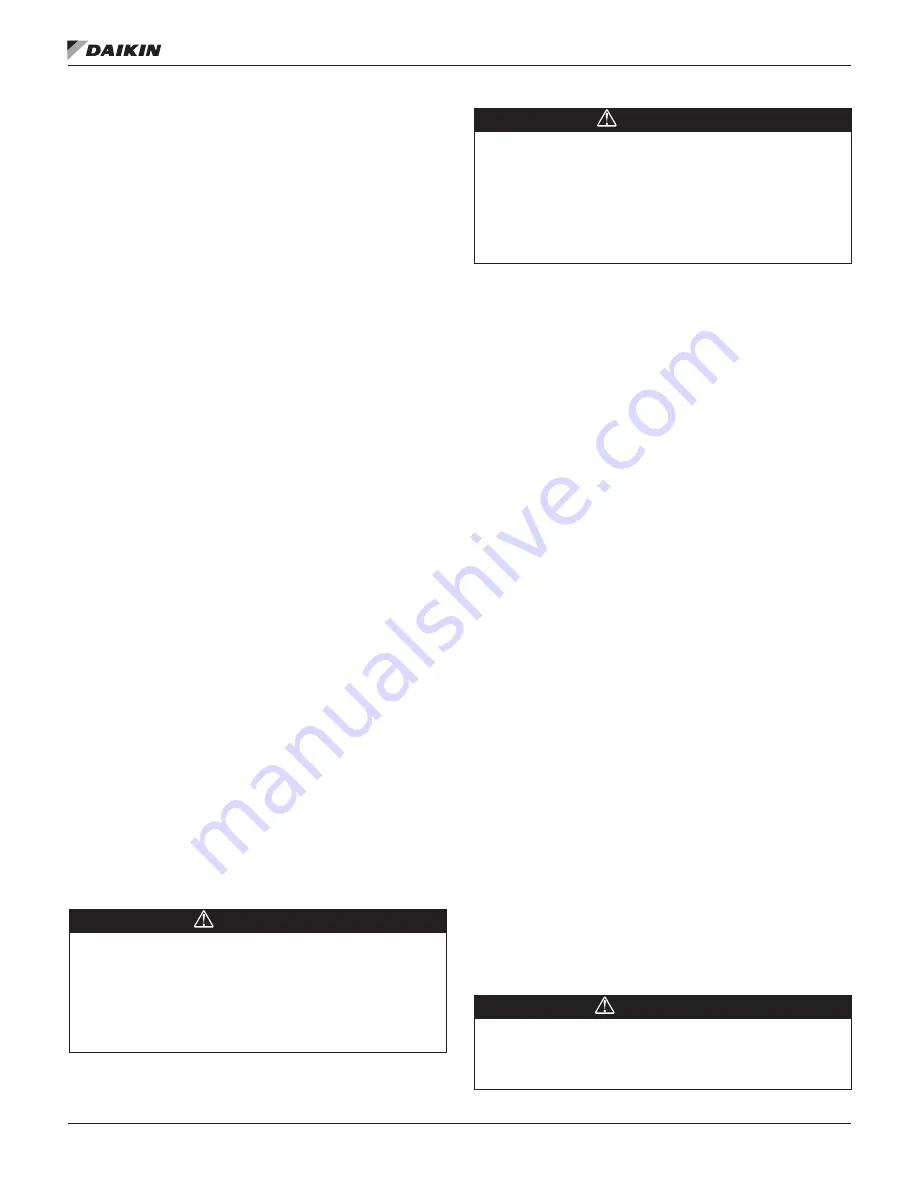
IOM 1322-1 • WATER-COOLED SCROLL COMPRESSOR 68 www.DaikinApplied.com
Unit Maintenance
System Maintenance
To provide smooth operation at peak capacity and to avoid
damage to package components, a program of periodic
inspections should be set up and followed. The following items
are intended as a guide to be used during inspection and must
be combined with sound refrigeration and electrical practices to
provide trouble-free performance.
The liquid line sight glass/moisture indicator on all circuits must
be checked to be sure that the glass is full and clear and that
the moisture indicator indicates a dry condition. If the indicator
shows that a wet condition exists or if bubbles show in the
glass, even with a full refrigerant charge, the filter-drier element
must be changed.
Water supplies in some areas can tend to foul the water-cooled
condenser to the point where cleaning is necessary. The fouled
condenser will be indicated by an abnormally high condenser
approach temperature (saturated discharge temperature
minus leaving condenser water temperature) and can result
in nuisance trip-outs. To clean the condenser, mechanical
cleaning or a chemical descaling solution should be used
according to the manufacturer’s directions. The condenser flow
sensor should be cleaned anytime the condenser is opened.
This should typically be performed at the annual inspection;
however, more frequent cleaning may be required depending
on the conditions of the jobsite.
Recommended condenser flow sensor maintenance includes
the following:
• Check the sensor tip for buildup.
