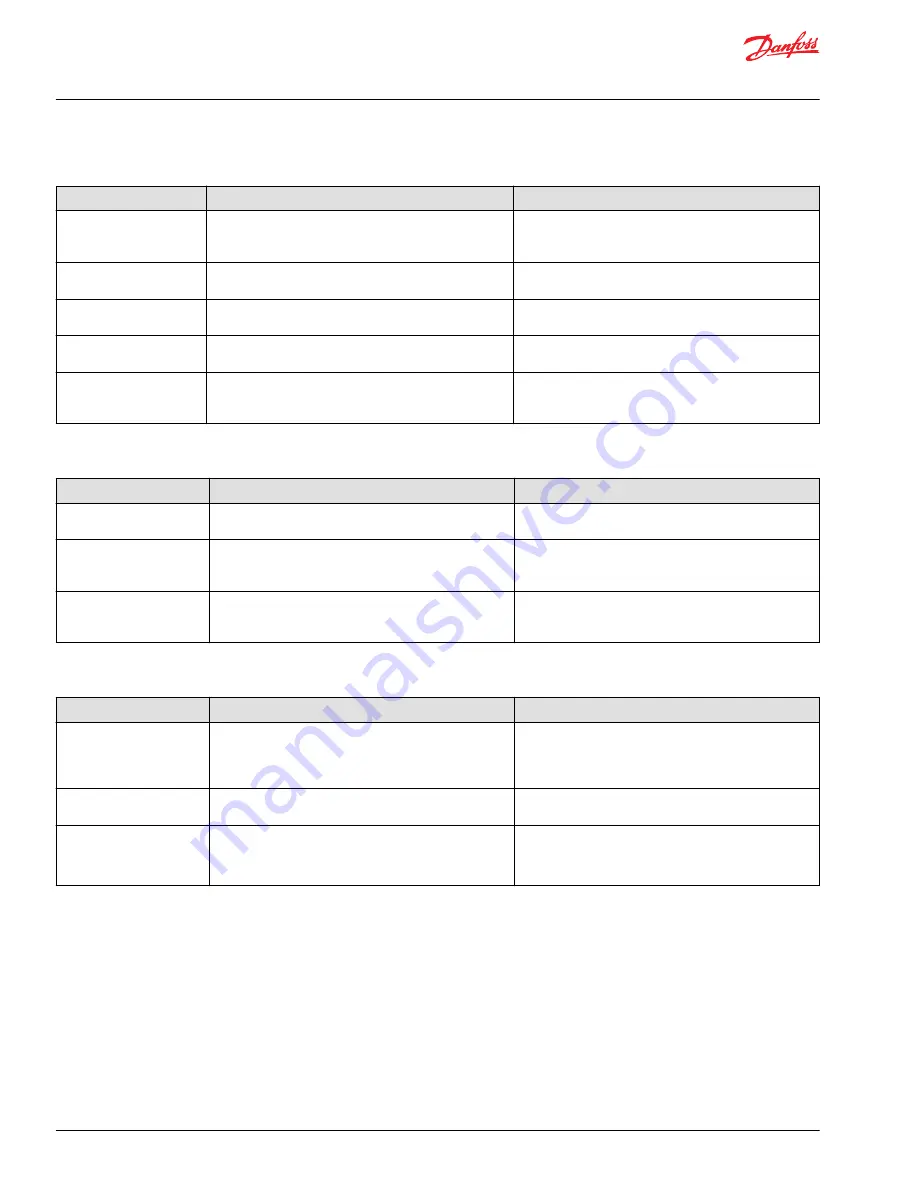
Excessive noise and/or vibration
Item
Description
Action
Check oil level in reservoir
and oil supply to the motor.
Insufficient hydraulic fluid could lead to cavitation that
would cause system noise.
Fill the reservoir to the proper level and ensure that oil
supply to the motor is adequate and the lines are
unobstructed.
Check for air in the system.
Air trapped within the system lines, or the motor itself,
could result in cavitation that would cause system noise.
Ensure that all of the system lines and components are
purged of air.
Inspect the output shaft
couplings.
A loose or incorrect shaft coupling will produce vibrations
that could result in system noise.
Ensure that the correct coupling is used and that it fits
properly onto the shaft.
Inspect the output shaft
alignment.
Misaligned shafts create excessive frictional vibration that
could result in system noise.
Ensure that the shafts are properly aligned.
Hydraulic oil viscosity above
limits.
Viscosity above acceptable limits will result in cavitation
that would lead to system noise.
Replace hydraulic oil with appropriate fluid for operating
conditions. Refer to publication 5200L0463 for information
on fluid selection.
System operating hot
Item
Description
Action
Check oil level in reservoir
and oil supply to the pump.
Insufficient amount of hydraulic fluid will not meet the
cooling demands of the system.
Fill the reservoir to the proper level.
Inspect the heat exchanger,
(if so equipped).
If the heat exchanger fails, or becomes obstructed, it may
not meet the cooling demands of the system.
Ensure that heat exchanger is receiving adequate air flow
and that the heat exchanger is in good operating
condition. Repair or replace as necessary.
Check the system relief
valves.
If a system relief valve becomes unseated for an extended
period of time or fails for any other reason, the system
could become overheated.
Repair or replace any malfunctioning relief valves as
applicable and verify that the loads on the machine are not
excessive.
Motor shifting irregularities
Item
Description
Action
Check the electrical
connection and electrical
signal to the shifting valve
coil.
Electrical signal is needed to energize the valve coil. The
energized coil is shifting the motor.
Ensure that the electrical connection between controller
valve coil is alright. Check wires and connectors. Check
electric signal. Valve coil can be energized with 12V PWM-
signal or directly with 12V.
Check valve coil
The energized valve coil is moving the valve spool. That
leads to motor shifting.
Measure valve coil resistance. Value needs to be 5,3ohms
+-5%. Replace valve if resistance is differing.
Check shifting pressure.
Shifting pressure moves servo piston. Obstruction could
result in slow or no shift conditions.
Shifting pressure at full energized valve coil (1500mA)
needs to be at 20-32bar [290-464psi] or system input
pressure, whichever is lower. Replace shifting valve when
measured pressure is differing.
Service Manual
K and L Frame Variable Motors, Cartridge Mount
Troubleshooting
14 |
©
Danfoss | July 2017
520L0631 | AX00000042en-US0402