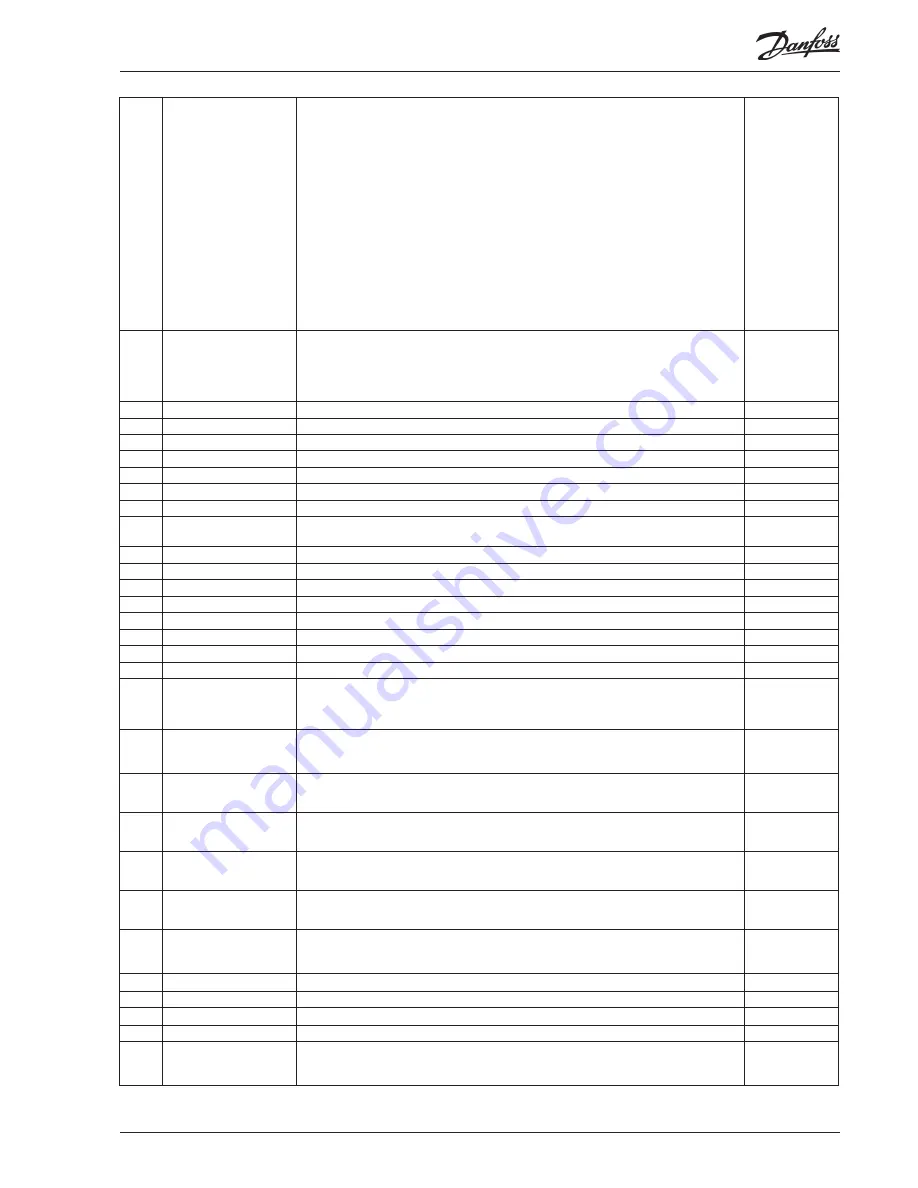
AK-PC
551
User
Guide RS8GY302 © Danfoss 2015-06
9
Control status
Read the status of the control circuit here e.g.:
• No comp. - No compressor capacity available
• Normal ctrl - Normal control
• Alarm Comp. - Cannot start compressor due to alarm condition
• ON timer - Cannot stop compressor due to ON timer restriction
• Start timer - Cannot start compressor due to Start timer restriction
• Normal ctrl - Normal control - no compressor staging
• Inj. On Delay - Waiting for injection on delay to expire
• Cascade
• 1st comp del - First compressor run timer
• Pump down - Last compressor running to pump down limit
• Sensor error - Emergency control due to sensor error
• Load shed - Load shedding function active
• Sd High - Capacity control in High Sd safety prevention mode
• Pc High - Capacity control in High Pc safety prevention mode
• Manual ctrl - Capacity control in manual mode
• Main switch OFF - OFF
Actuel zone
You will be able to see how the regulation is in relation to the reference here:
P0 error: No regulation
- Zone: The desired pressure is below the reference value
NZ: The pressure is in place in relation to the reference value
+ Zone: The desired pressure is above the reference value
Control temp.
