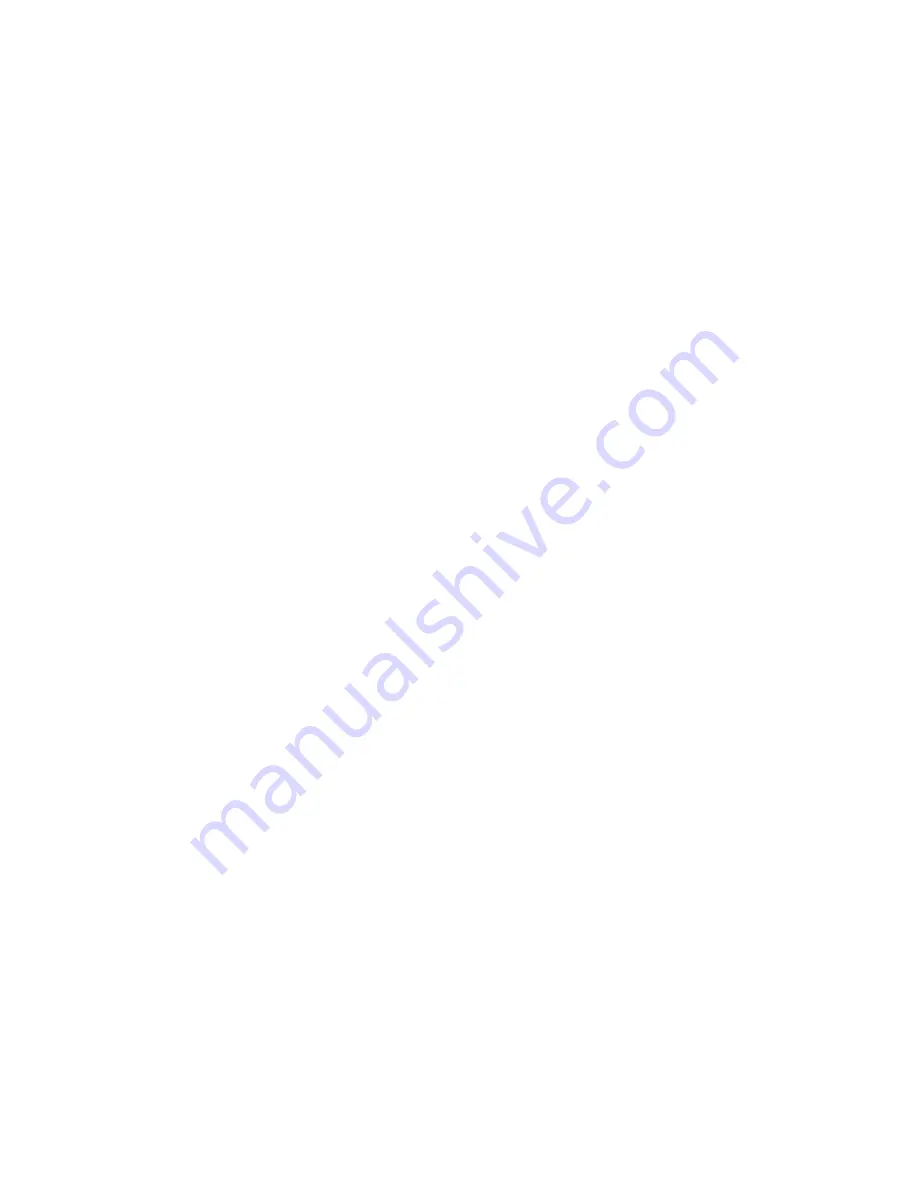
Shad-o-Scan 3001/4501 User Manual (Draft)
7
Teledyne DALSA
Regulatory Compliance
The Shad-o-Scan has been designed and manufactured in accordance with the applicable
clauses of the international standards and legislations.
•
EN 61000-6-3: Electromagnetic compatibility (EMC)
–
Generic standards.
Emission standard for residential, commercial and light-industrial environments
•
IEC/EN 61000-6-2: Electromagnetic compatibility (EMC)
–
Generic standards.
Immunity standard for industrial environments
•
EN 50581/EN IEC 63000: Technical documentations for the assessment of
electrical and electronic products with respect to the restriction of hazardous
substances
Detector Maintenance
Before performing any of the following operations, make sure that the power to the
detector is switched OFF.
Protecting the Detector Front Cover
The front cover of the detector and should be treated with care, as scratches or debris in
this area may produce artifacts in the X-ray image.
Cleaning the Detector Body and Front Cover
The detector body and front cover can be cleaned with a mild, non-abrasive cleanser such
as isopropyl alcohol. Place a small amount of cleanser on a soft cloth and rub gently over
the detector body surface. Wipe off with a clean soft cloth. Do not use any harsh cleansers
or solvents that may damage the paint or other finishes on the detector.
In the event of detector exposure to bio-hazardous materials, proper cleaning procedures
should be undertaken prior to removal or maintenance of the detector.
Calibration
To have the best image performance, the raw image data generated by the detector
should be corrected at the host by using a flat field (offset and gain) correction. As the
offset (dark) calibration signal depends (amongst others) on ambient temperature
conditions of the detector, it is commonly accepted good practice to generate these
calibration images frequently at times that the X-ray source is switched off. It is
recommended to re-calibrate the gain correction image at least once per year, or
whenever the X-ray tube is exchanged or anything changes in the X-ray imaging
geometry (e.g. the distance between the X-ray source and the detector).
The detector can contain deviating pixels. To have the best possible image quality it is
advised to perform a defect pixel correction in the host system. It is recommended to
create a defect pixel calibration map at least once every year, or more frequently in case of
heavy use.