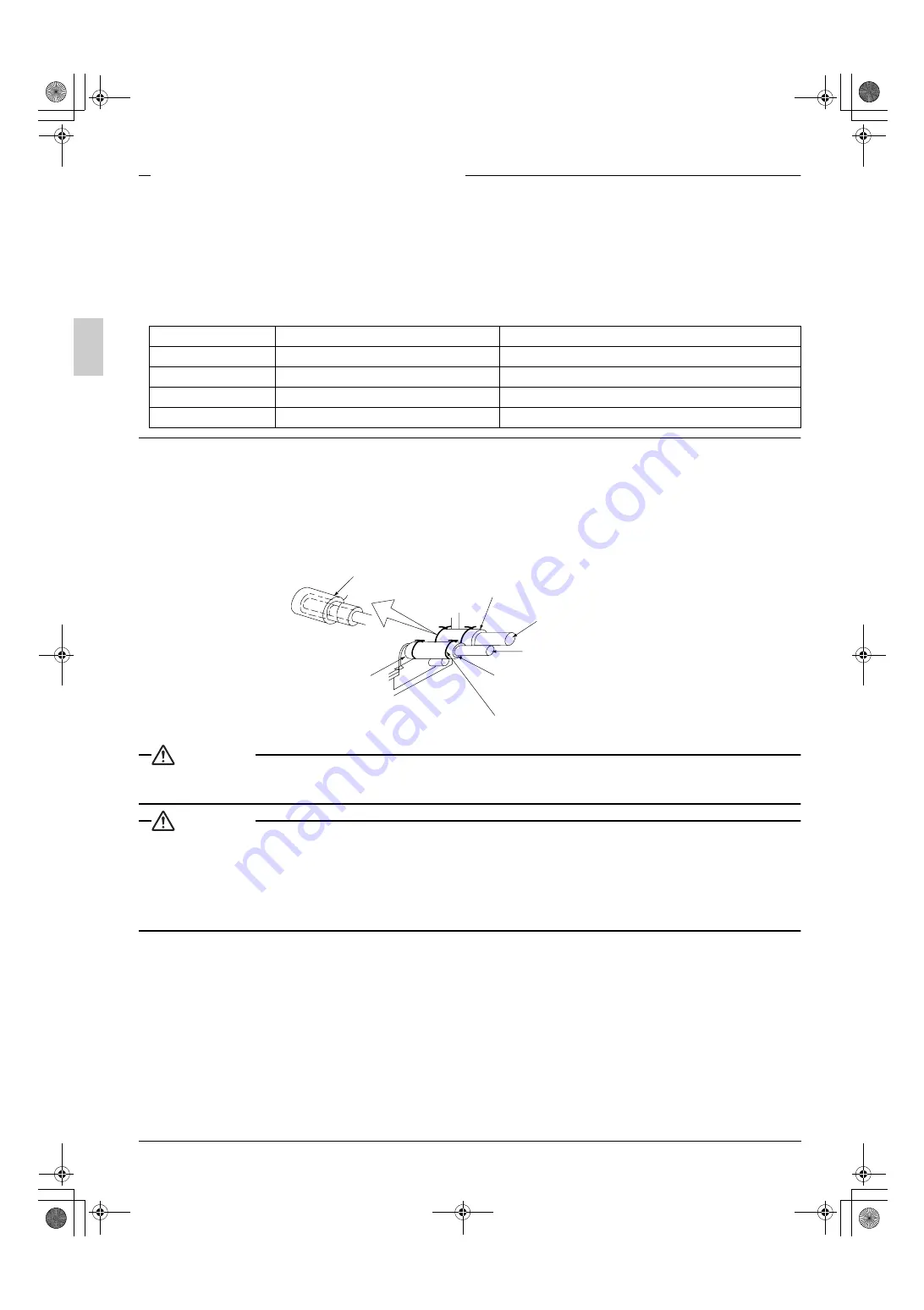
9
English
Not recommendable but in case of emergency
You must use a torque wrench but if you are obliged to install the unit without a torque wrench, you may
follow the installation method mentioned below
After the work is finished, make sure to check that there is no gas leak.
When you keep on tightening the flare nut with a spanner, there is a point where the
tightening torque suddenly increases. From that position, further tighten the flare nut the angle shown
below:
•
Make absolutely sure to execute heat insulation works on the pipe-connecting section after checking gas
leakage by thoroughly studying the following figure and using the attached heat insulating materials for
fitting (4) and (5). (Fasten both ends with the clamps (9).)
(Refer to Fig. 8)
•
Wrap the sealing pad (7) only around the insulation for the joints on the gas piping side.
(Refer to Fig. 8)
CAUTION
For local insulation, be sure to insulate local piping all the way into the pipe connections inside the machine.
Exposed piping may cause condensation or burns on contact.
CAUTION
CAUTION TO BE TAKEN WHEN BRAZING REFRIGERANT PIPING
“Do not use flux when brazing refrigerant piping. Therefore, use the phosphor copper brazing filler metal
(BCuP-2: JIS Z 3264/B-Cu93P-710/795: ISO 3677) which does not require flux.”
(Flux has extremely harmful influence on refrigerant piping systems. For instance, if the chlorine based
flux is used, it will cause pipe corrosion or, in particular, if the flux contains fluorine, it will damage the refrig-
erant oil.)
•
Before brazing local refrigerant piping, nitrogen gas shall be blown through the piping to expel air from the
piping.
If you brazing is done without nitrogen gas blowing, a large amount of oxide film develops inside the piping,
and could cause system malfunction.
•
When brazing the refrigerant piping, only begin brazing after having carried out nitrogen substitution or
while inserting nitrogen into the refrigerant piping. Once this is done, connect the indoor unit with a flared
or a flanged connection.
Pipe size
Further tightening angle
Recommended arm length of tool
φ
6.4 (1/4”)
60 to 90 degrees
Approx. 150mm
φ
9.5 (3/8”)
60 to 90 degrees
Approx. 200mm
φ
12.7 (1/2”)
30 to 60 degrees
Approx. 250mm
φ
15.9 (5/8”)
30 to 60 degrees
Approx. 300mm
(9) Clamp (attached) (×4)
Gas pipe
Liquid pipe
(5)Insulation for fitting (attached)
(for liquid line)
(4) Insulation for fitting (attached)
(for gas line)
Attach to the bottom
(For both gas piping
and liquid piping)
(7) Middle sealing pad (attached)
(Wrap from the bottom up)
Fig. 8
01_EN_3P156215-4C.fm Page 9 Saturday, May 14, 2005 9:17 AM