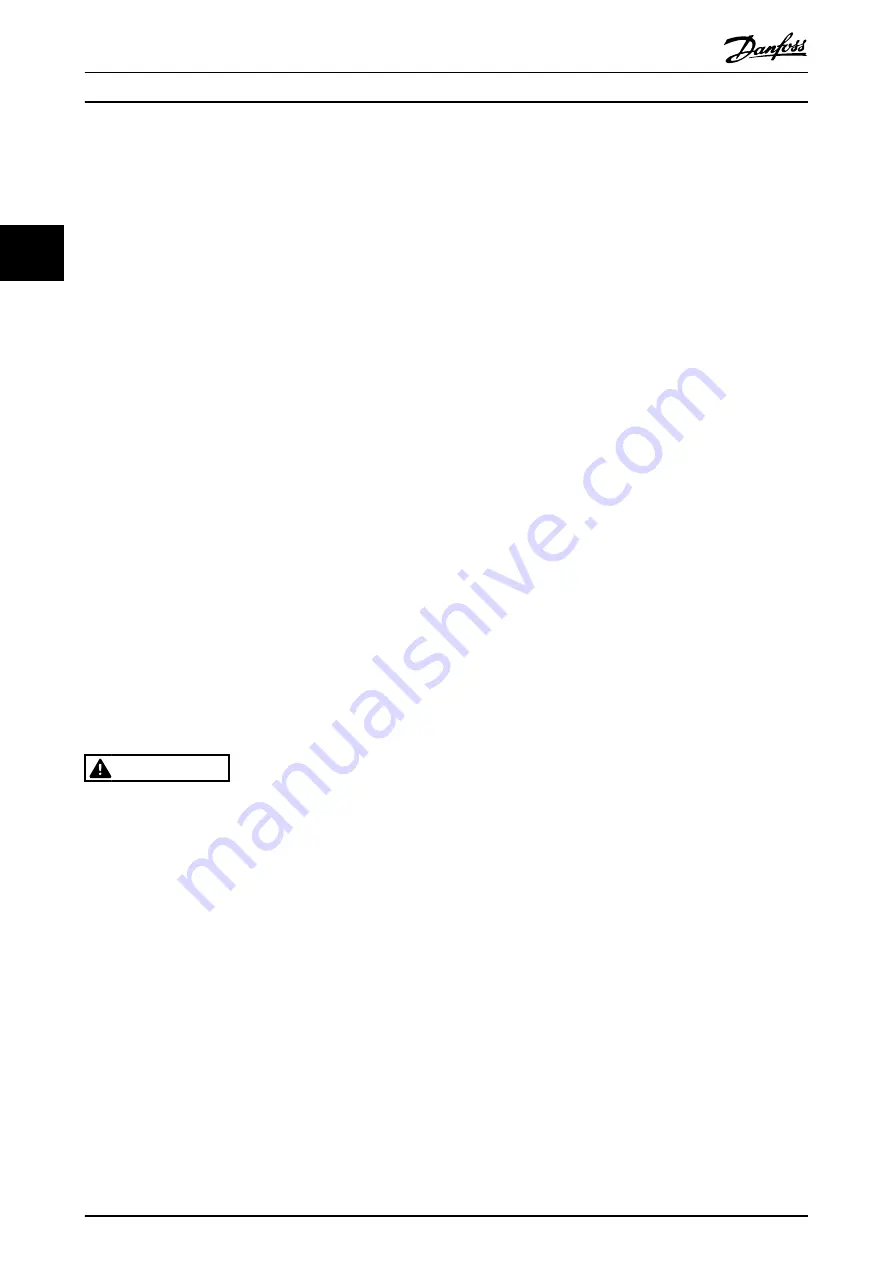
•
Operation is allowed only in compliance with the
national EMC regulations for the application
concerned.
•
See the
VLT
®
ISD 410 Design Guide
for information
regarding EMC-compliant installation of the servo
system.
•
Compliance with the limit values specified by
national regulations is the responsibility of the
producer of the plant, system or machine.
•
Compliance with the specifications, connection
conditions and installation conditions in this
instruction manual is mandatory.
•
The safety regulations and safety provisions of
the country in which the equipment is used must
be observed.
•
Care must be taken to ensure that orderly
protective earthing of the equipment, which
protects the user against the supply voltage and
protects the power supply module against
overload, is performed in accordance with local
and national regulations.
•
Overload protection for the servomotor can be
programmed using the master system. For more
information, see
Programming
in the
VLT
®
ISD 410
Design Guide
.
•
Do not remove or replace the SD card on the
encoder box during operation, otherwise the
contents of the SD card could be destroyed.
Switch the encoder box off and wait 10 seconds
before removing the SD card.
WARNING
EARTHING HAZARD
For reasons of operator safety, the components of the
servo system must be earthed correctly in accordance with
national or local electrical regulations and the information
in these operating instructions. The earth leakage current
is greater than 3.5 mA. Improper earthing of the
servomotor may result in death or serious injury.
Operational Safety
•
Safety-related applications are allowed only if
they are explicitly and unambiguously mentioned
in the
VLT
®
ISD 410 Design Guide
. Otherwise they
are not allowed.
•
All applications that can cause hazards to people
or damage to property are safety-related
applications.
•
The stop functions implemented in the software
of the master system do not interrupt the mains
voltage supply to the power supply module and
are therefore not allowed to be used as safety
switches for the servo system.
•
The motor can be brought to a stop by a
software command or a zero speed setpoint, but
DC voltage remains present on the servomotor
and/or mains voltage in the power supply
module. If personal safety considerations (e.g. risk
of personal injury caused by contact with moving
machine parts after an unintended start) make it
necessary to ensure that an unintended start
cannot occur, these stop functions are not
sufficient. In this case the servo system must be
detached from the mains network or a suitable
stop function must be implemented.
•
When the servomotor is stopped, it may start up
again on its own if the circuitry of the servomotor
is defective or after the elimination of a
temporary overload, a problem with the supply
voltage or a problem with the servomotor. If
personal safety considerations (e.g. risk of
personal injury caused by contact with moving
machine parts after an unintentional start) make
it necessary to ensure that an unintended start
cannot occur, the normal stop functions of the
servomotor are not sufficient. In this case the
servo system must be disconnected from the
mains network or a suitable stop function must
be implemented.
•
The servomotor may start running unintentionally
during parameter configuration or programming.
If this can pose a risk to personal safety (e.g. risk
of personal injury due to contact with moving
machine parts), unintended motor starting must
be prevented, for example by using the Safe Stop
function or by safe disconnection of the
servomotors.
•
Do not disconnect the cables from the
servomotor while the servo system is connected
to mains voltage. Ensure that the mains supply is
disconnected and the required waiting time has
elapsed before disconnecting or connecting the
hybrid cable or disconnecting cables from the
connection box and/or the power supply module.
Safety Instructions
VLT
®
ISD Encoder Box Operating Instructions
8
MG75F102 - VLT
®
is a registered Danfoss trademark
3
3
Содержание ISD Encoder Box
Страница 1: ...MAKING MODERN LIVING POSSIBLE Operating Instructions VLT ISD Encoder Box...
Страница 2: ......
Страница 44: ...www danfoss com drives MG75F102 175R1123 MG75F102 Rev 2012 08 13...