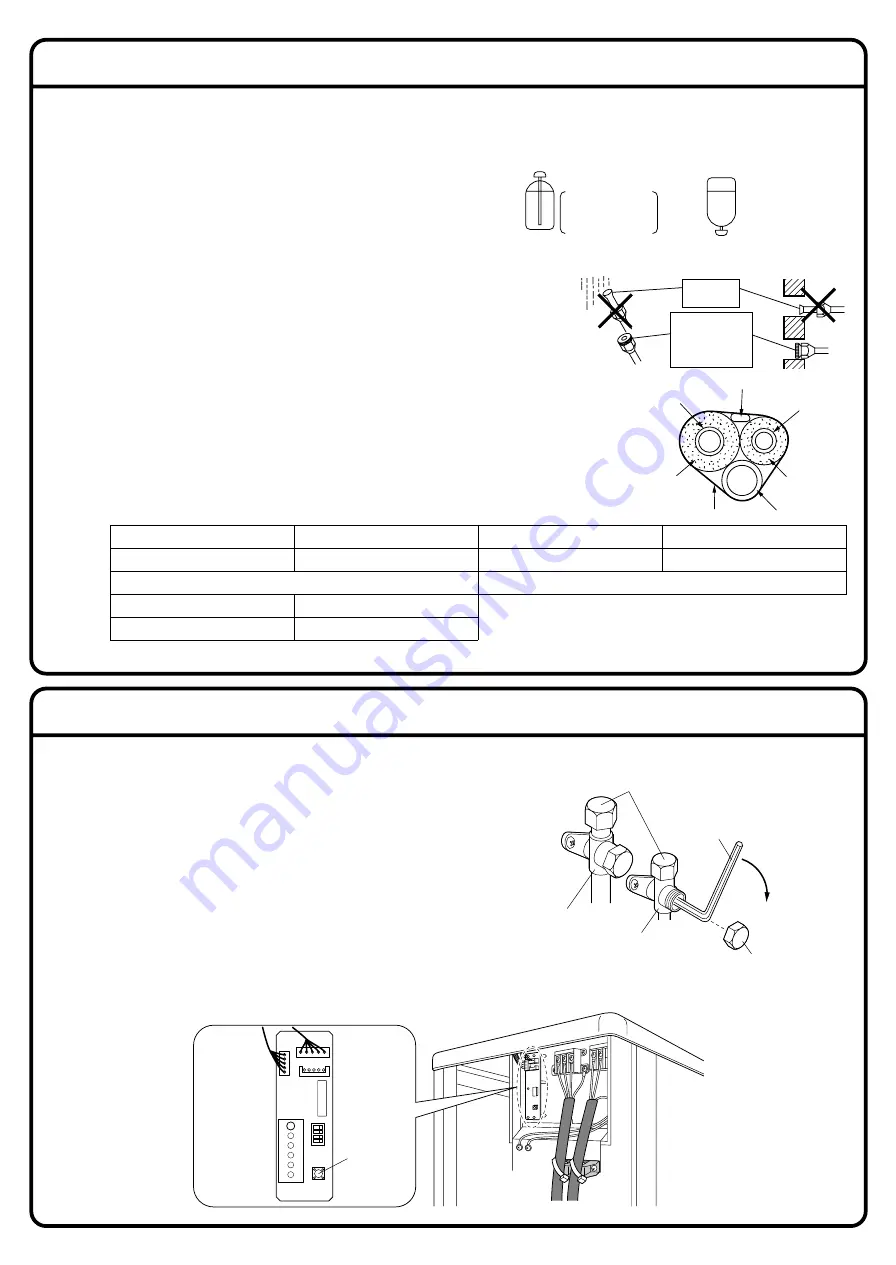
Outdoor Unit Installation (4)
Pump Down Operation
6.
Refilling the refrigerant.
Check the type of refrigerant to be used on the machine nameplate.
Precautions when adding R410A
Fill from the liquid pipe in liquid form.
It is a mixed refrigerant, so adding it in gas form may cause the
refrigerant composition to change, preventing normal operation.
1)
Before filling, check whether the cylinder has a siphon attached or not.
(It should have something like “liquid filling siphon attached” displayed on it.)
•
Be sure to use the R410A tools to ensure pressure and to prevent foreign objects entering.
7.
Refrigerant piping work.
7-1
Cautions on pipe handling.
1) Protect the open end of the pipe against dust and moisture.
2) All pipe bends should be as gentle as possible. Use a pipe bender for bending.
7-2
Selection of copper and heat insulation materials.
When using commercial copper pipes and fittings, observe the following:
1) Insulation material: Polyethylene foam
Heat transfer rate: 0.041 to 0.052W/mK (0.024 to 0.030Btu/fth˚F (0.035 to 0.045kcal/mh˚C))
Refrigerant gas pipe’s surface temperature reaches 230˚F (110˚C) max.
Choose heat insulation materials that will withstand this temperature.
2) Be sure to insulate both the gas and liquid piping and to provide insulation
dimensions as below.
In order to protect the environment, be sure to pump down when relocating or disposing of the unit.
1) Remove the valve cap from liquid stop valve and gas stop valve.
2) Carry out forced cooling operation.
3) After 5 to 10 minutes, close the liquid stop valve with a
hexagonal wrench.
4) After 2 to 3 minutes, close the gas stop valve and stop forced
cooling operation.
Forced cooling operation
1) Press the Forced Operation switch (SW1) to begin forced cooling. Press the Forced Operation switch (SW1) again
to stop forced cooling.
3)
Use separate thermal insulation pipes for gas and liquid refrigerant pipes.
Gas side
O.D. 5/8 inch (15.9mm)
1-15/16 inch (50mm) or more
Thickness 0.039 inch (1.0mm) (C1220T-O)
Liquid side
O.D. 3/8 inch (9.5mm)
1-3/16 inch (30mm) or more
Thickness 0.031 inch (0.8mm) (C1220T-O)
Gas pipe thermal insulation
I.D. 0.630-0.787 inch (16-20mm)
Thickness 0.393 inch (10mm) Min.
Liquid pipe thermal insulation
I.D. 0.472-0.591 inch (12-15mm)
Minimum bend radius
Wall
If no flare cap is
available, cover the
flare mouth with
tape to keep dirt or
water out.
Be sure to
place a cap.
Rain
Gas pipe
Liquid pipe
Gas pipe
insulation
Liquid pipe
insulation
Finishing tape
Drain hose
Inter-unit wire
LED-A
SW4
ON
AB
C
D
S102
SW1
S2
Forced
operation
switch
Close
valve cap
Hexagonal
wrench
Service port
Liquid stop valve
Gas stop valve
Filling a cylinder with an
attached siphon
Stand the cylinder upright
when filling.
There is a siphon pipe
inside, so the cylinder
need not be upside-
down to fill with liquid.
Filling other cylinders
Turn the cylinder
upside-down when filling.
Содержание RKS30
Страница 13: ...3P235796 1F M08B133E ...