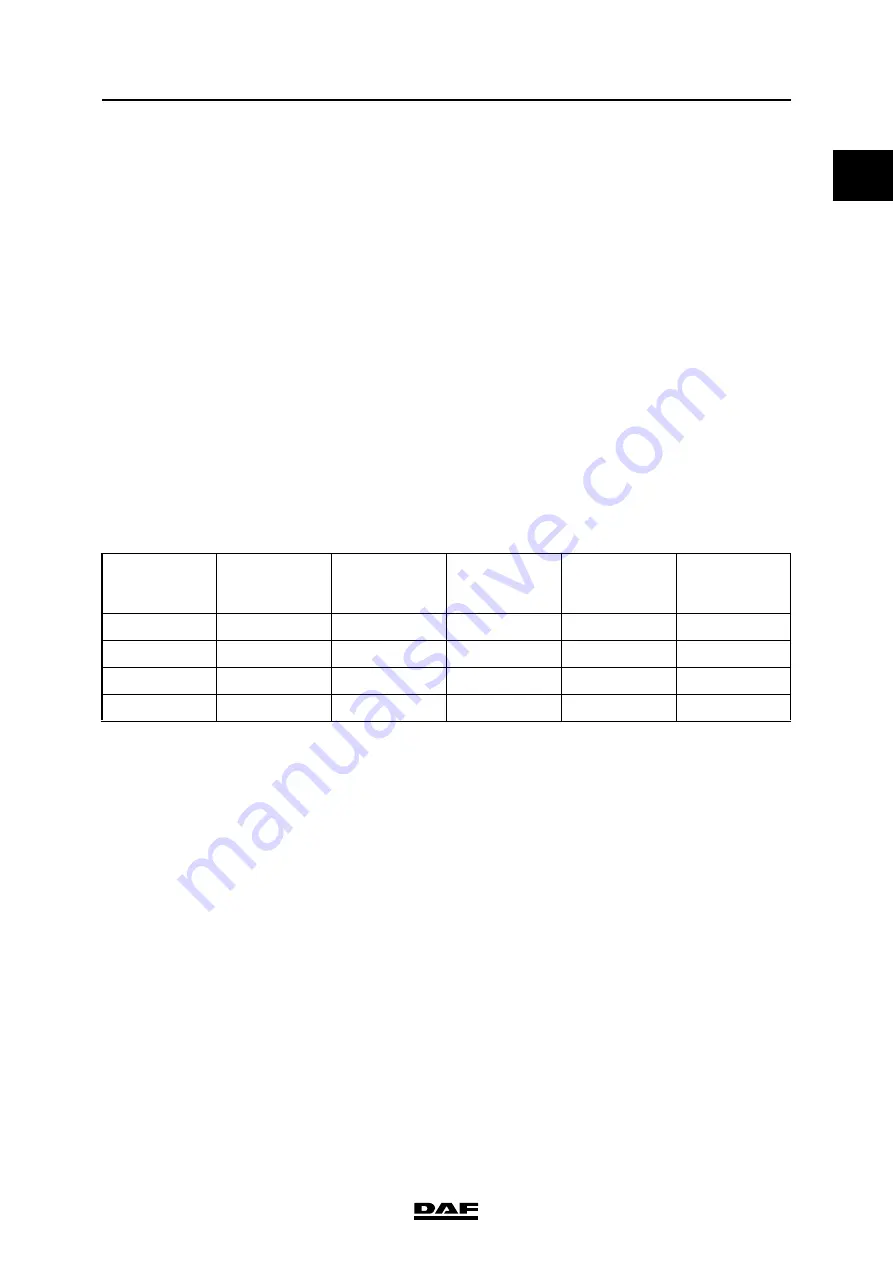
©
200416
6-1
XE engine fuel system
TECHNICAL DATA
ΧΦ65/75/85
series
4
0
6. XE ENGINE FUEL SYSTEM
6.1 GENERAL
Gallery pressure
Fuel level element
Overview of injectors
Fuel lift pump
Pump housing
At starting speed
approx. 0.5 - 1.0 bar
At idling speed
approx. 2.5 - 3.0 bar
At maximum no-load engine speed
approx. 6.5 - 7.0 bar
Angular displacement
86
Resistance value
- Full
approx. 500
-
•
approx. 355
-
∂
approx. 234
-
approx. 137
- Not used
approx. 33
Vacuum relief valve opening pressure
10 - 20 mbar
Pressure relief valve opening pressure
200 - 300 mbar
Engine type
Number of
holes in
injector
Nozzle no.