The current value of the regulation sensor can be read here
Reference
The total regulation reference can be read here
Running capacity
Here the connected capacity can be read as a % of total capacity
Requested capacity
Here the preferred connected capacity can be read as a % of total capacity
No. of running comp.
The number of compressors in operation can be read here
PoA Pressure
The measured pressure for the PoA pressure transmitter can be read here
ToA Saturated temp.
The measured PoA pressure converted to temperature can be read here
MC PoA offset
The size of a reference displacement on Po required from the system unit
(suction pressure optimisation function) can be read here
Pc Pressure
The measured pressure for pressure transmitter Pc can be read here
Tc Saturated temp.
The measured Pc pressure converted to temperature can be read here
Day / Night status
The status of the day/night function can be read here
Load shed
The status of the load shed function can be read here
Injection ON A
The status of the injection ON signal sent to the evaporator controllers can be read here
MC Load Shedding
The status of the load shed signal received from the system device can be read here
MC Night Setback
The status of the night increase signal received from the system device can be read here
Control settings
Regulation settings
Control mode
Regulation type
The regulation is normally set to “Auto”, but it can be changed to “Off” or “Manual”.
When setting to “Manual”, a forced capacity setting can subsequently be entered in %.
MAN / OFF / AUTO
Fac: AUTO
Min: 0 %
Max: 100%
Setpoint
Enter the set point for the regulation (regulation reference = set point + different offsets) here
An offset can originate from a night increase signal or from an override function on the
system device.
Min: -80°C (-1.0 bar)
Max: 30°C (50 bar)
Fac: -15°C (3.5 bar)
Neutral zone
Set the neutral zone around the reference here. Also see the illustration on page 3.
Min: 0,1 K (0.1 bar)
Max: 20 K (5.0 bar)
Fac: 6 K (0.4 bar)
Night offset
If necessary, set the value by which the reference will be raised at night.
Keep the setting at 0 if regulating with Po optimisation from a system device.
Min: -25 K (-5.0 bar)
Max: 25 K (5.0 bar)
Fac: 0 K (0.0 bar)
Max Reference
Set the highest permissible regulation reference here
Min: -50°C (-1.0 bar)
Max: 80°C (50.0 bar)
Fac: 80°C (40.0 bar)
Min Reference
Set the lowest permissible regulation reference here
Min: -80°C (-1.0 bar)
Max: 25°C (40.0 bar)
Fac: -80°C (-1.0 bar)
PI control selection
Set how quickly the PI regulation must react here: 1 = slowly, 10 = very quickly.
(For “Custom” setting 0, the special settings options will open, i.e. Kp, Tn and time settings
around the neutral zone. These options are only for trained staff.)
Min: 0 (custom)
Max: 10
Fac: 5
Gain factor Kp
The amplification factor, Kp (can only be seen and set when the previous menu is set to “0”)
Integration time Tn
Integration time Tn (see above)
+ Zone rate of change Change coefficient for + zone (see above)
- Zone rate of change Change coefficient for - zone (see above)
First step runtime
At start-up, the cooling system must have time to cool down before PI regulation takes over
the regulation role and can cut in the next compressor.
Set the time before the next compressor may be started here.
Min: 0 s
Max: 300 s
Fac: 120 s