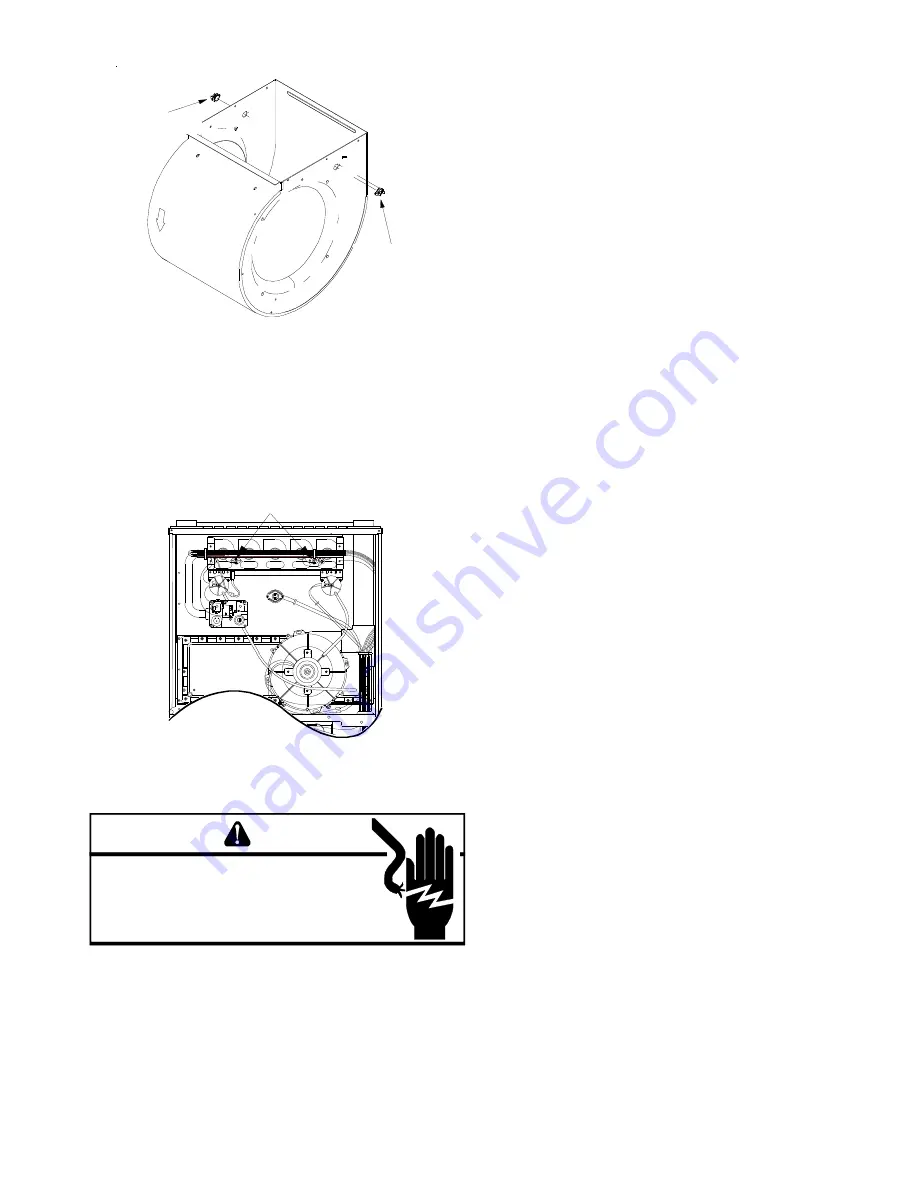
SERVICING
55
AUXILIARY LIMIT
CONTROL
AUXILIARY LIMIT
CONTROL
BLOWER HOUSING
Auxiliary Limit Control Location
S-302 CHECKING FLAME ROLLOUT CONTROL
A temperature activated manual reset control is mounted
to the manifold assembly on modulating furnace, as shown
in the following illustration.
*
*
*
*
*
*
*
2
FLAME
ROLLOUT
SWITCHES
Flame Rollout Switch Location
(90% Upflow Furnace Shown, Counterflow Similar)
WARNING
HIGH
VOLTAGE
D
ISCONNECT
ALL
POWER BEFORE SERVICING OR
CHANGING ANY ELECTRICAL WIRING.
M
ULTIPLE POWER
SOURCES MAY BE PRESENT.
F
AILURE TO DO SO MAY CAUSE
PROPERTY DAMAGE, PERSONAL INJURY OR DEATH.
1. Turn off all power sources
2. Remove the two wires from the roll out switch
3. Using an ohmmeter, check for a closed circuit across
the two roll out switch contacts (this will be the same
reading that you see by touching your two meter leads
together).
S-303 INDUCED DRAFT BLOWER MOTOR
Induced Draft Blower (IDB)
All modulating furnace models use a three phase induced
draft blower to draw flue gases through the heat exchanger.
The inducer uses ball bearings and is permanently
lubricated. This motor is driven at varying speeds by the
VFD (variable frequency drive) section of the IFC. The
IFC takes typical single phase power supplied to the furnace
and converts it to a three phase supply to operate the
draft inducer at the desired speed. The windings of the
induced draft motor will have equal resi/- 5%.
Normal resistance readings at room temperature will range
from 14-17 ohms. The voltage supplied by the IFC to drive
the induced draft blower will vary from 15-110 volts A/C
between any two windings. This would be read between
any two of the three power wires between the IFC and the
induced draft blower. This voltage to the IBD will vary
between furnace models and is dependant on what
percentage of maximum fire is being called for. The power
wires are colored red, white and black. A green colored
ground wire is also present.
S-304 MODULATING GAS VALVE
CHECK / ADJUSTMENT
Modulating furnaces use a 24 VAC pneumatically operated
gas valve by Honeywell. The valve is energized by the in-
tegrated furnace control on a call for heat, wired in series
through the front-cover pressure switch. The firing rate
percentage is determined by the negative pressure cre-
ated by the operation of the draft inducer. The gas valve
is equipped with 1/8 NPT fittings to access both the inlet
and manifold gas pressures. To do a manifold gas pres-
sure check, the furnace can be operated in field test mode.
This mode will quickly bring the furnace up to high fire. To
enter field test mode; during a call for heat, press the
fault recall button twice within a five second period; when
the dual seven segment displays show Ft, press the fault
recall button again to enter field test mode.The furnace
will stay in field test for five minutes or until the call for
heat is satisfied. Gas valve orientation must be such that
the switch is facing out towards the front of the furnace.
In the event of low manifold gas pressure, loss of flame or
low flame signal fault alerts on modulating furnaces, per-
form the following steps to determine if gas valve adjust-
ment is necessary. All other potential issues must be con-
sidered before adjusting manifold pressure such as inad-
equate gas supply pressure or condensation causing the
blocked drain switch to go open, breaking the 24 volt cir-
cuit to the gas valve. Follow this procedure to adjust the
gas valve/manifold pressure if necessary. Before adjust-
ing gas valve/manifold pressure, verify adequate gas sup-
ply pressure by measuring gas supply pressure during igni-
tion. Gas supply pressure must be within the range shown
in the Inlet Gas Supply Pressure chart. Do not attempt to
adjust manifold gas pressure if supply pressure is outside
the appropriate gas pressure range shown in the following
chart.