Hole diameter
Bar filter
Opening
pressure
XE 250 C1
8
1081
0.182
Yes
300 + 10 bar
XE 280 C1/C3
8
1081
0.182
Yes
300 + 10 bar
XE 315 C1/C3
8
1081
0.182
Yes
300 + 10 bar
XE 355 C1
8
1286
0.182
Yes
300 + 10 bar
Fuel lift pump pressure
7.0 - 8.0 bar
Pressure relief valve opening pressure
approx. 8.5 bar
Weight, including camshaft and pump units
approx. 70 kg
Pressure relief valve opening pressure
circa 5.5 - 6 bar
https://www.truck-manuals.net/
Содержание CF65
Страница 2: ...https www truck manuals net...
Страница 4: ...TECHNICAL DATA 2 200416 Contents 0 65 75 85 series 4 https www truck manuals net...
Страница 10: ...TECHNICAL DATA 1 6 200416 Engine general 0 65 75 85 series 4 https www truck manuals net...
Страница 14: ...TECHNICAL DATA 2 4 200416 CE engine fuel system 0 65 75 85 series 4 https www truck manuals net...
Страница 26: ...TECHNICAL DATA 7 4 200416 XE engine inlet exhaust system 0 65 75 85 series 4 https www truck manuals net...
Страница 30: ...DIAGNOSTICS 2 200416 Contents 1 65 75 85 series 4 https www truck manuals net...
Страница 32: ...DIAGNOSTICS 1 2 200416 Tractive problems 1 65 75 85 series 4 https www truck manuals net...
Страница 38: ...DIAGNOSTICS 2 6 200416 CE engine fuel system 1 65 75 85 series 4 https www truck manuals net...
Страница 50: ...DIAGNOSTICS 5 6 200416 Fuel system XE PE engine 1 65 75 85 series 4 https www truck manuals net...
Страница 56: ...DIAGNOSTICS 7 4 200416 Engine brake XE PE engine 1 65 75 85 series 4 https www truck manuals net...
Страница 58: ...CE ENGINE FUEL SYSTEM 2 200416 Contents 2 65 75 85 series 4 https www truck manuals net...
Страница 60: ...CE ENGINE FUEL SYSTEM 1 2 200416 Safety instructions 2 65 75 85 series 4 https www truck manuals net...
Страница 72: ...CE ENGINE FUEL SYSTEM 2 12 200416 General 2 65 75 85 series 4 https www truck manuals net...
Страница 92: ...CE ENGINE FUEL SYSTEM 4 14 200416 Inspection and adjustment 2 65 75 85 series 4 https www truck manuals net...
Страница 122: ...CE ENGINE FUEL SYSTEM 5 30 200416 Removal and installation 2 65 75 85 series 4 https www truck manuals net...
Страница 126: ...CE ENGINE INLET EXHAUST SYSTEM 2 200416 Contents 3 65 75 85 series 4 https www truck manuals net...
Страница 128: ...CE ENGINE INLET EXHAUST SYSTEM 1 2 200416 Safety instructions 3 65 75 85 series 4 https www truck manuals net...
Страница 132: ...CE ENGINE INLET EXHAUST SYSTEM 2 4 200416 General 3 65 75 85 series 4 https www truck manuals net...
Страница 140: ...CE ENGINE INLET EXHAUST SYSTEM 3 8 200416 Inspection and adjustment 3 65 75 85 series 4 https www truck manuals net...
