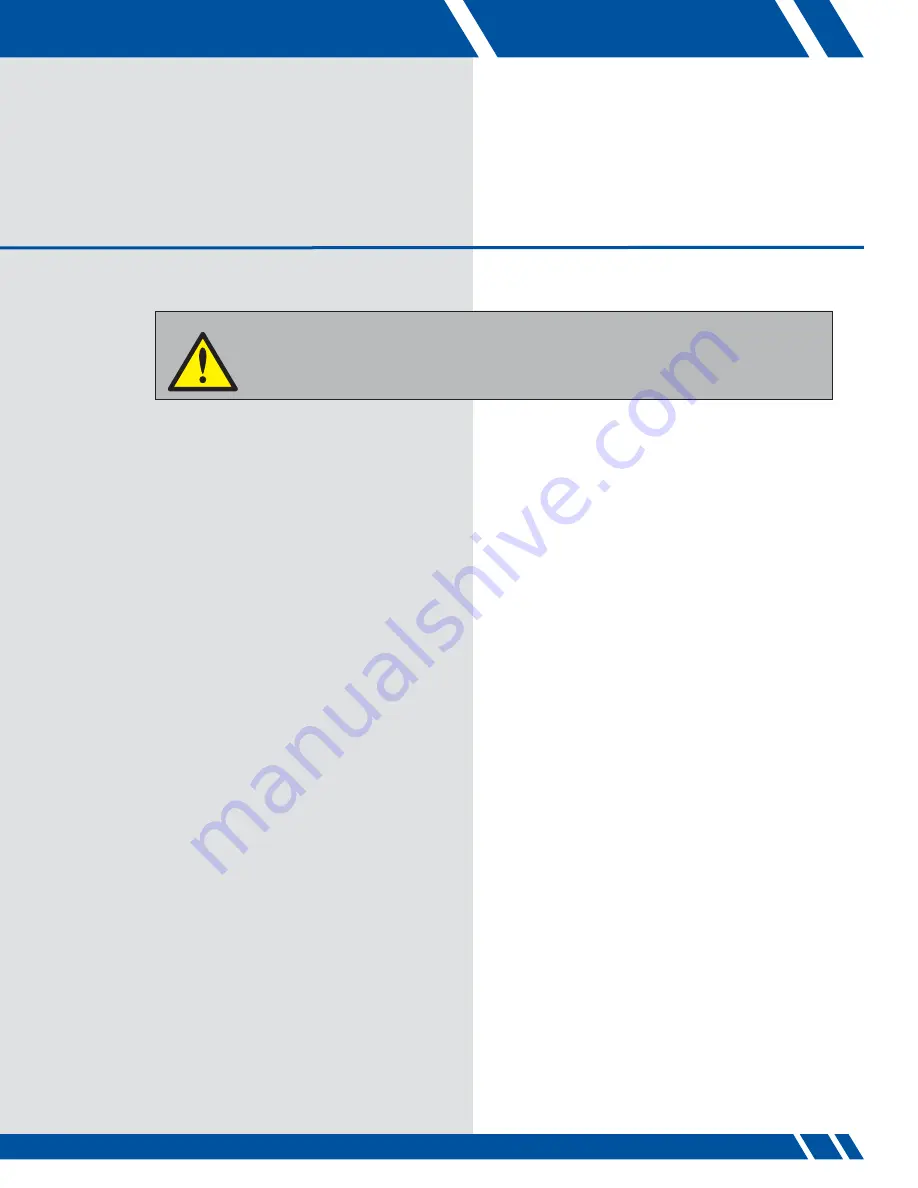
WARNING
The Vortek batten hoists are not designed to raise and lower people.
These hoists should NEVER be used for this purpose.
The Vortek
®
hoist system is an automated rigging system, meaning that the load is not counter-weighted. Each hoist
can lift loads only up to the design capacity. Overloading will result in electrical overload protection shut down of
the hoist and possible damage to rigging components.
Each hoist system consists of an integral electric motor driven gear reducer, directly coupled to a cable drum,
which winds steel cables (wire ropes) leading over sheaves installed within the hoist assembly and along the
structural steel of the building. The cables support battens for attaching the load. The battens can be lowered to
within the specified trim above the stage floor to allow attachment of loads.
The Vortek M Series control system consists of three basic parts, as described below:
Motor and Electronic Variable Frequency Drive (VFD)
The motor, Electronic Variable Frequency Drive, and dynamic braking resistor for each motor are located
within each Vortek M Series motorized hoist. A local control panel is located on each hoist for programming
and diagnostics by factory personnel. There is a reset-able circuit breaker located at each power point on the
HV wire way. The rated twist-locking plug on each unit acts as the main high voltage disconnect along with its
corresponding CB.
Hoist Assembly (Cable Drum, Load Brake, Limit Switches, and Frame)
The Daktronics M Series control and hoist assemblies are usually mounted on the rigging steel at the top of the
stage house. Depending on design circumstances the Vortek M Series controlled hoists may be mounted in a
different location. The gear motor, helically grooved cable drum, support bearing, and frame structure are all
factory assembled and tested. Maximum upper height and minimum lower height are set by limit switches which
are adjusted by factory-trained personnel during installation and commissioning of the system. A position encoder
is located at the brake end of each hoist motor, attached directly to the motor shaft. Each hoist assembly is also
equipped with a LOAD BRAKE, a unique safety feature provided exclusively by Daktronics. This unit is designed
to engage automatically when the load is being lowered to greatly reduce any possibility of a loaded batten to
descend uncontrolled.
02
GENERAL INFORMATION
GENERAL INFORMATION
3