• Clean the tip using a soft cloth. Stubborn buildup - such
as lime - can be removed using a common vinegar
cleaning agent.
The compressor oil level must be checked periodically to be
sure that the level is at the center of the oil sightglass located
in the compressor’s equalizing line or on the compressor itself
Low oil level can cause inadequate lubrication and if oil must
be added, use oils referred to in the following Compressor
Lubrication section.
A pressure tap has been provided on the liquid line
downstream of the filter-drier and solenoid valve but before the
expansion valve. An accurate subcooled liquid pressure and
temperature can be taken here. The pressure read here could
also provide an indication of excessive pressure drop through
the filter-drier and solenoid valve due to a clogging filter-drier.
Note: A normal pressure drop through the solenoid valve is
approximately 3 psig (20.7 kPa) at full load condition.
DANGER
LOCKOUT/TAGOUT
all power sources prior to servicing the unit.
Disconnect all power before doing any service inside the unit or serious
personal injury or death can occur. The panel is always energized to ground
even when the system switch is off. To de-energize the complete panel
including crankcase heaters, pull the main unit disconnect. Be sure to read
and understand the installation, operation, and service instructions within
this manual.
CAUTION
Warranty may be affected if wiring is not in accordance with specifications.
A blown fuse or tripped protector indicates a short ground or overload.
Before replacing fuse or restarting compressor, the trouble must be found
and corrected. It is important to have a qualified control panel electrician
service this panel. Unqualified tampering with the controls can cause
serious damage to equipment and void the warranty. If motor or compressor
damage is suspected, do not restart until qualified service personnel have
checked the unit.
All power electrical terminals should be checked for proper
torque every six months, as they tend to loosen due to normal
heating and cooling of the wire.
Compressor Lubrication
The oil level should be watched carefully upon initial start-up
and regularly thereafter.
All tandem and trio compressors on WGZ units come equipped
with oil equalization lines connecting the crankcase of each
set of compressors in each refrigerant circuit. This allows
the oil to move from one compressor crankcase to the other
during normal operation, and balance between the two when
the compressors are off. The oil sight glass is located in the
equalization line on or on the compressor body depending on
model size. In either case, the oil level should be 1/4 to 1/3 of
the glass.
POE type oil is used for compressor lubrication. This type of
oil is extremely hygroscopic, which means it will quickly absorb
moisture if exposed to air and may form acids that can be
harmful to the chiller. Avoid prolonged exposure of POE oil
to the atmosphere to prevent this problem. For more details
on acceptable oil types, contact your Daikin Applied service
representative.
The units are factory-charged with lubricant. It is important that
only the manufacturer’s recommended oils be used Acceptable
POE oil types are:
• CPI/Lubrizol Emkarate RL32-3 MAF
• Copeland Ultra 32-3 MAF
• Parker Emkarate RL32-3MAF
• Virginia LE323MAF
• Nu Calgon 4314-66
• Exxon/Mobil EAL Arctic 22 CC*
•
Hatcol 22CC*
• Everest 22CC*
NOTE:
These types of oils can only be used as “Top Off” oils.
Oil can be added to the compressor through the oil fill
hole in the crankcase. Special equipment is required
to add oil and the work should be done by qualified
refrigeration technicians with the proper training and
equipment.
WARNING
POE oil must be handled carefully using proper protective equipment
(gloves, eye protection, etc.) The oil must not come in contact with certain
polymers (e.g. PVC), as it may absorb moisture from this material. Also, do
not use oil or refrigerant additives in the system.
Unit Maintenance
Содержание IOM 1322-1
Страница 4: ......
Страница 57: ...Unit Controller Operation www DaikinApplied com 57 IOM 1322 1 WATER COOLED SCROLL COMPRESSOR...
Страница 71: ...Unit Maintenance www DaikinApplied com 71 IOM 1322 1 WATER COOLED SCROLL COMPRESSOR...
Страница 72: ...IOM 1322 1 WATER COOLED SCROLL COMPRESSOR 72 www DaikinApplied com Troubleshooting Chart Troubleshooting Chart...
Страница 74: ...IOM 1322 1 WATER COOLED SCROLL COMPRESSOR 74 www DaikinApplied com Troubleshooting Chart...
Страница 75: ...Troubleshooting Chart www DaikinApplied com 75 IOM 1322 1 WATER COOLED SCROLL COMPRESSOR...
Страница 76: ...IOM 1322 1 WATER COOLED SCROLL COMPRESSOR 76 www DaikinApplied com Troubleshooting Chart...
Страница 77: ...Troubleshooting Chart www DaikinApplied com 77 IOM 1322 1 WATER COOLED SCROLL COMPRESSOR...
Страница 78: ...IOM 1322 1 WATER COOLED SCROLL COMPRESSOR 78 www DaikinApplied com Troubleshooting Chart...