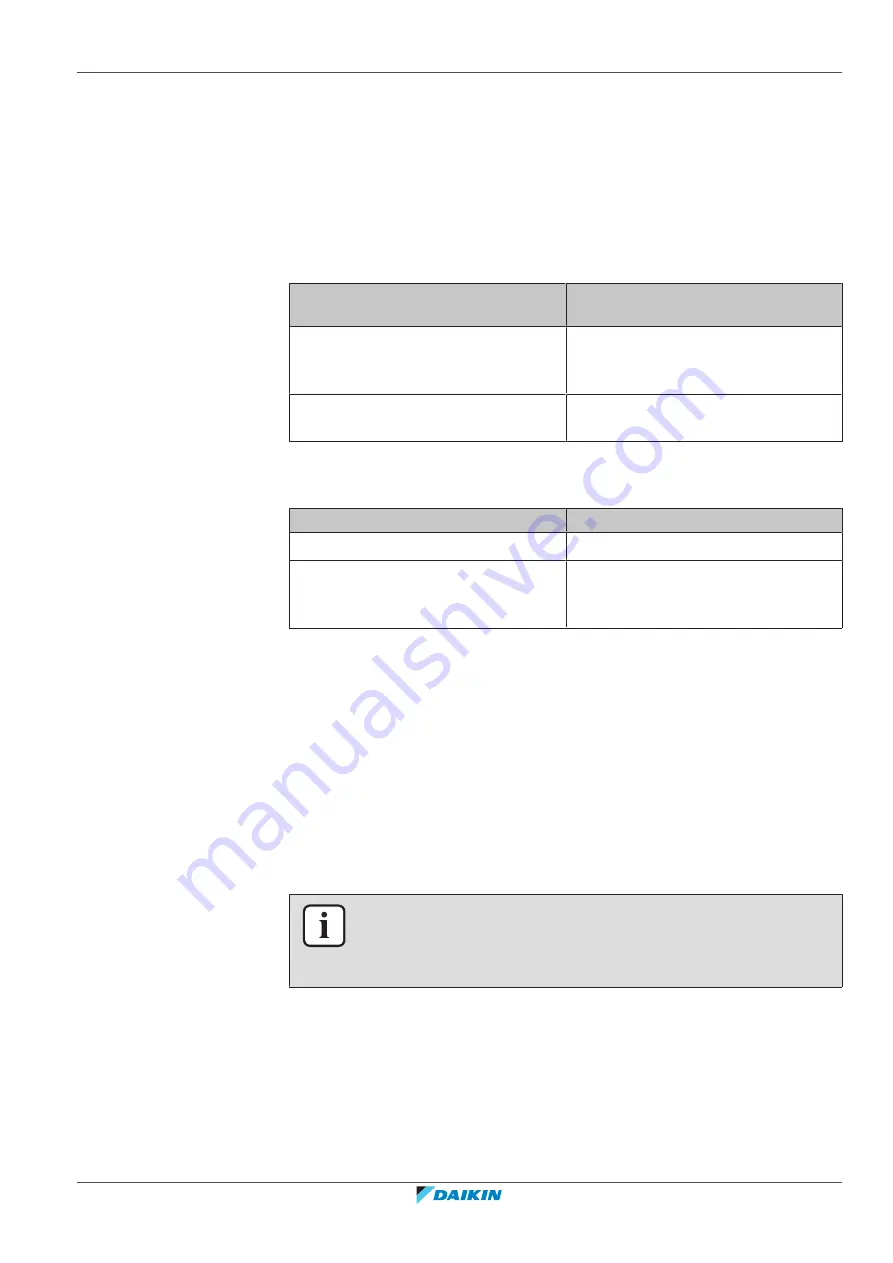
2
|
Components
Service manual
57
ATXP20~35 + FTXP20~71 + ARXP20~35 + RXP20~71
Split Comfora R32
ESIE18-01C – 2020.07
8
When the expansion valve was commanded to close, check the inlet and
outlet of the valve with a contact thermometer or use an expansion valve
stethoscope to see if refrigerant flows through the expansion valve. Check
that the valve is NOT bleeding.
Result:
There MUST be NO flow through the expansion valve.
9
When the expansion valve was commanded to open, check the inlet and
outlet of the valve with a contact thermometer or use an expansion valve
stethoscope to see if refrigerant flows through the expansion valve.
Result:
Refrigerant MUST flow through the expansion valve.
Is the flow through the expansion valve
correct?
Action
Yes
Component is OK. Return to the
troubleshooting of the specific error
and continue with the next step.
No
Replace the expansion valve, see
57].
Problem solved?
After all checking procedures listed above have been performed:
Is the problem solved?
Action
Yes
No further actions required.
No
Return to the troubleshooting of the
specific error and continue with the
next procedure.
2.3.2 Repair procedures
To remove the expansion valve motor
Prerequisite:
Stop the unit operation via the user interface.
Prerequisite:
Turn OFF the respective circuit breaker.
Prerequisite:
Remove the required plate work, see
92].
1
If needed, remove any parts or insulation to create more space for the
removal.
2
Pull up the expansion valve motor to remove it from the expansion valve
body.
INFORMATION
It may be needed to turn the expansion valve coil 1/8 turn counter clockwise to
unlock it. Make sure to note the correct orientation (position) of the expansion valve
coil before removal.
Содержание Split Comfora R32
Страница 163: ......
Страница 164: ...ESIE18 01C 2020 07 Copyright 2019 Daikin Verantwortung für Energie und Umwelt ...