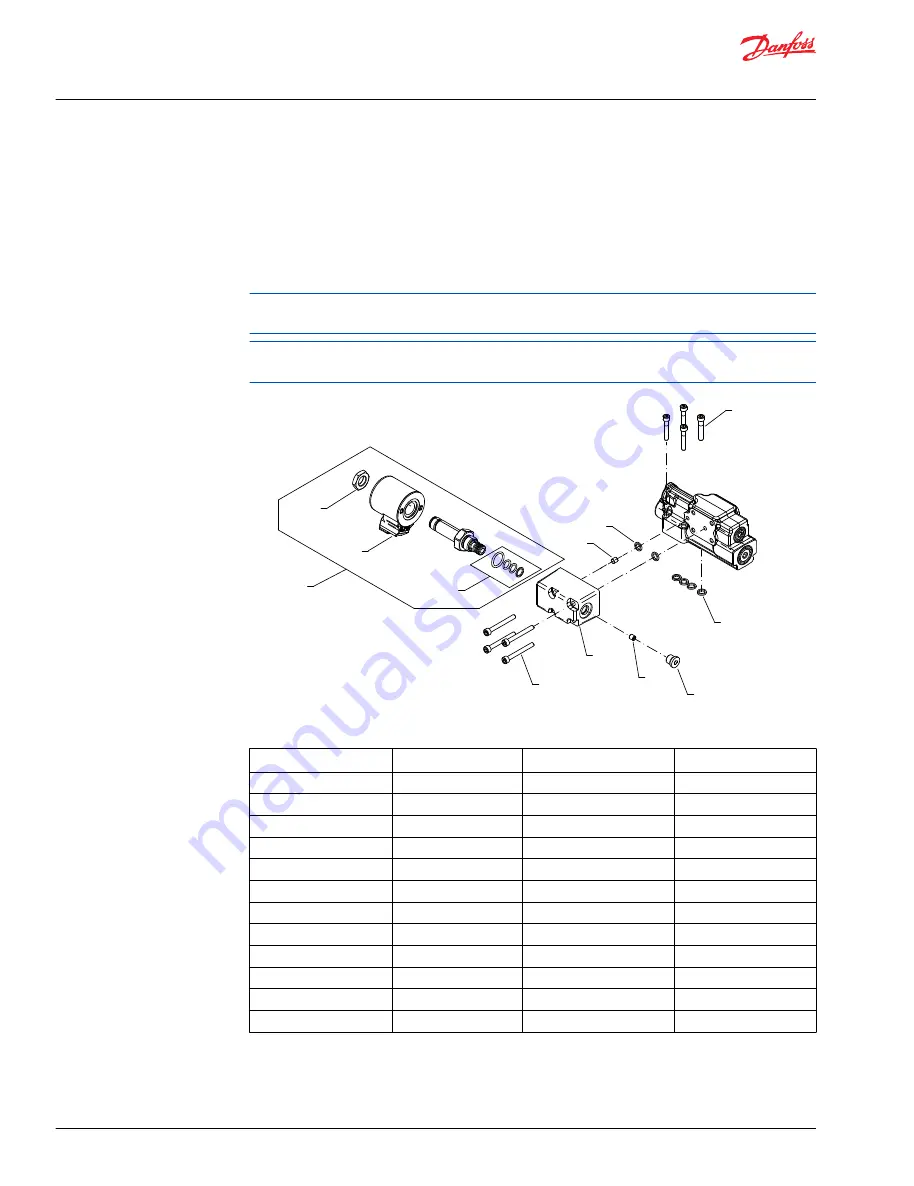
Electronic Torque Limiting Control
Repair
Disassembly, inspection and reassembly steps are the same as the steps in the previous topic (Electric
Controls). This includes repair of the spools and plugs.
The solenoid (C155), nut (QC125), and O-rings (QC120) for the valve are available as separate repair
parts. The valve is only available as a complete assembly (QC150).
If it is necessary to remove the orifice (H020), use a 3 mm internal hex wrench. Torque it to 2.7 Nm [24
in-lb] when it is installed in the manifold.
P108790
QC125
* Included in overhaul seal kit Q210
C155
QC150
QC120
C154
C149
C151
C152
H020
C153
*C200
C300
Item
Description
Wrench size
Torque
C149
Orifice
3 mm internal hex
2.7 Nm [24 in-lb]
C151
Screws
6.4 Nm [4.7 lbf-ft]
C152
Manifold
-
-
C153
Plug
5 mm internal hex
12 Nm [8.9 lbf-ft]
C154
O-ring
-
-
C155
Solenoid
-
-
C200
O-rings
-
-
C300
Screws
6.4 Nm [4.7 lbf-ft]
QC120
O-rings
QC125
Nut
8.7 Nm [6.4 lbf-ft]
QC150
Valve assembly
27.7 Nm [20.4 lbf-ft]
H020
Manifold orifice
3 mm internal hex
2.7 Nm [24 in-lb}
Service Manual
Series 45 E Frame Open Circuit Pumps
Minor repair
36 |
©
Danfoss | September 2016
AX00000024en-US0401
All manuals and user guides at all-guides.com
all-guides.com