Страница 152: ...CE ENGINE ENGINE BRAKE 2 200416 Contents 4 65 75 85 series 4 https www truck manuals net...
Страница 154: ...CE ENGINE ENGINE BRAKE 1 2 200416 Safety instructions 4 65 75 85 series 4 https www truck manuals net...
Страница 158: ...CE ENGINE ENGINE BRAKE 3 2 200416 Inspection and adjustment 4 65 75 85 series 4 https www truck manuals net...
Страница 160: ...CE ENGINE ENGINE BRAKE 4 2 200416 Removal and installation 4 65 75 85 series 4 https www truck manuals net...
Страница 162: ...PE ENGINE FUEL SYSTEM 2 200324 Contents 5 CF65 75 85 series 4 https www truck manuals net...
Страница 164: ...PE ENGINE FUEL SYSTEM 1 2 200324 Safety instructions 5 CF65 75 85 series 4 https www truck manuals net...
Страница 208: ...PE ENGINE FUEL SYSTEM 4 20 200324 Removal and installation 5 CF65 75 85 series 4 https www truck manuals net...
Страница 216: ...PE ENGINE INLET EXHAUST SYSTEM 2 200324 Contents 6 CF65 75 85 series 4 https www truck manuals net...
Страница 218: ...PE ENGINE INLET EXHAUST SYSTEM 1 2 200324 Safety instructions 6 CF65 75 85 series 4 https www truck manuals net...
Страница 222: ...PE ENGINE INLET EXHAUST SYSTEM 2 4 200324 General 6 CF65 75 85 series 4 https www truck manuals net...
Страница 236: ...ENGINE BRAKE PE ENGINE 2 200324 Contents 7 CF65 75 85 series 4 https www truck manuals net...
Страница 238: ...ENGINE BRAKE PE ENGINE 1 2 200324 Safety instructions 7 CF65 75 85 series 4 https www truck manuals net...
Страница 242: ...ENGINE BRAKE PE ENGINE 3 2 200324 Inspection and adjustment 7 CF65 75 85 series 4 https www truck manuals net...
Страница 244: ...ENGINE BRAKE PE ENGINE 4 2 200324 Removal and installation 7 CF65 75 85 series 4 https www truck manuals net...
Страница 246: ...XE ENGINE FUEL SYSTEM 2 200324 Contents 8 CF65 75 85 series 4 https www truck manuals net...
Страница 248: ...XE ENGINE FUEL SYSTEM 1 2 200324 Safety instructions 8 CF65 75 85 series 4 https www truck manuals net...
Страница 262: ...XE ENGINE FUEL SYSTEM 2 14 200324 General 8 CF65 75 85 series 4 https www truck manuals net...
Страница 302: ...XE ENGINE INLET EXHAUST SYSTEM 2 200324 Contents 9 CF65 75 85 series 4 https www truck manuals net...
Страница 304: ...XE ENGINE INLET EXHAUST SYSTEM 1 2 200324 Safety instructions 9 CF65 75 85 series 4 https www truck manuals net...
Страница 308: ...XE ENGINE INLET EXHAUST SYSTEM 2 4 200324 General 9 CF65 75 85 series 4 https www truck manuals net...
Страница 320: ...XE ENGINE INLET EXHAUST SYSTEM 4 8 200324 Removal and installation 9 CF65 75 85 series 4 https www truck manuals net...
Страница 324: ...XE ENGINE ENGINE BRAKE 2 200324 Contents 10 CF65 75 85 series 4 https www truck manuals net...
Страница 326: ...XE ENGINE ENGINE BRAKE 1 2 200324 Safety instructions 10 CF65 75 85 series 4 https www truck manuals net...
Страница 342: ...XE ENGINE ENGINE BRAKE 2 16 200324 General 10 CF65 75 85 series 4 https www truck manuals net...
Страница 352: ...XE ENGINE ENGINE BRAKE 4 6 200324 Removal and installation 10 CF65 75 85 series 4 https www truck manuals net...