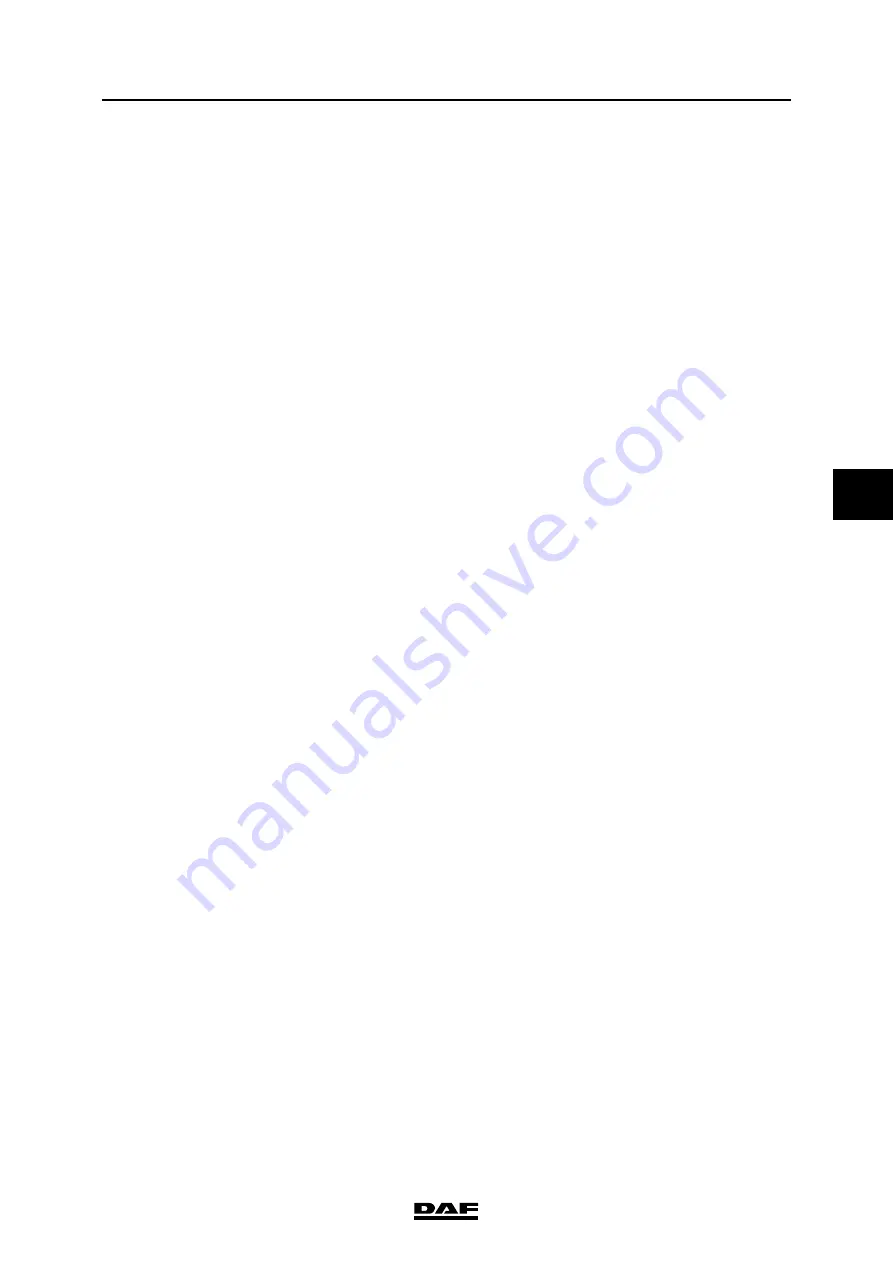
©
200518
3-11
Inspection and adjustment
EXPLANATORY NOTES ON THE MAINTENANCE ACTIVITIES
ΧΦ65/65
(II)
series
5
3.11 CHECKING FOR FUEL LEAKS
1.
Visually inspect all hose connections and
fuel system components for leaks.
3.12 CHECKING THE COMPONENTS AND HOSE CONNECTIONS FOR LEAKS
1.
Check all hose connections and cooling
system components for leaks.
2.
Check the hose connections and inlet
system components.
3.13 CHECKING THE EXHAUST SYSTEM
1.
Visually inspect the exhaust system for
leaks.
2.
Check the exhaust suspension points.
3.
Check that no heat transfer (due to
accumulated dirt, for example) can take
place to the exhaust system area, such as
pipes, components etc.
https://www.truck-manuals.net/
Содержание CF65
Страница 1: ...Maintenance manual CF65 CF65 II https www truck manuals net...
Страница 2: ...https www truck manuals net...
Страница 4: ...https www truck manuals net...
Страница 6: ...https www truck manuals net...
Страница 8: ...TECHNICAL DATA 2 200518 Contents 0 65 65 II series https www truck manuals net...
Страница 12: ...TECHNICAL DATA 2 2 200518 Steering gear and brake system 0 65 65 II series https www truck manuals net...
Страница 18: ...THREADED CONNECTIONS 2 200518 Contents 2 65 65 II series https www truck manuals net...
Страница 22: ...FLUIDS OIL AND LUBRICANTS 2 200518 Contents 3 65 65 II series https www truck manuals net...
Страница 24: ...FLUIDS OIL AND LUBRICANTS 1 2 200518 Specifications 3 65 65 II series https www truck manuals net...
Страница 26: ...MAINTENANCE SCHEDULE 2 200518 Contents 4 65 65 II series https www truck manuals net...
Страница 36: ...MAINTENANCE SCHEDULE 2 6 200518 Maintenance activities 4 65 65 II series https www truck manuals net...
Страница 112: ...EXPLANATORY NOTES ON THE MAINTENANCE ACTIVITIES 6 6 200518 Cleaning 5 65 65 II series https www truck manuals net...
Страница 114: ...EXPLANATORY NOTES ON THE MAINTENANCE ACTIVITIES 7 2 200518 Lubrication 5 65 65 II series https www truck manuals net...
Страница 115: ...https www truck manuals net...
Страница 116: ...Printed in the Netherlands DW13280404 English https www truck manuals net...